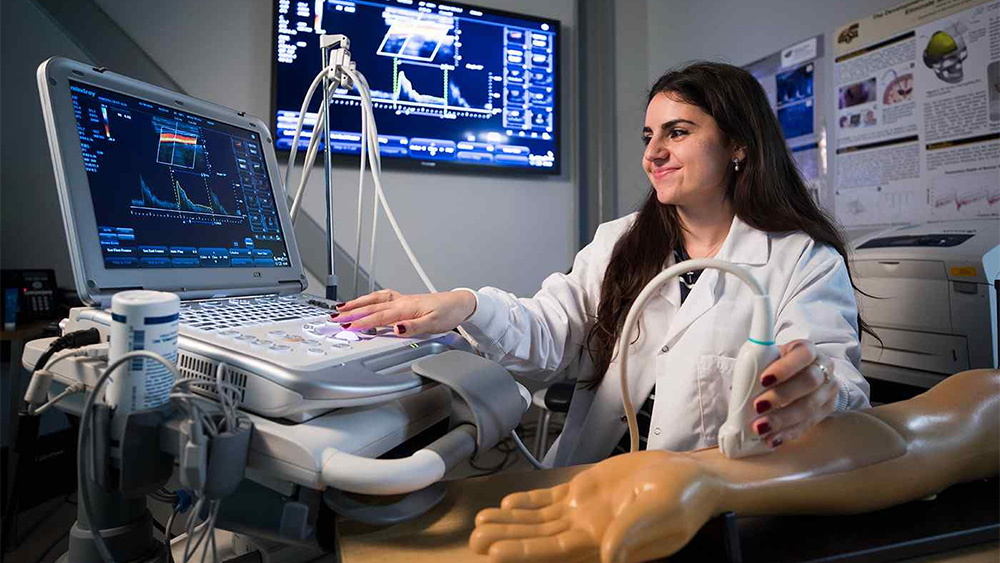
Wichita State University
Successfully run medical device companies are cross-functional. From product development, manufacturing, quality, and regulatory compliance, to marketing and sales, every business operation works together to produce and sell medical devices that improve the lives of end users. Still, many medical device companies struggle to embrace the mentality that quality is a shared responsibility across the entire organization.
ADVERTISEMENT |
The best-of-breed medical device businesses have embraced the idea of “true quality” within every aspect of their business. They realize creating a foundation of true quality is not just the quality department’s responsibility.
Unfortunately, the quality creation function is more often viewed as a hurdle to overcome when completing tasks, and this mindset leads to several myths about quality.
Here are three of the most common myths engineers believe to be true about quality along with how to eliminate these unfounded beliefs from emerging within your organization.
…
Add new comment