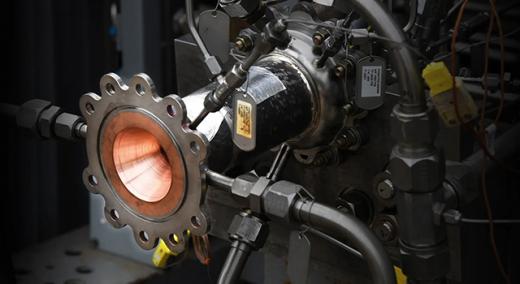
Historically, manufacturing processes have often involved substantial waste. From the early days of industrialization, companies have prioritized production speed and volume over efficient resource use. As resources seemed abundant and environmental consciousness was low, excessive waste became an accepted cost of business.
ADVERTISEMENT |
In recent years, there’s been a notable shift in manufacturing practices. Driven by global awareness of climate change and dwindling resources, companies have begun to prioritize sustainability. This shift not only reflects a commitment to ethical operations but also a response to consumer demands for environmentally responsible products.
The consequences of waste in manufacturing
Waste in the manufacturing sector leads to severe environmental consequences. Excessive material waste contributes to landfill overfill, while energy waste increases greenhouse gas emissions. Furthermore, water pollution from untreated industrial waste affects aquatic life and human health.
…
Add new comment