If you were to ask the average airline commuter to explain the mechanics of jet flight, chances are good that the concept of the turbine
engine would come up. Turbine engines are critical to jet flight, but they're only as reliable as their components. Given the tight tolerances required during their manufacture and the abuse that turbine airfoils take
in their lifetimes, an accurate, efficient measurement system is crucial. The technology of jet engines has come a long way in the past 50 years, but the tools used in their inspection haven't kept
up. In an effort to add both accuracy and efficiency to turbine blade measurement, Brown & Sharpe has introduced a revolutionary new turbine blade measuring machine called the AF-X. Unveiled in
June at Turbo Expo '99 in Indianapolis, the AF-X combines two patented elements: laser stripe illumination and line-scan camera technology. The technologies were developed by Metroptic, a joint venture between Brown
& Sharpe and an Israeli company. The combined technologies are known as a dynamic stripe sensor (DSS). The AF-X is specifically designed to measure turbine blades and will be
used by both the power generation and airfoil industries. Although the AF-X can measure all types of turbine blades, Brown & Sharpe views the aerospace industry as its primary market. Within the
aerospace industry, advanced airfoil and leading-edge forms have pushed the bounds of existing measurement technologies to quickly and accurately examine blades. The industry's two most common blade measurement
instruments are falling behind blade technology: Guillotine gages are pricey and archaic, and coordinate measuring machines (CMMs), although more accurate, are slower. In addition, guillotine gages can't accurately
measure a blade's leading and trailing edges--a key element in efficient turbines.
Blade-Measurement Options: A Comparison Guillotines These custom gages provide a quick, visual indication of a given blade's
characteristics.Guillotines are less accurate and repeatable than other blade measurement devices. Also, their required maintenance and design- specific nature can be costly. 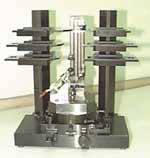 Guillotine Gage
CMMs
CMMs offer the ability to measure more than just blades while eliminating much of the user-oriented interface of the guillotines. Measuring fewer than two data
points per second, a CMM's primary limitation in this field is its lack of speed. 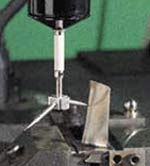 CMM probe
AF-X The AF-X provides fast and accurate noncontact measurement of all turbine blades. Tailored to one
market, this machine supplies users with more useful information than can any other measurement device. The AF-X can cost more initially than a set of guillotines or a CMM.
Its uses are currently limited to turbine blade measurement.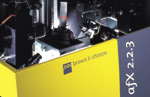 afX
|
|
Past: guillotine gages In the past, measuring a blade required an
engineer to cut it in half, put it on a shadow graph and then match it visually to a master template. Not only was this process slow and imprecise, but it only allowed for sample testing rather than
100-percent inspection. The next step in the evolution of airfoil measurement was to use guillotine gages, complex devices that snap onto turbine blades. Guillotine gages have remained a mainstay
of airfoil measurement for years. "They have their place in the world of measurement within the blade manufacturers of the world," says one industry expert. "Of course, they are less
accurate than other methods, such as CMM measurement or Brown & Sharpe's new noncontact AF-X." Guillotine gages are industry-specific and have to be custom-made for each blade
design and sometimes for each blade surface. Convincing industry insiders to switch from their considerable investment in the manufacture and maintenance of this gage system is an admittedly difficult task.
"As a cost issue, many have invested heavily in guillotines," notes David Genest, Brown & Sharpe's director of marketing and corporate communications. "As a speed issue, no CMM can match the
speed of these gages, notwithstanding their level of inaccuracy." The guillotine gage's intricate design provides many of its drawbacks. "It's a mechanical instrument, so if you drop it or
neglect to calibrate it regularly, it becomes less accurate," explains Genest. Part of the accuracy problem lies in the guillotine gage's user-oriented interface.
The gage consists of a series of mechanical sensors that snap onto a blade surface. These instruments are used to measure a blade's dimensions at a particular cross section or set of cross sections. "You
mount the blade to a fixture, attach this gage, take the measurements and write them down," says Genest. This fairly mechanical and user-oriented process introduces many variables and subsequent
chances for diminished accuracy. The price of a guillotine gage ranges broadly because larger blades with more complex curvatures require more expensive gages. At tens of thousands of
dollars each, a set for a number of blade designs can easily cost more than the AF-X's $205,000 price tag. Guillotine gages are quickly becoming yesterday's
technology. Although most blade manufacturers now use CMMs because of their greater accuracy, the guillotine gages' speed has prevented them from being eliminated completely. Present: CMMs "One advantage of coordinate measuring machines is that they can be used on
the shop floor to inspect components in a production environment," says Genest. Not long ago, CMMs were heralded as guillotine replacements. They can be
used to perform a variety of critical engine component inspection routines. Some scanning CMMs, including Brown & Sharpe's own Chameleon, are capable of scanning blades' leading and trailing edges.
CMMs offer increased accuracy and flexibility over guillotine gages. With CMMs, gone are the days of needing a specific tool for each blade design.
Gone are the days of poor accuracy and archaic design. So why aren't the days of the guillotine gone? "Ten years ago every gaging program that came along included a guillotine gage,
but now we build only two or three a year," says Michael Scanlon, engineering manager at Apollo Products, a custom gage and fixture manufacturer. In the
interest of compensating for some of the shortcomings of guillotine gages, some in the aerospace industry have turned to CMMs. "However, buying a CMM to
replace just a single guillotine gage wouldn't make sense. Because of what a CMM can cost, you'd consider purchasing one to replace guillotine gages in total," explains Scanlon.
However, many who did just that were disappointed. Despite the lack of accuracy that comes bundled with the guillotine's user-oriented interface, and the
fact that CMMs can output measurement results automatically and in many formats, turbine blade manufacturers and overhaulers alike were used to the
visual and tactile feedback afforded by the custom gages. As a result, companies have been wary of totally replacing guillotine gages. "People liked that guillotine
gages are so visual," Genest clarifies. "With them, you can see and touch errors in a blade. CMMs were viewed as slow and foreign."
Brown & Sharpe's goal is to replace CMMs with the AF-X for the measurement of turbine blades. "Those using CMMs for other measurements
would not get rid of their CMM, but instead would use the AF-X for blade measurement," says Genest. "CMMs are more generic. They're very good at
doing many different kinds of measurements, but the AF-X provides more tailored and useful data for this operation."
Theory of OperationAlthough the
actual optics, mechanics and software for the AF-X are quite complex, the theory of operation is fairly simple. Each AF-X incorporates four synchronized, simultaneously reading dynamic stripe sensors (DSS) and a turbine-blade stage that moves up and down. Each DSS comprises two stripe- generating lasers, a 3X objective lens
and a 5,000-pixel line-scan charge- coupled device (CCD) array. One laser is inclined at 30 degrees above the lens and the other at 30 degrees below. The lasers intersect at a point exactly 10
inches in front of the lens--the focal point. In operation, each pair of DSS lasers scans
a section of the blade with a laser stripe that is 0.001 in. wide and 4.5 in. long. At the same time, the DSS moves rapidly toward and away from the blade, seeking
the maximum amount of light to be reflected from the blade's surface at each CCD pixel position. For each pixel, this occurs only when the lasers intersect at the
point on the blade's surface that is in front of that pixel. Because the blade is curved, the intersection will not be simultaneous along the entire blade. As the DSS moves
in and out, the AF-X can calculate the true focus point for each pixel (i.e., the distance from the DSS to that point on the blade) and therefore the x, y and z coordinates of
that point, with the z value taken from the blade's vertical stage position. There are two DSSs positioned in front of the blade to be measured, and two behind.
All four DSSs are at the same height, and the above operation occurs on all four DSSs simultaneously, providing 360-degree measurement of that cross section. The
blade is then moved vertically and a new cross section is measured. Each cross- sectional measurement takes 1 second.
The four-DSS configuration is important not only because it allows measurement of the front and back sides of the blade, but also because it allows measurement of the
extremely critical leading and trailing edges--something that other technologies have failed to do adequately. The result is a true 360-degree measurement of the blade with 10-micron measurement
uncertainty. |
|
Future: AF-X To replace both CMMs and guillotine gages, the AF-X will have
to operate faster than a CMM and more accurately than a guillotine gage. The AF-X provides an impressive amount of information at a rapid speed. Operating in a controlled
environment, the AF-X can collect up to 20,000 data points per second, measuring a blade 200 mm long in less than a minute with 10-micron uncertainty. By comparison, Brown & Sharpe's Chameleon CMM, fast in terms of
CMM speed, collects only two data points per second. The marriage of guillotine-like speed with even more information than CMMs can provide is the AF-X's selling point, claims Genest.
To offer complete 360 degrees of measurement, the AF-X incorporates four synchronized, simultaneous-reading DSSs. Each consists of two stripe-generating lasers and a line-scan CCD camera
in a monolithic body. The four DSSs scan a complete cross section of the blade, including the critical leading and trailing edges. The ability to measure the edges set the AF-X apart from other
technologies and is another key selling point of the product, says Genest. Another benefit of the AF-X's use of DSS technology is fast and accurate output. Although a
guillotine gage is a quick tool for immediate feedback, the resulting data is insufficient at best. "Because of the nature of guillotine design, an operator can mistakenly get an unacceptable blade to pass through
guillotine inspection," explains Scanlon. "A given guillotine might measure 12 points on a blade surface, while a CMM could increase that number to a thousand points," adds Genest.
"The AF-X deals with thousands and thousands of points. So while a CMM and the AF-X may have comparable machine accuracy ratings, the AF-X gives the user a much more complete picture of
what is happening on every surface of a measured blade." To convey its findings, the new AF-X includes a PC and custom software in an industrial cabinet. AF-X's software illustrates
measurements in a 3-D rendering of the measured part. In addition, any points on the blade under or over allowable tolerances are highlighted for the user. This advanced software program
provides special routines developed exclusively for airfoil measurement and inspection applications. AF-X's software gives users many measurement options, plus a variety of formats in which to archive and report data.
Looking ahead
The AF-X's scalability suggests additional applications. "We see a market for this type of system not only in turbine engine blade manufacturing and inspection
and repair operations, but also for other applications where large amounts of accurate data are needed to check form and shape," says Frank Curtin, Brown
& Sharpe's chairman, president and CEO. The patented laser-strip illumination and high-performance line-scan camera technologies will likely be used in the
future to measure items as large as aircraft body sheet metal and as small as electronic circuits. "Coming right on the heels of the AF-X will be a similar configuration of the
machine with the same measuring technology for the measurement of dies and molds," adds Genest. "That's a natural because of the complex surfaces
involved. Next, we'll be measuring silicon wafers and other products in the electronics sector. In the long term, we will be using this technology to replace scores of traditional CMMs." About the author Robert Green is Quality Digest's assistant editor. E-mail your comments to afx@qualitydigest.com .
|