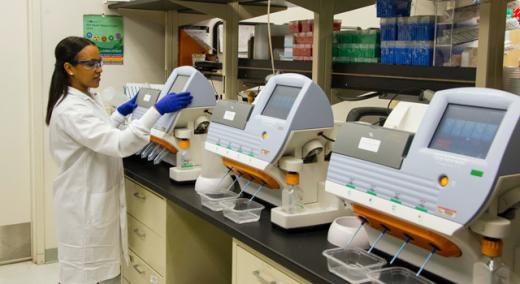
Photo by National Cancer Institute on Unsplash
The goal of your MedTech company’s supplier management process should be to ensure a consistent supply of high-quality parts and components that conform to your specifications.
ADVERTISEMENT |
But achieving that goal is easier said than done, and it depends heavily on whether you take a risk-based approach to your supplier management activities.
A proactive, risk-based supplier management process will take into account both the risks to your devices and the risks to your business in general. In other words, it will ensure that the decisions you make regarding your suppliers have the minimum impact on your business and the safety and efficacy of your devices.
Every company is different, but there are some standard practices and ways of approaching supplier management that you can use to make sure you account for risk at every step.
…
Comments
Managing Supplier Risk Begins With Defining the Risk
Many medical device suppliers currently use Design FMEAs and Process FMEAs. Some do them correctly and some do not. When these documents are done correctly by your supplier, they give you tremendous insight into your suppliers design and manufacturing risk.
I once gave a talk for ASQ on how one can audit these documents and the additional risk documents which they drive (Design Verfication Plan, Design Validation Plan, Process Control Plan and Process Validation Plan) very quickly (< 20 minutes each per Design FMEA and Process FMEA). When the Design FMEA and Process FMEA are done correctly and properly linked to the other risk documents they drive, they define the sources of the current risk with the supplier and current risk controls being used by them to control them. If your supplier is performing the Design FMEAs and Process FMEAs incorrectly, you know there is very likely major supplier risk present and the supplier has no idea what it is.
Any management of risk at the supplier must begin with an audit of the suppliers risk management documents.
Supplier risk
Agreed Richard. Mind, it a little sub-optimal if the supplier has not have an accredited certified QMS and even worse if it is not documneted by their business processes but simply direct copy of the ISO 9001 QMS Clauses. The PFMEA is populated as per the AIAG FMEA text guides, the Flow Process Chart and each step is the direct input to the PFMEA - line by line, not column of course. Then the highest risk is placed in a PCP etc. Process Layered Audits (Automotive) or PEAR (Aerospace) along with Internal Audits of the procedures in the Process to meet the Organization's Mgt System requirements and then, to the requirements of the seelected and certified International Standard (Say ISO 9001 etc).
Add new comment