by Stanley H. Salot Jr.
The world is changing at an ever-increasing pace. To be successful in business today requires more than just the development of a new, cool-looking widget. Now we must also consider the hazardous substances (HS) embodied in some of the materials we use to produce goods--especially electronics and electrical equipment. We must plan for the entire life cycle of the items that we're creating. Although many companies have understood these issues for years, now new requirements are being driven in many nations through statutory, regulatory and judicial means. Although these vary from country to country, they all have a common theme: Corporate officers and operations management personnel are to be held accountable for their actions that result in the proliferation of hazardous substances in their products and for the disposition of those products at the end of their use life cycle.
One of the many ramifications of these new restriction of hazardous substances directives is the demand for manufacturers to demonstrate that they have taken action to reduce or eliminate the amount of hazardous and/or restricted substances in the products they design and produce. By its very nature, the act of demonstrating that the actions taken in the past and present comply with customers' and regulatory HS restrictions require documentation that evidences the exercise of due diligence in all stages of the processes, running from design through procurement of materials through production to delivery and then waste management.
In response to the European Restrictions of Hazardous Substances (RoHS) and Waste Electrical and Electronic Equipment (WEEE) directives, California state bill no. 50 (SB-50) and the Japan Green Process Supplier Survey Initiative (JGPSSI), Asian-Pacific-region industry leaders expressed a shared, recognized need for the development of a set of requirements that could be accepted and adhered to by all companies subject to the new HS restriction demands. They called on the Electronic Component Certification Board (ECCB), the U.S. management arm of the International Electrotechnical Commission Quality Assessment System (IECQ), to create a process-based standard to which all companies could be held accountable. Members of the ECCB went to work and composed such a standard. It is a hazardous substance process management (HSPM)-based approach that integrates with and complements a company's ISO 9001 quality management system. It was thereafter adopted by members of the ECCB as the U.S. national standard. On April 7, 2005, the Management Committee of the IECQ met in London and voted unanimously to implement the new hazardous-substance-free (HSF) standard and requirements, which was given the title EIA/ECCB-954, to be collaboratively deployed by the Electronics Industries Alliance (EIA) and the ECCB.
During the October 2005 International Electrotechnical Commission (IEC) Management Committee meeting in South Africa, EIA/ECCB-954 was officially adopted as the international technical specification and given the international document title QC 080000 IECQ HSPM, generally referred to as IECQ HSPM.
The new IECQ HSPM specification provides a comprehensive, common-sense approach to ensuring that production processes are managed pursuant to achieving hazardous-substance-free operations and finished products. That process management includes elements required for IECQ HSPM compliance, as seen in figure 1.
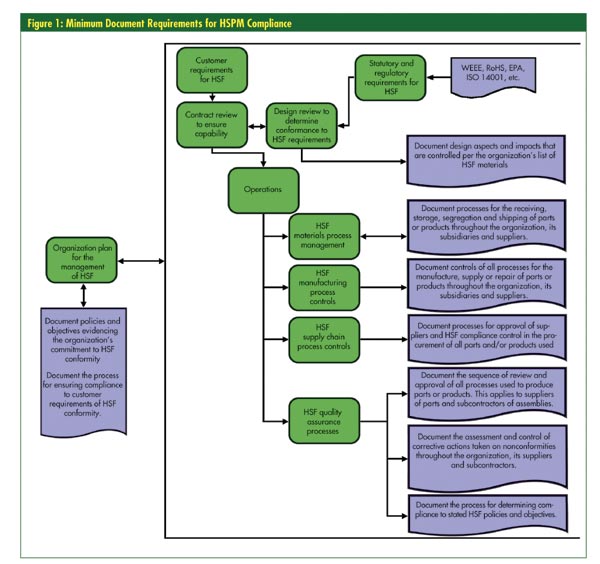
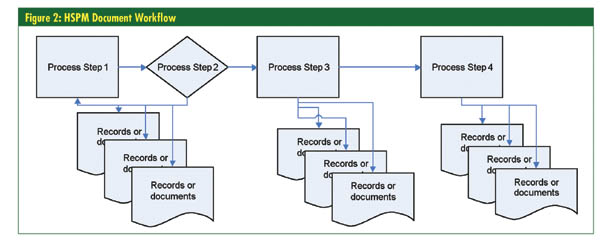
Now that we understand the need for more information to support our HSPM activities, we must find ways to identify and capture the required information with the least amount of additional overhead.
The deployment of WEEE, RoHS and Green Process management necessitates software for a process-based information management system. This type of software platform must be flexible, easily configured and able to interface with a number of disparate systems to meet the unique requirements of the company that it is to serve. The required software application must enable the company to capture key process information as well as provide the records necessary to demonstrate compliance to the IECQ HSPM specification. One such software application available in the market today is offered by EtQ Inc. The EtQ Flexible Workflow Engine (FWE) and its Reliance applications are two examples of the type of software platforms required to meet this new demand.
My organization is familiar and has had success with EtQ's platform, but any good quality management system software would do the job, such as those from ASI DataMyte, IQS or Omnex, to name a few. The main criteria when selecting software is that it be able to manage key performance indicators along with data collection, tracking and reporting. Alarms and escalation are important elements of a software application but not critical if you have some way of monitoring the data manually.
As seen in figure 1, the first step in the process is to understand customer requirements. Having records that demonstrate when the review was conducted, who conducted the review, what was reviewed, and any exceptions that exist between the requirements and the company's ability to meet them are essential. Exceptions will also need to be documented and approved as appropriate. This can be done online using electronic signatures if the software application has been validated for this capability.
You must provide access to all regulations, statutes, standards and specifications available to the employees in the organization. This can be done by using the software's documentation-control application. This enables control of electronic documents or an index identifying the location of paper documents as appropriate.
Within the documentation management system there must be a list of all hazardous substances and a plan as to how the company intends to reduce or eliminate them. Documented component specifications are another requirement as well as the specifications for all company-designed parts and/or systems with regards to hazardous substances or hazardous-substance-free parts or assemblies.
Records of design reviews are also required to demonstrate compliance. These records must include who was invited, who attended, what decisions were made and all action items resulting from the meeting.
Your software application should provide at a minimum a database for capturing this information. The corrective action/preventive action (CAPA) database should also have full tracking with alarms and escalation as appropriate. It should prevent the release of a component, product or process until all identified issues are resolved.
Purchasing and supplier management are the next key parts of the organization that must be documented and controlled as part of your HSPM system.
Purchasing will normally be managed through an ERP/accounting system and has direct connectivity or is governed by the list of approved suppliers. The additional purchasing requirement for HSPM should provide a detailed specification with each purchase order and ensure that purchases are only made from approved suppliers.
Supplier approval requires a defined procedure and assurance that the full chain of custody is identified, understood and managed. Linkages between supplier qualification, supplier assessment, receiving test/inspection records, nonconforming material and/or supplier corrective action are requirements that must be addressed and are best done using an information management system (IMS). The IMS should provide the ability for online shared access to suppliers. This allows the organization to identify nonconformances and automatically issue corrective action to an identified supplier using predefined e-mail notification and appropriate escalation. This also allows a controlled, secure channel for the supplier to respond to your organization.
Knowing what was done, when it was done, who did it and any other appropriate details is essential for a company to demonstrate the chain of custody throughout the supply channel, as required by the new regulations.
Once the raw material, components and/or assemblies are received, they must be managed in a manner that ensure the integrity of the HS and HSF materials. This includes identification and traceability throughout the organization. Nonconforming material must be identified and segregated. Actions taken to ensure that the material is processed completely are recorded, as is the corrective or preventive action taken to ensure compliance. For each step of the process there must be identified inputs, process activity and outputs. These will then be turned into inputs in the IMS so that appropriate records can be generated to demonstrate compliance.
Following are some of the data that a company should be collecting to demonstrate HSF compliance:
• Material date codes
• Material HS or HSF status at various points in stores
• Material HS or HSF status at various points in the manufacturing process
• Material HS or HSF failure data at various points in the process
• Process HS or HSF failure data at various points in the process
• Decisions made to use nonconforming material
• Process equipment change over checks
• Reworked HS or HSF material status
• Process material used to produce products
• Production equipment maintenance records
• Production equipment process changes
• Internal assessment results specific to HSPM conformance
• Corrective and preventive actions specific to HSPM conformance
• Management review actions taken specific to HSPM conformance
• Customer complaints or issues specific to HSPM conformance
Software systems can help organizations demonstrate component, assembly, product or process compliance at any time throughout the HSPM process.
Although it's possible to develop and maintain a paper-based or limited computer-based approach to demonstrate your compliance to HSF management systems, it's clearly easier and more effective to use a qualified IMS software application.
Stanley H. Salot Jr. is founder and chief technology officer of the Salot Bradley Group International (SBGi). Salot is an acknowledged expert in business and quality process management and is active in U.S. and international industry standards bodies. In his capacity as president of the ECCB, the U.S. arm of the IECQ, Salot recently co-authored the new IECQ HSPM specification for the electronics and electrical industries.
|