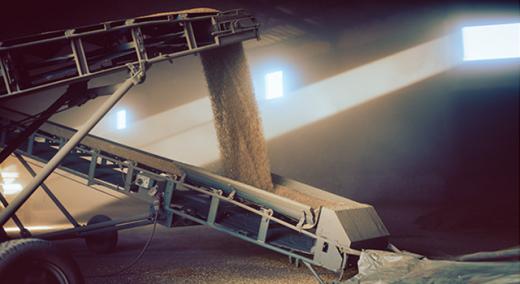
For owners and operators in the agricultural and food-processing industries, Jan. 1, 2022, was the deadline for completing a dust hazard analysis (DHA) for existing facilities in accordance with Chapter 7 of the National Fire Protection Association’s Standard 61 (2020) for the Prevention of Fires and Dust Explosions in Agricultural and Food Processing Facilities.
ADVERTISEMENT |
NFPA 61 and other related NFPA standards detail essential strategies and procedures for protecting people, processes, and property from the hazards presented by fires and dust explosions in facilities handling, processing, and storing bulk grains such as corn, wheat, oats, barley, sunflower seeds, soybeans, their byproducts, and other agriculture-related combustible dusts. All new processes and facilities handling and generating combustible dusts are now required to perform a DHA.
Appendix F of NFPA 61 (2020) provides a comprehensive checklist that serves as a blueprint for generating a DHA. This checklist includes evaluating the dust explosion protection for process equipment that can often be at risk, such as bucket elevators, conveyors, grinders, silos, and systems for spray-drying and dust collection.
…
Add new comment