All Features
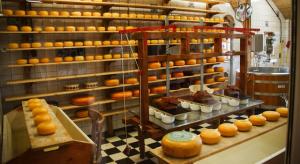
Dileep Thatte
According to information from the Centers for Disease Control and Prevention (CDC), every year 48 million people in the United States get sick, 128,000 are hospitalized, and 3,000 die from foodborne diseases. That means one in six people in the United States get sick from contaminated food every 12…
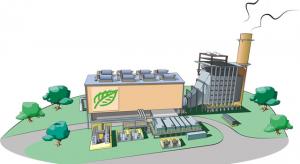
William A. Levinson
How will the United States’ withdrawal from the Paris Agreement affect greenhouse gas emissions? Quality Digest editor in chief Dirk Dusharme and Mike Richman, principal at Richman Business Media Consulting, point out that most manufacturers already recognize that waste, including waste of energy…
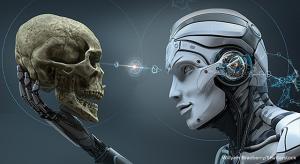
Kartik Hosanagar
Much has been written about the challenges associated with AI-based decisions. Some documented failures include gender and race biases in recruiting and credit approval software; chatbots that turned racist, and driverless cars that fail to recognize stop signs due to adversarial attacks;…
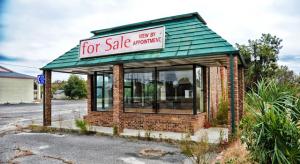
Frances Brunelle
Just as baby boomers on the manufacturing plant floor are getting ready to retire, so are the owners. More than 5,000 small manufacturing operations (with annual revenues between $2 and $20 million) will either close their doors or find new owners during the next five years.
Some of these owners…
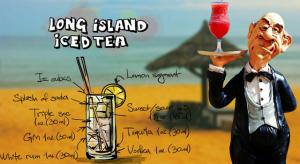
Anjalika Singh
Management system implementation reminds me of the advice my gym instructor gave when I first enrolled at my local health club: “Losing weight doesn’t happen in one day and with crash diets,” he said. “You gotta work out, gotta sleep the right amount, have a little fun in life. Yes, food is the…
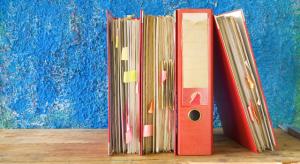
Inderjit Arora
Every company uses a system to understand the requirements and inputs of its customers, and then plans to deliver outputs meeting those requirements as a conforming product or service. The International Organization for Standardization (ISO) publishes management system standards that, when…
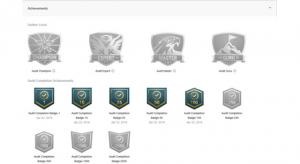
Paul Foster
When Deloitte wanted to get people excited about employee training, the company decided to adopt a gamification strategy for its online training portal. Using elements like achievement badges, missions, and leaderboards, they achieved a 37-percent increase in participation.
And when Ford Canada…
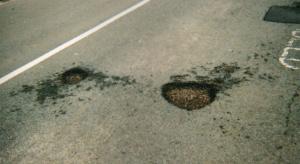
Jon Speer
Medical device manufacturers must implement and maintain a quality management system to ensure they are producing safe and effective medical devices. Created and maintained by the International Organization for Standardization (ISO), standard 13485 outlines the guidelines for medical device quality…
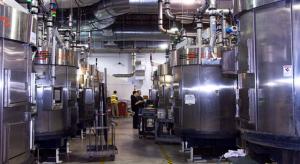
Eric Weisbrod
In manufacturing, standardization in production and process control leads to increased profitability and cuts down on many siloed problems that can plague even the most quality-focused organization. But when you have multiple, disparate plants around the country or the globe, standardization can…
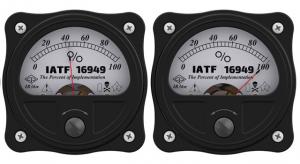
William A. Levinson
The martial arts rank, Shodan, for a first-degree black belt, does not mean “expert”; it means “first step.” ISO 9001:2015 is similarly a valuable and vital first step toward world-class performance, but it is only that—a first step. It covers only by implication many of the risks and opportunities…
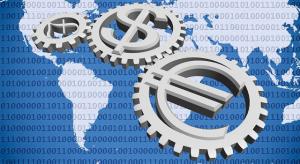
Jennifer Lopez
Globalization of the medical device market as well as its supporting supply chains continues to increase year after year. This has forced regulatory bodies to grapple with finding a way to narrow the gap between international and domestic regulation. In spring 2018 the United States Food and Drug…
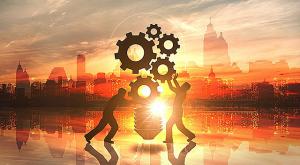
ISO
Innovation isn’t just about having a few bright ideas. It’s about creating value and helping organizations continuously adapt and evolve. ISO is developing a new series of International Standards on innovation management, the third of which has just been published.
Innovation is an increasingly…
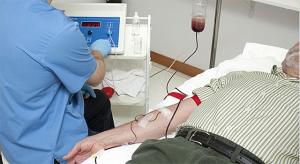
The FDA has announced an end to the alternative summary reporting (ASR) program for medical device manufacturers and will make the data publicly accessible.
The ASR program originally launched in 2000 when device manufacturers sought an “alternative summary” reporting exemption. ASR permitted…
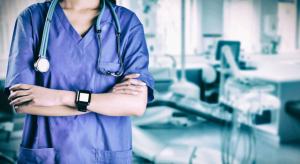
Grant Ramaley
Although the “new approach” to regulating medical devices has always given more urgency to higher-risk medical devices, this is not the case for the European Medical Device Regulation (MDR). Class 1 medical devices must fully comply with the regulation by May 26, 2020, or be shut out of the region…
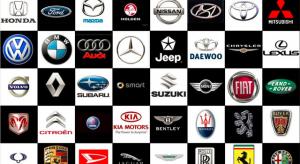
Chad Kymal, Gregory F. Gruska
During the early 1980s, GM, Ford, and Chrysler established the Automotive Industry Action Group (AIAG), a not-for-profit organization with the mission “To improve its members’ competitiveness through a cooperative effort of North American vehicle manufacturers and their suppliers.” In the late…
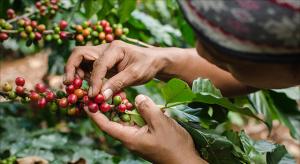
Jyoti Madhusoodanan, Knowable Magazine
A frog the size of a fingernail. A poncho-clad farmer leading his mule. A tree, some intertwining leaves, a silhouetted figure holding a pot. Such logos are stamped on labels of coffee, cocoa, mangoes, jeans, and myriad other products, certifying that the object for sale is in some way “sustainable…
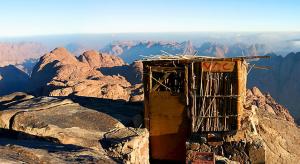
Well over half the world’s population does not have access to safe sanitation. For many people, this means the indignity and risks that come of having no toilets. The answer, it seems, lies in new sustainable treatment plants. The International Organization for Standardization (ISO) and the Gates …
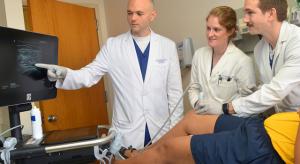
Jon Speer
The European Medical Device Regulation (MDR) is a new set of regulations that governs the production and distribution of medical devices in Europe, and compliance with the regulation is mandatory for medical device companies that want to sell their products in the European marketplace.
If your…
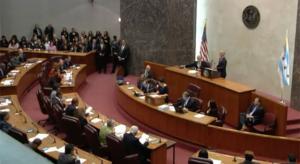
James J. Kline
The term “risk-based thinking” (RBT) is familiar to those in the quality profession. This familiarity comes in part from its inclusion in ISO 9001:2015, the International Organization for Standardization (ISO) quality management system standard. Although numerous articles and several books have…
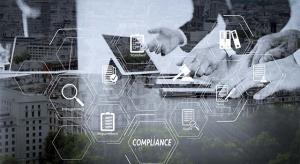
Ryan E. Day
In the article, “ANSI’s Role in the Wide World of Standards,” (Quality Digest, March 12, 2019), we looked at where standards originate and how companies are involved in developing them. In this article, we’ll outline four points that can help your organization integrate standards into your…
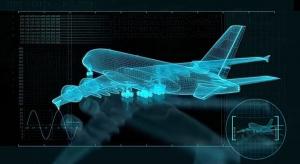
Ronda Culbertson
The AS9100 family of standards has completed very important updates, raising the business management quality bar again for aerospace and defense suppliers and OEMs. The transition to the new standards caught quite a few organizations somewhat flat-footed; particularly with the emphases on risk…
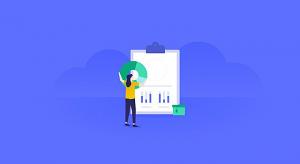
Harry Hertz
Recently I’ve seen some startling statistics from Gallup and Glassdoor about employee and customer engagement. I hope those statistics do not represent data from any organization you or I associate with. The actions of senior leaders, as well as setting the right focus on employees, can prevent…
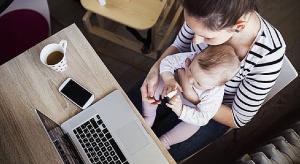
Alexandra Killewald, Xiaolin Zhuo
Almost 70 percent of American mothers with children younger than 18 work for pay, but motherhood remains disruptive for many women’s work lives.
American women earn almost 20 percent less per hour than their male peers, in part because women disproportionately take responsibility for raising…
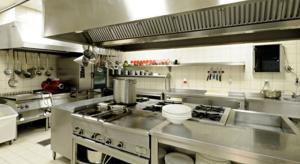
Brian S. Smith
Throughout my career, I have been a member of several trade organizations. I believe that standards have meaning, in every field. When I become a member of an organization, I endeavor to learn as much as possible.
For example, I belong to ASQ (American Society for Quality). I enjoy having…
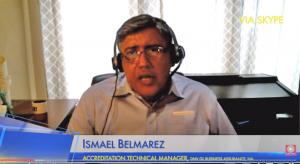
Ryan E. Day
According to the International Labor Organization, around the world every day 7,600 people die from work-related accidents or diseases—that’s more than 2.78 million people every year. To address the issue, the International Organization for Standardization (ISO) has developed a standard, ISO 45001…