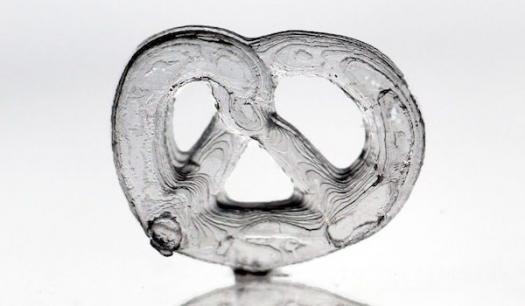
Karslruhe Institute of Technology
Complicated high-precision structures made of glass, like this pretzel, can be manufactured in a 3-D-printing process developed at Karslruhe Institute of Technology.
Almost two years ago, Micron3DP demonstrated one of the earliest forays into 3D printing with glass. Just a few months later, MIT backed up glass’s place in the additive manufacturing realm and showed just how beautiful the possibilities were.
ADVERTISEMENT |
Although intriguing, those early demonstrations were only able to produce rather imprecise glass components with poor resolution (on the order of millimeters) because they printed in molten glass.
Although that’s good enough for glass vases, bowls, and other artistic expressions, it just doesn’t cut it for the wide range of high-tech applications of glass that require intricate and precise microstructures.
…
Add new comment