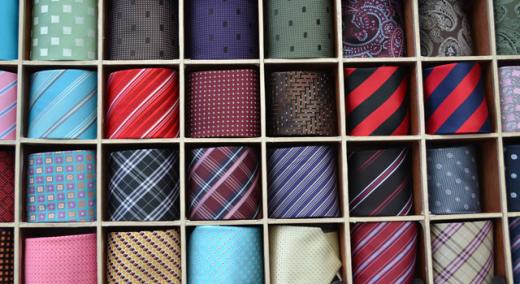
As customer demands for more customization and choice increase, the complexity of products and associated product design, manufacturing, and sales processes also increase. Product life cycles are also getting shorter, requiring a constant flow of new products with high-value features and capabilities.
ADVERTISEMENT |
This challenges product design and engineering processes to become leaner, faster, and more inclusive. Addressing and managing complexity is a key success factor. The challenge can be tackled using a three-pronged approach that includes increased collaboration, greater integration, and the use of a configuration life-cycle management system.
Integrating key IT systems
One of the most significant hindrances to companies today is their siloed systems. You might have a product life-cycle management (PLM) system in the engineering department, a customer relationship management (CRM) system on the sales side, and an enterprise resource planning (ERP) system on the manufacturing side. These different systems often don’t talk to one another.
…
Add new comment