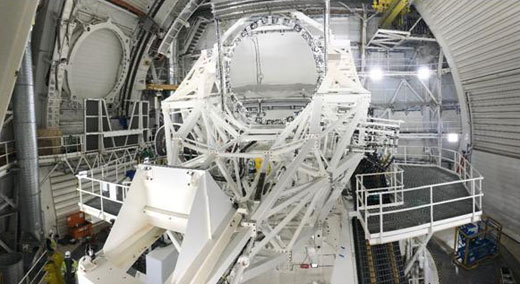
The Daniel K. Inouye Solar Telescope (DKIST) is strategically constructed on the summit of Haleakala, 10,023 ft above sea level, which is an ideal vantage point for solar observations. Site construction started in 2012 and moved into the integration, testing, and commissioning (IT&C) phase during the summer of 2019. DKIST will reveal features three times smaller than anything we can see on the Sun today and will do so multiple times a second.
ADVERTISEMENT |
Mounted on the telescope mount assembly (TMA) and measuring in at 4 m is the world’s largest off-axis parabolic primary mirror along with five other feed optics and the thermal system. Following the TMA is the rotating coudé laboratory, which houses the scientific instruments. All of the aforementioned elements need to be optically aligned as well as mechanically aligned to the mechanical axis of the TMA, a theoretical location whose location and motion is derived by solar altitude and azimuth. Using today’s laser tracking technologies and metrology software has made it possible to survey and interpret large articulating mechanical structures like DKIST’s telescope mount, optics, and thermal systems.
…
Add new comment