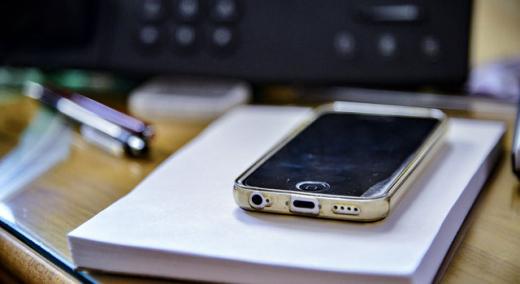
How often do you check your phone at work? Maybe you’re reading this article on it right now (Don’t worry; we won’t tell.). Smartphones were a revolution for workplace distractions, but they can also be tools for productivity.
ADVERTISEMENT |
I recently attended the IBM Watson IoT Exchange event in Orlando, Florida, the AI giant’s annual conference for its Watson solutions. It brings together users and developers of multiple IBM IoT products, including Maximo enterprise asset management.
As I attended the keynotes and workshops of the Maximo stream, I noticed a trend: Several of the featured monitoring, analytics, and asset management solutions required or recommended the use of a consumer electronic device, such as a smartphone, consumer tablet, or augmented reality headset.
…
Add new comment