by Paul Sagar
Electronic gage temperature compensation has proven to be an effective and economically beneficial shop floor stratagem. Older technologies, however, limited user interfaces to displays, push buttons, codes and abbreviations that were hard to comprehend. The concept of temperature compensation and the complexities of linear and nonlinear expansion coefficients were confusing, and competing theories and algorithms added to the perplexity. These factors tended to impede the widespread implementation of an otherwise highly beneficial and cost-effective technology.
Fortunately, temperature compensation has come a long way. Today's devices are more automated, user-friendly and affordable than ever.
The main components in temperature compensation are sensors. Today's temperature-compensation applications use sensors that have been designed specifically for tough industrial applications. Unfortunately, noncontact sensors (e.g., infrared sensors) aren't sufficiently accurate for temperature-compensation requirements, particularly when shiny metal components are measured. Such applications therefore usually require that sensors make contact with workpieces, masters and gage fixtures.
Contact temperature-sensing elements that are incorporated into commercial temperature sensors tend to have minimal mass for fast response. Consequently, they're fragile. Therefore, a sensor that comes into repeated contact with a metal workpiece and that might be exposed to coolants and grit must be strengthened and sealed, or it will fail frequently. In addition, it must have some sprung-axial and lateral freedom of movement to conform to the workpiece surface or master it's targeting, and to retract when hard contact is made.
The price of durability, however, is slower response time. All contact temperature-sensor response curves are asymptotic. (See figure 1.) Rather than waiting for a full reading, temperature-compensation systems are often calibrated to use temperature readings near the top of the curve, when the sensor has registered most, but not quite all, of the temperature change. The figure illustrates that within two to three seconds a sensor will have registered 95 percent or more of a temperature change, from ambient to target temperature. This range might be from the shop floor air temperature of 22° C (72° F), which the sensor could measure after an idle period, to a workpiece temperature of 45° C (113° F) after the part emerges from a washer--a change of 23° C (41° F).
A temperature-compensation system receives inputs in real time from temperature sensors positioned to measure temperatures of workpieces, masters (when they're in position to set the gage) and gage fixtures. It uses these along with the preprogrammed nominal size and coefficient parameters to calculate a net correction that would be required to reflect the true dimensions if the workpiece, master and gage were at 20° C (68° F)--the international reference temperature according to ISO 1, first released in 1975. The temperature-compensation device, or the host gage to which it's communicating, uses this correction to adjust values determined by a linear variable differential transducer (LVDT) or other dimensional probe inputs before they're displayed. Consequently, temperature-compensated gages can deliver results year-round, as if workpieces and the environment were at a controlled 20° C, even when temperatures vary. Because such thermal deviations can be the cause of significant discrepancies in gage performance, eliminating thermally induced gaging errors can mean a considerable improvement in year-round gage correlation.
Gage repeatability and reproducibility (GR&R) studies measure the amount of variation in a measurement system arising from the measurement de--vice itself and the people taking the measurements. Gage studies are subjected to the 10-percent rule, which requires, for one, that no more than 10 percent of a total tolerance be consumed by GR&R variation.
Recognizing the potential for error, procedures for conducting GR&R studies usually require that temperatures be held constant while data are taken. This is fine for determining the best possible performance of the measurement system under ideal conditions. However, it's unrealistic to exclude the effects of temperature variations when considering true gage performance.
After these studies are made, the gages are used on the shop floor and erroneously assumed to perform to the same GR&R standard observed in a controlled environment. In practice, even small temperature variations will rapidly consume more than 10 percent of total tolerance.
A true test of GR&R should take temperature variations into account. No procedures have yet been widely adopted to address this issue. However, a temperature-compensation system minimizes the effects of thermal influences and maintains the GR&R while being subjected to wide fluctuations in temperature. Thus, thermal effects can be excluded from measurements, and gages will perform at a constant GR&R on the shop floor.
Another way to look at the effects of eliminating thermal errors is to consider the difference between precision and accuracy. Precision tends to focus on repeatability of measurements, while accuracy is concerned with exactness of conformity to specification. A group of measurements that were very close together but not to specification could be considered precise even if they weren't accurate. Thermally corrected measurements can preserve the precision of measurements while increasing their accuracy.
Manufacturers of bearing rings, auto engine blocks, cylinder heads, crankshafts, pistons, piston pins, shafts, axles, brake rotors and printing cylinders are already enjoying these benefits. The common theme of these components is their substantial mass relative to tight tolerance specifications. They can experience shop floor thermal expansion and contraction that consume a substantial part, if not all, of total tolerance. Failure to address this problem can create process-control, quality and yield issues. This is unnecessary now that these errors can be minimized rapidly and inexpensively.
Bearing rings represent a good example of parts that are large enough to experience shop floor thermal expansion. For example, a bearing ring with a 100-mm diameter might have a total tolerance of 25 µm (.025 mm). At 37° C (98° F), this ring will have expanded by as much as 20 µm above its comparable size when measured at a temperature of 20° C. It will have consumed 80 percent of total tolerance, even though GR&R standards require that the minimum measurement system variation should be no greater than 10 percent. It would be quite possible on a hot day for an undersized ring measuring, say, 99.985 mm, to be measured on the shop floor and found to be within specification, only to be rejected later at a cooler temperature. Further, only a small temperature variation is needed to cause expansion that would push a measured dimension beyond a tolerance limit, causing a bad part to be called good, or vice versa. Just a micron or two can make that difference. As parts approach tolerance limits, the effects of temperature become a particular concern.
One of the world's leading makers of bearings takes this matter very seriously. The company has supported a leading temperature-compensation equipment manufacturer, Albion Devices Inc., in developing its MicroComp temperature-compensation system and is using it in many of its plants worldwide to monitor the production of bearing rings.
In the company's benchtop gage applications on the production floor, one temperature sensor is placed within the gage in such a way as to sense the temperature of the workpiece or the master, depending on which is in position. Another sensor is embedded within the gage hardware to pick up a representative temperature of the fixture. A single LVDT probe is used to compare the dimension of a master to a workpiece.
When the master is placed in the gage fixture and MicroComp is "zeroed," the master's temperature is sensed by the first sensor. MicroComp immediately corrects for any difference in temperature of the master from 20° C, which would otherwise cause the gage to be calibrated inaccurately from the outset. This is usually the case with comparative gages that don't compensate for temperature.
It also monitors the temperature of the gage fixture that's being read by the second sensor--the gage sensor--and compensates in real time for any temperature-caused change in the gage fixture's size. As parts are measured, the first temperature sensor makes contact with the bearing ring and takes its temperature within two or three seconds. The correction algorithm is applied using preprogrammed coefficients and the calculations for master and gage size variation described previously. It displays a net temperature-corrected dimension on its screen. This dimension represents the true difference in size between master and workpiece that would be observed if master, workpiece and gage fixture were at 20° C.
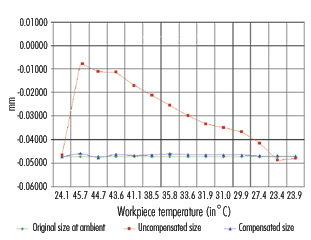
|
Thus, even if the plant floor is extremely hot or cold, operators instantaneously obtain close to the same measurement result they would if they were to take the part into a temperature-controlled gage room, let it stabilize during several hours, and take the measurement at a controlled temperature, as seen in figure 2.
Operators are looking at measurements that will allow them to control the production process using data that are almost free of thermal errors. The parts that are produced and controlled on this line will be assembled without problems with mating parts, using the same temperature-compensated gaging method at different times and different temperatures. The quality department can be assured that parts meet specified tolerances.
Before it's put into use in temperature-compensating mode, a temperature-compensation system must be programmed with coefficients suitable for its proposed application. These can be selected from a list provided in software, or custom values may be entered. For best results users should determine these values empirically by testing at varying temperatures. Empirically determined correction coefficients can be accurate to within ± 3 percent or better, versus the ± 10-percent to 15-percent accuracy recommended in handbooks. The temperature sensors typically reach to within 0.5° F of actual temperature within reasonable gage cycle times. The end result of using empirically determined coefficients is that temperature compensation typically corrects for 95 to 98 percent of all thermal error. The remaining 2 to 5 percent error might amount to a micron or two at worst but will compare favorably to an error as large as 30 µm or more.
Process-capability studies have been conducted by major auto manufacturers on several production lines both before and after introducing temperature-compensated gaging. (See figure 3.) The reduction of measurement variation in the process allows closer and more accurate control of the process, producing dramatic results of 200 percent and greater in Cp and Cpk measurements.
Temperature compensation represents the lowest-cost solution to real problems:
• It improves accuracy and process capability.
• It provides correlation between gages.
• It's more accurate and less expensive than mechanical means, such as air conditioning, in controlling shop floor temperatures.
• It maintains GR&R on the shop floor.
• It provides more "elbow room" for operators because less tolerance is used by thermal errors, and more is available for other factors.
• It gives true dimensions at the international standard of 20° C, which is the size that was intended by the design engineers who produced the specifications.
Comparison of process-capability study results with and without temperature compensation |
Temperature compensation can improve quality, reduce scrap and rework, improve gage correlation and boost process-control statistics such as Cp and Cpk by consistently minimizing the detrimental effects of thermal errors in shop floor gaging. Above all, by reducing costs and improving productivity, gage temperature compensation increases profits. Precision-component manufacturers intent on process improvement can't afford to miss the potential return on investment possible from implementing temperature compensation. The potential reductions in production inefficiencies and inaccuracies, the minimization of misunderstandings and disagreements over dimensional control and improvements in production yields will quickly justify the investment of capital, time and effort in installing or retrofitting this technology.
For too long, thermal effects on the shop floor have been ignored or dismissed as too difficult to control. Now, as manufacturers search for ways to improve capability and reduce costs, there are user-friendly, cost-effective and tested technological innovations available. If we're truly concerned about competing in an increasingly tough manufacturing marketplace, then gage temperature compensation shouldn't be ignored.
Paul Sagar is president of Albion Devices Inc., a leader in the development, implementation and servicing of user-friendly shop floor temperature-compensated gaging systems. For more information, visit www.albiondevices.com.
|