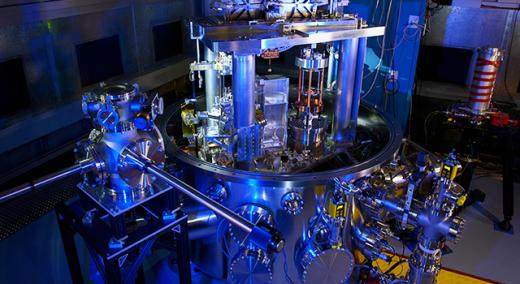
Alot has changed at the National Institute of Standards and Technology (NIST) during the past 120 years. For one thing, we were known as the National Bureau of Standards for the first 87 years of our existence. Then, in 1988, we became the National Institute of Standards and Technology (NIST), to reflect our agency’s expanding mission and a renewed emphasis on boosting the competitiveness of American industry.
ADVERTISEMENT |
But as much as things change, they also stay the same. While much of our early work has been baked into the American economy, NIST continues to be a world leader in advancing measurement science. We still provide many of our original services, though the techniques and technologies have evolved.
…
Add new comment