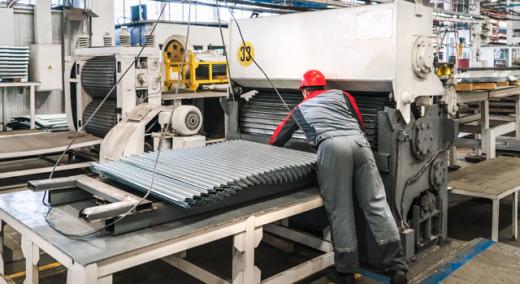
In the quickly changing industrial landscape, firms continue to place a high premium on safety. Innovative approaches to improving industrial safety have been made possible by technological advancements. One particularly revolutionary option is computerized maintenance management system (CMMS) software. This article examines how CMMS software transforms safety procedures in industrial settings, providing instances of its effective application in the real world.
ADVERTISEMENT |
Proactive asset management and equipment monitoring
A well-implemented CMMS software serves as the foundation of asset management, transforming how important equipment and machinery are maintained and monitored. CMMS can detect possible equipment faults before they occur by using predictive maintenance algorithms and real-time sensor data integration. This proactive method reduces safety hazards associated with unexpected breakdowns, maintaining continual equipment reliability and protecting workers’ well-being.
…
Comments
https://www.qualitydigest.com/user/125595
A Computerized Maintenance Management System (CMMS) helps streamline asset tracking, preventive maintenance planning, and work order management to reduce downtime and extend equipment life. Top CMMS software like UpKeep and IBM Maximo offer mobile-friendly solutions for maintenance scheduling, inventory control, and KPI tracking. Whether you're exploring CMMS meaning, comparing CMMS vs EAM, or searching for the best free CMMS programs, this guide covers it all.
WEBSITE:https://ids.tech/
Add new comment