by Sidney Vianna
Few industry sectors require the consistent level of safety and reliability found in commercial aviation. Societal acceptance of avoidable aviation accidents will continue to decrease. All the stakeholders in this economic sector understand the need for passengers to feel as safe as possible when boarding an aircraft. Regulatory agencies such as the Federal Aviation Administration have been established to oversee and regulate organizations involved with all aspects and facets of flight safety. Some of the most important, influential and visible stakeholders involved in flight safety are the so-called "repair stations." Repair stations vary tremendously in size and scope of activities. Some large repair stations provide the daily work necessary to keep an airline's fleet operating. Others perform substantial maintenance, which might include more thorough inspection and repairs on airframes and overhauls of highly complex pieces of hardware, such as aircraft engines. Some repair stations offer specialized services for their customers, such as welding, heat treating and coating on a variety of aircraft parts. However, the vast majority of repair stations perform maintenance on components, and are normally remote from airports and hangars.
FAA and other national aviation authorities (e.g., NAA) oversight of certified repair stations require a tremendous amount of resources centered around personnel with a high degree of specialized knowledge about manufacturing and repair processes, material technology, regulations, quality control techniques and much more. Like many other federal agencies, the FAA has a limited budget, and the agency is always under public and congressional scrutiny, especially during the aftermaths of aviation accidents. In reports published in 2003 and 2005, the Department of Transportation through the Office of the Inspector General (DOT IG) expressed concerns about the FAA's oversight of the contract maintenance industry and stated that the agency's oversight is currently insufficient for the amount of work independent repair stations perform for airlines.
The FAA has responded to these findings, in part, by introducing a risk-based inspection program that identifies those repair stations doing the most work for airlines and monitoring their operations more closely. At present, it is estimated that the FAA has certified close to 4,600 domestic and 650 foreign repair stations. However, in addition to the FAA-certified repair stations, a growing number of noncertified repair stations are performing safety-critical work, according to a December 2005 report issued by the DOT IG. By definition, the work performed by these noncertified repair stations is not overseen by the FAA inspectors. Even though the work performed in such noncertified stations must be performed by FAA-certified mechanics and inspected by FAA-certified inspectors, there is a dramatic difference between the regulatory requirements for certified and noncertified stations, as seen in figure 1 below.
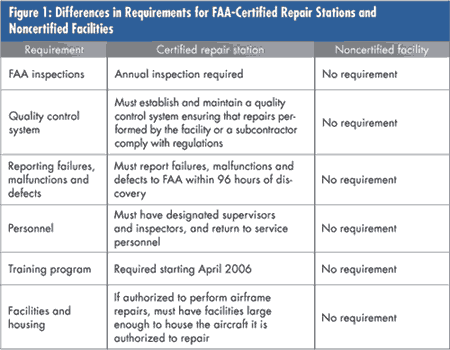
Due to economic pressures, many airlines are outsourcing a growing percentage of their maintenance, repair and overhaul (MR&O) activities. A 2005 DOT IG report estimated that during the past decade, network air carriers have increased contract maintenance from 37 percent of their total maintenance expenses to 53 percent. Furthermore, some of the outsourced MR&O work is being contracted to emerging suppliers, based in countries without a strong history in the aerospace and aviation sectors. Many interested stakeholders are concerned with the FAA's and other NAA's (as well as the airlines') ability to perform adequate oversight of distant repair stations. In these instances, inspectors need to assess the suppliers' technical and technological abilities in addition to their quality management practices, but under the heightened challenge of language and cultural barriers and differences. Figure 2 below shows the number of noncertified vendors approved by Air Transportation Oversight System air carriers to perform aircraft maintenance. It ranges from 4 percent to 39 percent of the total number of maintenance vendors.
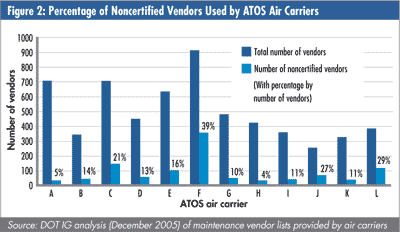
With all of these growing concerns about the contract maintenance sector being able to maintain and improve flight safety under this continually changing backdrop, a potential additional layer of control that all stakeholders might consider to provide supplementary confidence of both certified and noncertified repair stations might be derived from the industry-controlled other-party (ICOP) certification scheme to the AS9110 standard. AS9110 includes all ISO 9001 quality management system (QMS) requirements and specifies additional requirements for a QMS meant to be deployed by aerospace maintenance organizations.
It should be noted at this point that AS9110 is a U.S. standard, developed and maintained by the International Aerospace Quality Group. In Europe, the technically equivalent standard is EN 9110. Both documents contain the same requirements, so MR&O organizations operating in those parts of the world will be subjected to the same level of expectations.
AS9110 is very similar to the AS9100 standard, a document that has been developed through the Society of Automotive Engineers by the industry's major original equipment manufacturers (OEMs) and is being deployed throughout the aerospace supply chain. According to the Online Aerospace Supplier Information System database, there are more than 5,600 organizations certified to the AS9100 standard. A basic and critical aspect for any MR&O organization is compliance with the applicable aviation authorities' regulatory requirements as well as customer requirements. Accredited certification of an MR&O supplier to AS9110 is intended to provide an additional layer of control, not act as a replacement for regulatory oversight or customer monitoring.
The ICOP certification scheme has additional controls when compared to the traditional third-party certification process. Some of the additional controls include witnessed audits by OEMs and allowances for regulatory NAA representatives to perform audits of the accreditation and certification bodies, in addition to being present during the assessments of the suppliers themselves. The ICOP scheme also strengthens the requirements imposed for the qualification and competence of registrar auditors, and time spent on site during the audits.
At this time, airline involvement in the AS9110 standard and the ICOP scheme has been minimal. It is expected that some airlines, realizing the potential implications and benefits of invoking AS9110 to their supplier base, might become more involved through the sectorial groups: The Americas Aerospace Quality Group, the European Aerospace Quality Group and the Asia-Pacific Aerospace Quality Group. (See figure 3 below.)
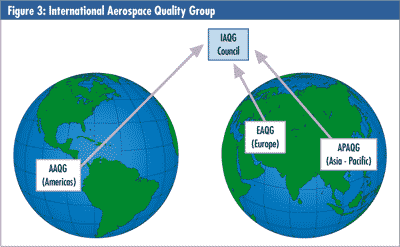
Let's explore why implementation and possibly accredited other-party certification of an MR&O organization to AS9110 could be beneficial to stakeholders, such as the suppliers themselves, the airlines, aerospace OEMs and regulatory agencies. From a supplier standpoint, implementing AS9110 may lead to a well-structured QMS, departing from the failed "do-inspect-fix-blame" cycle to the much better and more successful "plan-do-check-act" approach. The intent of a properly implemented QMS is to prevent avoidable rework and repair, thus improving profitability and timeliness of work execution. Establishing a process for monitoring customer satisfaction is also a requirement from AS9110, so the supplier will have to be proactive and seek feedback on how customers perceive it. As an example, if customers overwhelmingly complain about late deliveries or completion of major overhauls, the supplier should not only identify the issue, but through the management review, corrective action and continual improvement processes, establish ways to rectify the problems.
Many legacy airlines are presently going through financial difficulties, and supplier oversight is an increasingly expensive activity. If airlines could collectively rely on AS9110 certificates as a component of their supplier oversight process and tailor the remainder of their oversight activities based on the results of the AS9110 audits performed by the registrars and/or other customers, they could allocate their oversight resources more wisely. In the OEM world, such a process is becoming a generally accepted practice. Many aerospace OEMs are relying on ICOP-controlled AS9100 certificates as evidence of the supplier's QMS and focus instead on product-specific assessments. By shifting their attention from QMS assessment to product-related issues, OEMs are better able to assess the supplier's performance on issues that are near and dear to them. It is a much more focused assessment.
Aerospace OEMs themselves perform repair and overhaul activities and also outsource some of the work. Compliance to AS9110 could assist in boosting confidence in the quality of this work, either in house or at outside repair stations.
For regulatory agencies also struggling with the oversight-resources issue, this layer of oversight could be a welcome activity. The suppliers themselves are responsible for the costs of the registrar audits. The regulatory agencies, upon gaining confidence in the AS9110 certification process, could even use, like the airlines, the results of the AS9110 audits as an input to tailor their own oversight audits. For noncertified repair stations presently outside of the regulatory oversight process, certification to AS9110 could give the NAAs some confidence about the supplier's ability to conduct repair work that satisfies minimum recognized standards.
For the AS9110 ICOP certification process to be a reliable component of an industrywide oversight process, it is critical that all players, from the regulatory agencies, to the airlines, to the repair stations, to the accreditation bodies, to the certification bodies and suppliers, are aligned in keeping flight safety as the utmost goal. An AS9110 certificate must not decline into a fancy but meaningless certificate on the wall to be displayed at trade shows and hung in the lobby. As evidence of heightened oversight, in the AS9100 ICOP certification scheme we have seen several cases of registrar suspensions during the last five years. For the most part, such suspensions were temporary. However, some registrars have had their AS accreditation permanently withdrawn; information about registrar accreditation status is available through the OASIS database.
In addition, the AAQG, EAQG and APAQG need to make sure that the accreditation requirements for registrars authorized to issue AS9110 certificates are truly harmonized. As of early January 2006, there were different approaches between some of the European accreditation bodies and the U.S. accreditation body, ANSI-ASQ National Accreditation Board (ANAB). For the process to have, as intended, worldwide acceptance, it is critical for a truly harmonized process to exist.
Sidney Vianna is the director of aviation, space and defense certification services for DNV Certification, a leading international certification/registration body. He is a nonvoting member of the Registration Management Committee with the Americas Aerospace Quality Group. He is also the district manager in the United States and western Canada.
|