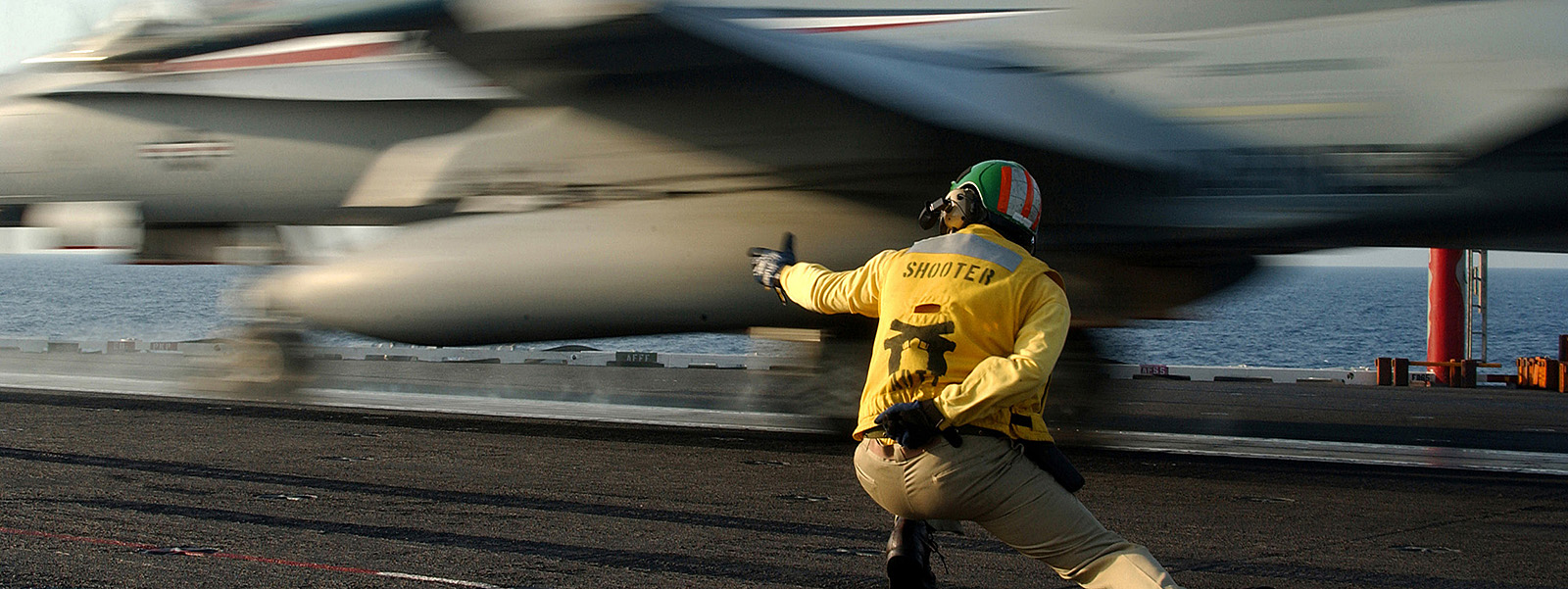
Many industries have no clear boundary between safety and quality culture. In fact, they are often closely integrated. Quality failures and nonconformances that require rework have been correlated with increased accidents and recordable injury rates in manufacturing organizations. These injuries are frequently the result of fatigue, workplace pressure, and the pressure from extra work due to quality failures.
Among the important elements of people, processes, and tools, people are the primary point of failure in increasingly automated systems. Unlike machines, we are subject to fatigue, information overload, and stress that can have a serious impact on our ability to work safely and efficiently. However, people are also where dynamic sense-making, decision-making, and situational awareness reside, which are vital ingredients in complex and high-reliability organizations (HRO).
The aviation industry represents the best example of an HRO, in which automated systems such as navigation and air traffic control are integrated with highly developed human competencies. As a result, the industry sees an extremely small number of safety violations relative to the millions of hours of commercial aviation operation annually.
HRO cultures are built on the same fundamental principles that support healthy quality and safety cultures. In everyday operations, HROs are sensitive to minor fluctuations and behavioral deviations so that they can detect and correct them before they cascade into major failures. They continuously refresh and update their knowledge of the system to anticipate and prevent future failures. In a crisis, HROs combine standard operating procedures (SOPs) and adaptive behavior with on-the-spot sense-making and organizing. Workers are empowered to assess the situation while simultaneously acting to correct failures and protect the system.
The Deepwater Horizon disaster in the Gulf of Mexico in 2010 catalyzed the study of safety and quality culture in the petroleum industry. In 2011, the Deepwater Horizon Study Group from the Center for Catastrophic Risk Management reported that the organizational culture of both BP and the Deepwater Horizon offshore drilling rig had been a contributing factor to the disaster, which added considerable urgency to understanding how and why this was the case.
HROs, like oil rigs, face the challenge of trying to integrate increasingly autonomous technology with human workers that remain prone to fatigue, sub-optimal behavior, and other factors that can lead to poor decision-making and compromised safety. Crew resource management (CRM) has emerged as a method for creating a work environment for HROs where there are rigid and standardized roles. This enables workers to operate with a high degree of precision, while remaining flexible and dynamic enough to adapt quickly to rapidly changing situations, particularly in a crisis.
Culture is therefore an integral element of every organization. In the new Intelex Insight Report, “Quality and Safety in Organizational Culture: A Cross-Industry Look,” you’ll explore the nuclear energy, construction, petroleum, and healthcare industries to learn:
• How people continue to be vital elements of software-dominated systems.
• How complex systems breed complex problems that defy simple solutions.
• How standards such as ISO 9001:2015 and industry-specific frameworks can guide organizations in their quest for better safety and quality cultures.
• How communication, leadership engagement, and situational awareness are the building blocks of strong organizational culture in every industry.
Add new comment