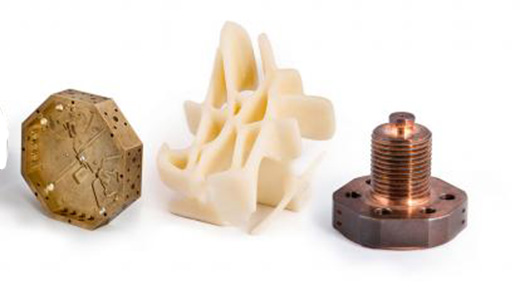
This story was originally published by Knowable Magazine.
Part one looked at the innovative possibilities inherent in 3D printing; here we consider some of its shortcomings and the solutions that companies are finding.
A few years into this century, the industry reached a tipping point, as sales of all kinds of 3D fabricators and raw materials began to accelerate substantially. One impetus was simply the passage of time: Because U.S. patents generally last for only 20 years, the ones granted during that first flurry of 3D printing during the 1980s were beginning to expire.
ADVERTISEMENT |
…
Add new comment