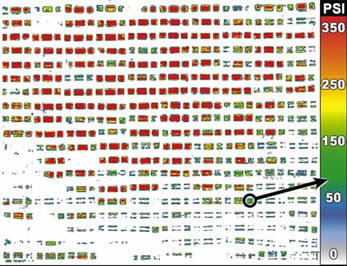
Pressurex film delivers color-coded test results.
|
Sensor Film Helps Hold Tighter Tolerances
Sensor Product’s Pressurex Film and Topaq Image Analysis System
As an innovator of film capacitor technology, SB Electronics designs and manufactures products that are on the cutting edge of today’s demanding electronics applications. To maintain continuous improvement of its manufacturing processes, David Bryan, manufacturing engineering manager for SB Electronics, recently specified the use of Pressurex, a tactile surface-pressure-indicating sensor film from Sensor Products Inc. of Madison, New Jersey.
Many of SB Electronics’ radial lead products are designed to take up the minimum amount of space on printed circuit boards. This is often done by flattening the round capacitors by pressing them between aluminum plates. A highe
r-than-expected scrap rate led the company’s quality department to contact engineering to troubleshoot and improve the process.
“After histograms indicated that some of our tighter tolerance parts (±1% capacitance) were going out of specification during our pressing operation, and making some initial dimensional measurements using conventional measuring equipment (calipers and micrometers), I wanted a better way to determine exactly what was happening with the surface pressure during this process,” says Bryan.
Bryan ordered Pressurex, a thin sensor film that instantly captures and permanently records pressure distribution and magnitude between contacting or mating surfaces. The film measures pressure from 2-43,000 psi (0.14-3,000 kg/cm 2). For his test, Bryan specified the “Super Low” Pressurex product, which measures pressure from 70-350 psi (5-25kg/cm 2).
Bryan used the Pressurex film in a manner similar to what is commonly known as press profiling. During a normal production run a specified number of capacitor sections (i.e., what the capacitors are called at this stage of the manufacturing process) are sandwiched between a pair of relatively thin aluminum transfer plates. These transfer plates are then placed in a hydraulic press where they go through a part-number- specific pressing cycle. The force and time parameters vary by product part number.
During his evaluation Bryan placed a sheet of the Pressurex film on top of the capacitor array as they were placed between the aluminum transfer plates. The transfer plates were then run through the specific pressing cycle for that product part number.
After the pressing operation, when Bryan examined the Pressurex film, different areas of the film exhibited different intensities of color, with the color changes directly proportional to the actual pressure applied at any given spot on the film. By comparing the color intensity to a color-correlation chart (conceptually similar to interpreting Litmus paper), Bryan was able to determine the precise pressure magnitude at any given area on the film. “I could visually inspect Pressurex and prove that the press plates weren’t flat and were causing uneven pressure distribution,” says Bryan.
The aluminum transfer plates were sent to the machine shop, where they were set up on a surface plate and evaluated for flatness and parallelism. The dimensional results indicated that the transfer plates were, in fact, warped. Revisions were made to the transfer plate design, and new plates made to tighter flatness and parallelism specifications.
Follow-up testing was done with the new transfer plates, and the Pressurex film indicated a dramatic improvement in the overall pressure distribution during the pressing operation. Once the plate parallelism was resolved, the scrap rate during this operation was significantly reduced.
Stimulated by this discovery, Bryan wanted to statistically analyze the surface pressure further. He asked Sensor Products to use its Topaq Image Analysis System, which consists of a Windows-based software and scanner calibrated to read and further interpret the film.
“In this case I sent the exposed Pressurex film to Sensor Products, where they ran it through their Topaq system,” says Bryan. “The exposed pressure-sensitive film is scanned optically, and the software is used to interpret numerous types of statistical information from the high-resolution, color-calibrated image.
“With this information we were able to see the force distribution, the peak force, the total force, the total contact area, the average psi, and the standard deviation. All this information is available in various, easy-to-read two- and three-dimensional formats.”
Bryan continues to use standard tools such as micrometers and calipers for quality checking at SB Electronics, but is asking that Pressurex tests be included as an ongoing quality control protocol.
Sensor Products: Pressurex Film and Topaq Image Analysis System
- Quickly assesses surface contact pressure between any two objects that contact or impact.
- Cut to the desired dimension by the user.
- Highly economical and requires no training or electronic controls.
www.sensorprod.com
|