At Parker Hannifin's Tucson, Arizona, facility (Partek), we use a Visual Basic program to input our inspection data into shop-floor
computers. The screen shows the part number being inspected, and the computer prompts the operators to look for visual defects and instructs them on which dimensions to measure. For many dimensions, operators can use
digital micrometers or calipers to check the parts and then simply press a button to enter the measurement. The data is transmitted to a computer using a GageTalker. All relevant information is then sent to a Microsoft
Access database (see Table 1). Palo Verde Software wrote the code in Visual Basic and worked with us to develop the screen layouts. Because the software development company is local, the wizards at Palo Verde have been
able to customize and further refine the program as we gained experience with it.
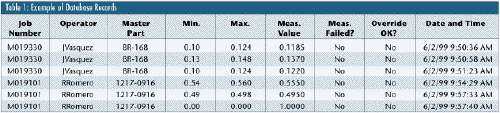 |
The table shows only about a third of the data in each line of the database, because the database pages are too wide to present in this format. Columns one, two and
three are self-explanatory. Columns four and five show specification limits, and column six is the actual measurement the operators got when the parts were
checked. Column seven is titled "Measurement Failed?" The first thing I do every morning is check that column to see if we made any parts out of specification. If any
parts were reported out of tolerance, I make sure they went to the material review board (MRB). If production wants to continue the job run while the parts are out of
specification (as when, for example, the problem is in the process of being corrected), they must get permission from an authorized person. That person must
approve the override and indicate so in column eight. Column nine is a date/time stamp that gives us a clear record of when specific events took place.
One of the things we learned from our MRB records (also in a database) is that our design engineers often over-specify some of our part dimensions. The corrective
action in those cases is simply to open up the tolerance. At other times, we have to make process changes to bring the parts into specification.
Just glancing at our database records gives us a good picture of what part was made, who made it, when he or she made it and how well we can hold the
tolerance. When I give customers the plant tour, I show them our database and how carefully we keep track of everything. It gives them a lot of confidence to know we
are on top of our processes, and it helps our marketing department sell our products. Because Access is a Windows application, it's easy to cut and paste data into other
Windows applications, such as Excel. From there, it's a snap to construct graphs and compute statistics. Some of the statistical process control packages on the
market are also Windows applications, and you can use them to make histograms, compute process capability and make control charts.
Access is a powerful program that lets you manipulate data in a database. In seconds I can put together a query that will sort through our 80,000-plus inspection
records and pull out all data for a given part number. We have used Access to perform studies to estimate measurement error, compute process capability and study physical effects in our process.
All of the aforementioned software is used to collect data and perform SPC, but this doesn't limit its usefulness. SPC is a scientific comparison of short-term and
long-term variation. It is important to remember that SPC is universal in application. It is frequently used to analyze dimensional data in a factory, but it can also be used
to investigate the time it takes to process purchase orders, analyze customer returns, monitor a patient's blood pressure in a doctor's office or study the use of operating theaters in a busy hospital.
Partek's data collection and analysis system allows us to continuously improve production. There are many problems through which we have to work our way
over time, but because we keep an extensive history of our production efforts, our parts are better today than they were a year ago. They will be better still next year.
With custom software, SPC and a little elbow grease, my job gets easier every day. About the author
Gregory P. Ferguson is quality manager at Parker Hannifin's Tucson facility. E-mail him at gferguson@qualitydigest.com . |