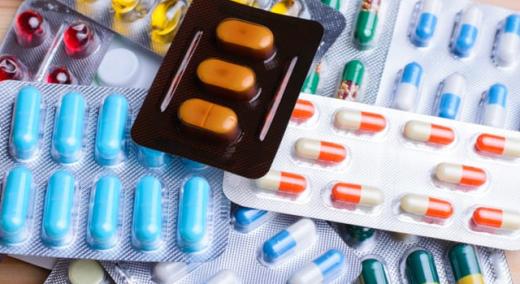
If you were to contact a group of recycling professionals, as one recent survey did, and ask them to list all the ways that consumer product manufacturers drive them crazy, you’d probably hear a lot about “shrink sleeves”—those full-body, shrink-to-fit plastic labels found on beer cans, yogurt containers, and any number of other items.
ADVERTISEMENT |
Because these sleeves fool the infrared sensors that are supposed to identify plastics by polymer type in recycling facilities (see “Recycling meets reality”), it becomes difficult to sort the items correctly. And that can lead to all kinds of downstream contamination issues for the recycling facilities that are supposed to turn bales of “sorted” plastic and cans into reasonably pure materials for new products.
…
Add new comment