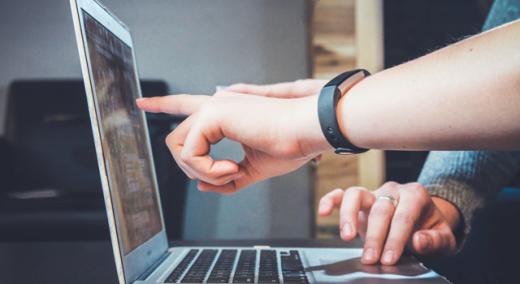
Photo by John Schnobrich on Unsplash.
In a highly regulated industry like medical technology, manufacturing processes must undergo either process verification or process validation to ensure they’re consistently producing the correct result. The question is, which one should you use?
Verification and validation are two different activities, and they’re used under different circumstances. Knowing when to validate or verify a process is essential from both a quality and regulatory perspective.
So, let’s take a look at what process verification and process validation refer to, and when you should use each of them in medical device manufacturing: What’s the difference between process verification vs. process validation?
…
Comments
Verification - Sample Plans
If a feature can be verified, but you do less than 100% verification using a sampling plan, does the process still require verification? This is a source of debate at our facility. Some features can be verified/measured and the sample is indicative of the process yield. The differing schools of thought are verification in lieu of validation is 100% verification of the feature(s). Validation should be performed for processes as cited in the guidance and this article, but also for any features that are sampled (not 100%). Another thought was that a simple process capability study versus a full-on IQ/OQ/PQ validtion can be used.
Clarification
So, is Verification the assessment of the process output relative to its specs? Is validation assessment that the process procedures are being followed, because the output might be difficult or perhaps even impossible to verify? Or am I still missing the point?
THX
I don't get it.
I am more confused about validation vs. verification than I was before I read this article, and I want to explain why because I think I am the intended audience for this article, but it just did not give me the clarity promised.
Verification: “confirmation by examination and provision of objective evidence that specified requirements have been fulfilled.”
Validation: “establishing by objective evidence that a process consistently produces a result or product meeting its predetermined specifications.”
Distinction: "At first glance, this looks very similar to the definition for verification. However, process validation doesn’t measure or test a final product against specifications, like when you verify a process is working correctly."
Validation is the only definition that includes the word "product," so this immediately threw me for a loop, because given these two nearly-identical definitions, I struggled to find the relevant distinctions, and the only distinction called out here is one that appears to go in the opposite direction when I look at the definitions. There are other distinctions, not examined in the article, which also seem like they might matter: "have been" versus "consistently produces"; and "establishing" versus "confirmation."
Based on the rest of the article, the most relevant distinction I could grab onto was whether a characteristic had to be confirmed via destruction of the part or not. But something in my brain says that just can't be right. Whether I destroy 1000 batches of product to confirm its characteristics, or I test samples of each batch and confirm a state of statistical process control, it seems like either definition could fit either of these activities, but one of them seems more like validation than the other, and it is the use of SPC—not the nondestruction of product—that seems like the relevant distinction in this example because it speaks to the "consistently produces" verbiage of validation's definition.
I was hoping for a framework for understanding the distinction, but I'm left with my initial impression: similar but different and closely-related activities whose details are the purview of people other than me.
Add new comment