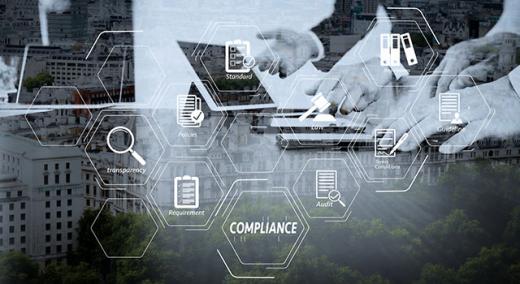
Demonstrating identification and traceability in all quality system processes is a must for medical device companies to comply with FDA regulations. To satisfy this compliance need, companies will need to connect related processes within their quality system to close the loop between related pre- and post-market activities and processes. That’s what’s known as closed-loop traceability (CLT).
ADVERTISEMENT |
With a global regulatory emphasis on CLT, it’s up to medical device companies to ensure their systems can keep pace with this expectation. More devices of increasing complexity are hitting the market, challenging companies to maintain clear documentation and traceability in real time. Failing to do so hampers a company’s overall efficiency—not to mention exposes it to penalties, fines, and operational disruptions.
Fortunately, medical device companies have access to modern QMS solutions that increase the accuracy and speed of demonstrating CLT, creating opportunities not only to stay compliant but also improve their operations and competitive edge in the market.
…
Add new comment