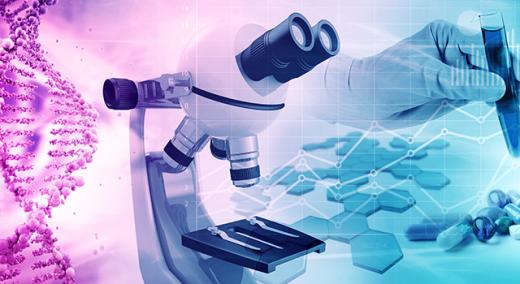
The pharmaceutical industry has seen significant upheaval and disruption during the past several years. These changes are due in part to the impacts of Covid—for example, interruptions in the supply chain and overwhelming market demand for shortened production times.
ADVERTISEMENT |
They are also being driven by extensive shifts in emergent digital technologies, a need for deep predictive data insights, and a cultural demand for personal and system connectivity. Add to this list a shifting regulatory environment with an increased focus on personal responsibility for auditing and risk management. New opportunities and responsibilities can seem overwhelming.
However, the bright side of assuming personal responsibility is the self-determination it allows. Businesses that make innovative changes amidst upheavals and downturns actually gain momentum and outperform competitors upon recovery. What sets apart thriving pharma businesses is their willingness to spot the market shifts as they begin to crest, pivot to align with them, and then swim through deep waters to ultimately catch and ride the wave. Their adaptive autonomy allows them to absorb disruptions and modify in company-specific ways to move through them.
…
Add new comment