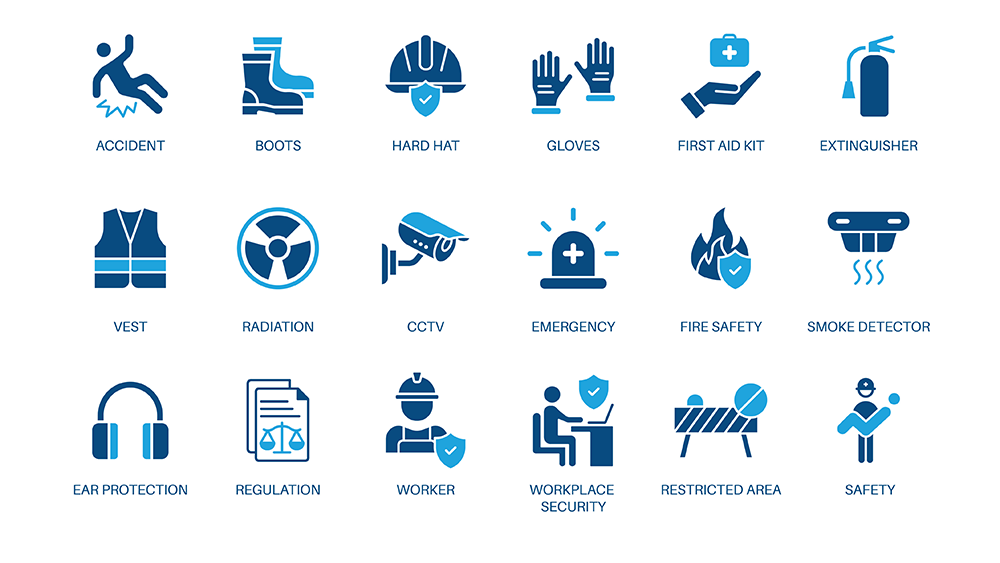
Adobe Stock
The workplace has changed forever, having gone through a revolution similar to the Industrial Revolution. Our workplaces are diverse, complex, and frequently changing. If we take any lesson from the Covid pandemic, it’s that the way we work, where we work, and how we work have fundamentally shifted.
ADVERTISEMENT |
Likewise, we’re altering the way we manage workplace hazards. How we assess hazards, manage risks, and communicate about them and their control measures have changed. This revolution is enabled by technology, specifically mobile technology.
Why managing workplace hazards is important
Understanding workplace hazards and having effective controls for them is a basic right for all employees and the responsibility of every employer. Here are a few tips that have helped me manage workplace hazards. The goal is simple: Workplaces should be safe, healthy environments where human ingenuity and creativity can flourish.
…
Add new comment