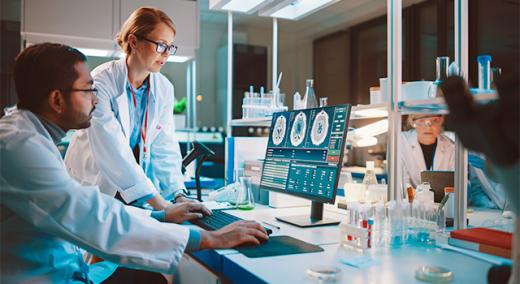
Since 2010, citations for insufficient corrective action and preventive action (CAPA) procedures have been at the top of the list of the most common issues within the U.S. Food and Drug Administration (FDA) inspections, particularly for the medical device industry. Issues can occur while manufacturing medical devices or pharmaceuticals, and when they do, companies must ensure they take all necessary steps to identify and resolve the issue and, importantly, work to prevent it from reoccurring.
ADVERTISEMENT |
These problems can be solved with CAPA systems. CAPA processes are necessary to maintain and improve the quality of products as well as to remain compliant with regulations. They provide structure for finding and solving the root cause of an issue. The intent of the CAPA process is to assist medical device or pharmaceutical companies in eliminating nonconformities, deviations, or complaints. Noncompliance can also present itself in the form of quality management system (QMS) or process failures.
…
Add new comment