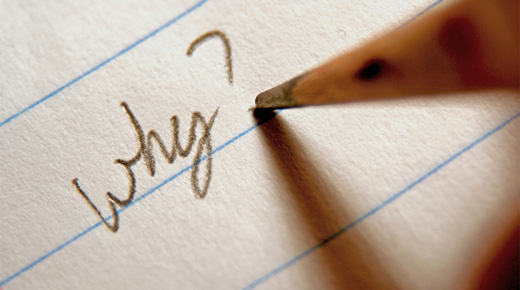
The 5 Whys is a well-known root cause analysis technique that originated at Toyota and has been adopted by many other organizations that have implemented lean manufacturing principles. Unlike more sophisticated problem-solving techniques, the 5 Whys doesn’t involve data segmentation, hypothesis testing, regression, or other advanced statistical tools; and in many cases can be completed without a data collection plan. By repeatedly asking the question “Why?” at least five times, you can successively peel away the layers of symptoms, which can lead to identifying the root cause of a problem.
…
Comments
Root Cause Analysis
Good article! I have been working on an article that, hopefully, will help teams avoid some of these pitfalls and still get some good utility out of root cause analysis. I have recently begun avoiding the term "root cause" in favor of "leverage point;" mostly because of the issue with interactions.
One bad thing about reading it online, though, was that for some reason a popup ad came up and couldn't be closed, so I had to read around that ad.
Pop-up
Rip. thanks for the feedback on the pop-up. A handful of people experienced the same problem and we think it has been fixed.
Root Cause Analysis with 5 Whys + A good well written Process
My experience has been that in trying to solve problems using root cause and the 5 whys will always work if you have a well written process description document
that everyone will use to guide their activities, and when you find that root cause or causes you make sure the document gets rewritten and that everyone is retrained on
the solution after being tested and verified. Too often this does not happen amongst all of the celabration.
5-Why Limitations
Excellent article, especially the part about using deductions to fill out the 5-Whys. I see that all the time.
You lost me on the last paragraph. You talk about countermeasures as actions to negate the root causes but not the symptoms. Based on that definition, the common term would be corretive action. I'm not sure the purpose of using a word different word than the one that's been in use for decades. I can't see any difference between corrective action and countermeasures. Can you expand on that?
Updated Reference
Enjoyed the article. Here is a link to the most recent TapRooT® Books (a series) that have been published in 2015-2018. See: http://www.taproot.com/store/Books/. For low to medium risk investigation the book to see is: http://www.taproot.com/store/TapRooT-and-reg-investigation-Essentials-Book-set.html. For major investigations, the book to see is: http://www.taproot.com/store/TapRooT-and-reg-Major-Investigations-Book-Set.html. Or you can get them as a set at: http://www.taproot.com/store/TapRooT-and-reg-minor-to-Major-Investigations-Book-Set-NEW-MAJENG-11.html.
Thanks
Mark
Add new comment