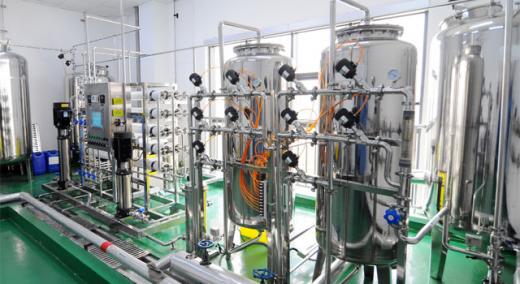
Following any tech transfer project, the subsequent startup of the manufacturing line is almost always full of challenges. The goal is to start up as soon as possible once the project is completed but also to achieve steady-state throughput as quickly as possible after the startup begins. This type of startup is what is called a vertical startup.
ADVERTISEMENT |
In practice, vertical startups are rare because management teams typically focus their attention on having the facility and the equipment qualified in time to meet the process qualification milestone. The consequences of this thinking is that a broad range of workstreams are often neglected or receive inadequate attention although they are critical to startup. Workstreams like staffing, training, procedure development, supply chain, analytical methods, etc. must all be ready to go by this important milestone. The result can be like having perfectly tuned race cars lined up on the starting line of a Formula 1 race, but with untrained drivers, little gas, unpracticed pit crews, and no spare parts.
…
Add new comment