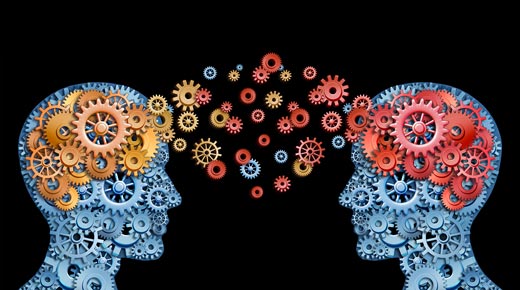
Does your organization benefit from lessons learned? Does it learn from previous quality issues? A vast amount of learning takes place every day in every manufacturing facility. Do global manufacturing companies share experiences gained from resolving quality issues between overseas plants? And what will they gain if they do?
ADVERTISEMENT |
What is lessons learned?
In project management nomenclature: Lessons learned is the learning gained from the process of performing the project. We learn from our own project experiences as well as the experiences of others. Sharing lessons learned among project team members prevents an organization from repeating the same mistakes and also allows it to take advantage of organizational best practices. Learning should be deliberate. Organizations should be prepared to take advantage of the key learning opportunities that projects provide. Unfortunately, capturing lessons learned too often is seen as optional… if time permits.
…
Add new comment