by Peter Klepp
To remain competitive in the global economy, manufacturers are constantly seeking to increase productivity and reduce costs. With material costs relatively constant, it 's difficult to compete with an economy where the hourly rate is a fraction of yours. To be competitive, your only option is to increase productivity. A remote process management (RPM) system can help you realize an almost fivefold productivity increase using your existing machinery, facilities and employees.
RPM is a set of technologies that allows operators to remotely control and monitor their process equipment. RPM systems are used to achieve productivity, safety and security enhancements in industries from petrochemicals to zoology. The focus of this article will be RPM systems for manufacturing.
RPM systems utilize video cameras, microphones and remote control relays to monitor and control processes. By providing a view of remote locations, machines and processes, RPM can allow you to continuously run manufacturing processes unattended (even though you may be at a different location in the facility, at home or traveling). The average single-shift machine shop utilizes its machine tools for a maximum of only six or seven hours per day, five days per week. This leaves a total of only 1,820 available manufacturing hours in the entire year. Normally, to increase productivity on a machine, more operators would have to be hired; to increase productivity of the plant, more machines, facilities, power, and heating, ventilation and air-conditioning systems would need to be purchased. By using an RPM system and integrating automation if necessary, you can increase the available machine hours to 8,760 per year, for a 4.8 times increase in productivity. Imagine how competitive a factory would be if it could make almost five times more product five times faster while still using the same equipment, facilities and operators.
Many manufacturers currently have bar-feeding lathes, screw machines or pallet-feeding milling machines. These are capable of unattended operation, but they are shut down when the operators go home. Owners and managers are hesitant to risk running these machines unattended due to safety and/or quality concerns. A simple RPM system can minimize or eliminate this risk by allowing the machines to be periodically monitored and controlled from anywhere there is a high-speed Internet connection. With the ability to see, hear and control machines on a real-time basis, your risk level is much lower.
With specialized detection capabilities, you can be alerted to issues that may need your attention, such as broken or dull tools, bar feeder/pallet jams, coolant or lubrication issues, nonconforming parts, an absence of parts stock or an overflow of finished parts. Using thermal imaging will allow you to see when a cutting tool is getting worn because its heat signature will increase. An effective tool-wear and management program can also be derived from viewing, recording and analyzing trend data on cutting-tool heat signatures.
You can also effectively manage personnel with the ability not only to listen, but also to speak with remote contacts. Recording operations can also provide many benefits. Among them is the capability to review past activities and identify exactly where/when/how issues occur. Most important, these sophisticated remote monitoring, control and automation systems can be added to existing systems to upgrade the functionality of virtually any machine.
The largest benefit of RPM is its ability to increase the available operating time of your machine tools. The secondary benefit of an RPM system is that it can increase personnel productivity, especially during unsupervised or poorly supervised shifts, simply from the presence of monitoring equipment. Recorded video coverage of high-value assets can significantly decrease losses due to theft, vandalism or equipment misuse. These solutions can also dramatically decrease liabilities by recording areas of potential personal injury. This security and liability coverage alone can provide insurance cost savings that pay for the investment over time, not to mention the far larger savings and increases in profits from increased production.
The key to RPM is the tight integration of monitoring and control devices (such as remotely aimed cameras) with Internet technologies. Broadband Internet connections provide the capacity needed for live video monitoring. There are also many optional components that can be leveraged.
Cameras differ widely in aiming/zooming capabilities and illumination sensitivity, to name just a few key characteristics. Thermal imaging capabilities can also be used to inspect the thermal properties of cutting tools and surfaces. An Internet-accessible digital recorder can provide flexible visibility into all time periods. RPM users can review events many times faster than real time. These digital systems only record when there is motion, which allows for a high degree of compression, enabling digital storage and indexing. Digital indexing brings the capability to rapidly scan to the part of the video that is of most interest. Other detector and controller options that can be selected are custom mounting assemblies and/or protective enclosures. For example, these enclosures could allow a camera to be mounted inside a machine in a harsh environment where chips and coolant splash wouldn't be a factor.
A wide variety of input and output controllers can be used. A simple example is a remotely controlled light that can allow camera operation in darkness, or a relay to reset or turn off a machine. Another simple example is a microphone and speaker set, or perhaps a wiper/compressed air blast to clean a window view into a machine or to blow chips away from a cutting edge. A more complex example would be a laser-beam break-detector used to determine the presence, absence, or size of parts, tools or stock.
Custom solutions often bring the most value for RPM applications. Application consulting services can help focus investments for maximum effect to optimize both cost and effectiveness. Custom Internet applications may be of interest to enable enhanced user interfaces or capabilities. Custom configuration services and network consulting can also increase functionality. Installation services can cut costs to help users implement solutions on budget and on time.
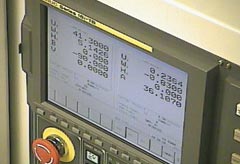
A camera allows you to monitor the entire shop floor or zoom into a control panel.
|
An example of a basic RPM solution might be to add an RPM system to a bar-feeding screw machine or lathe. The machine itself is already capable of unattended operation, and the duration of operation is primarily limited by the bar/chip capacity and tool wear. The basic RPM system would be an articulating zoom camera positioned so that it could view the cutting area and the machine control panel. The operator would simply leave the machine running, and its operation could be subsequently monitored from any Internet connection or Internet device. The operator, or factory owner, could be at home relaxing and could periodically check on the operation of his or her machines by logging into the Web address for this camera using a home computer, PDA or cell phone. The camera can be re-aimed or zoomed in or out as desired at the click of a button. The remote operator would monitor the control panel for alarms and view the machining area to make sure that all of the tools were cutting well. The operator could get a real-time view of the finished parts, and even listen to the machine. If a condition existed that was not to the viewer's satisfaction, then the machine could be remotely shut down with the click of a button. This basic system can be configured to record all of these images and sounds for future analysis.
How many times have you wanted to go back in time to see why something happened? Why did a tool break or why did a machine really crash? RPM gives you that ability. You can scroll back in time through a time-stamped video to see and hear exactly what happened and when. The risk associated with leaving your machines unattended is mitigated. Even if you had a single bar feeder, and you were able to gain only three more hours of unattended operation every day, you could still realize a 46-percent productivity increase on that machine.
There's nothing special or expensive required for implementing a remote monitoring system. To implement a Web-based system, you will need to have a high-speed Internet connection in your facility (perhaps an existing DSL, cable modem, T1, T3, frame relay and/or other data service). Connecting the system is as easy as adding another computer to your network and opening a path from the Internet connection. You follow the instructions, plug in and mount the camera and configure the software, and it's ready to be used. In most cases, there are no monthly costs or additional fees, and the system can be set up and configured by anyone with basic computer skills. Comprehensive consulting services are also available for more complex installations. Entry-level, fixed-position systems can start at less than $1,600.
Peter Klepp is the president of Dorsey Metrology International, a manufacturer of precision dimensional measurement instruments. Dorsey has spent more than 50 years developing and manufacturing a wide variety of quality gaging products utilizing sensing technologies, from basic dial indicators to integrated laser and vision systems.
|