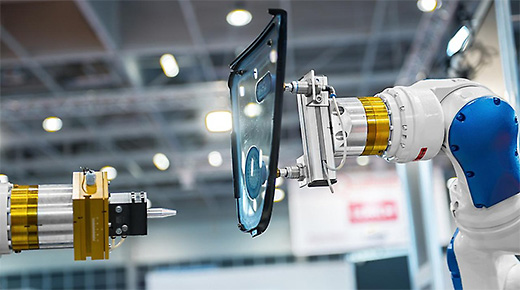
Cost of quality (CoQ) is certainly not a new topic. It was first described in 1956 by American quality control expert Armand V. Feigenbaum in a Harvard Business Review article. As you likely already know, CoQ consists of four categories: internal and external failures, and appraisal and prevention activities. It sounds easy to measure, but as you also likely know, it isn’t.
ADVERTISEMENT |
One of the reasons CoQ is so hard to nail down is because of hidden costs associated with poor quality. The information we need is often siloed within departments other than quality. Other times, the information we need lies stranded outside of our organizations among supply chain, R&D, and commercial partners. Worse yet, what if we don’t even know what information we need? Conversely, what if we know the information we need, but it’s not being captured?
…
Add new comment