by Phil Heil and Richard Daigle
The economic axiom that what goes up must come down has
held true in recent years. Money has been tight in many
industries, but forecasters tell us that what’s been
down will start to rise in 2004. This is good news for
most businesses, but it’s great news for
the machine vision industry.
In addition to the economic upswing, another factor contributing
to what could be the best year ever for machine vision
systems are smart sensors, or “smart cameras.” They’ve
come into their own, offering far greater power for far
less money than was the case even two or three years ago.
As manufacturers prosper, they will invest more in quality
control, inspection and robotic assembly--all areas in
which smart cameras can make a significant difference,
providing 100-percent inspection and no-fail robotic guidance.
This may sound like an optimistic fantasy, depending
on your company’s situation, but it’s not.
The National Association of Manufacturers forecasts a 6
percent production boost that will generate some 250,000
jobs in 2004, partially offsetting heavy job losses suffered
in recent years. The Manufacturers Alliance/
MAPI reported its business index rose to 77 during the
last quarter of 2003, the highest level since the index
began in 1972. Short- and long-term futures for machine
vision are equally bright.
There was a time during the early 1990s when smart cameras
had a reputation, perhaps deservedly, as expensive high-tech
gadgetry that didn’t deliver in terms of performance.
Just five years ago, the average cost of a machine vision
smart camera system was out of many companies’ price
range. Today, an even more powerful
system can cost less than $2,000. During a recent training
luncheon at DVT Corp. in Atlanta, one student, commenting
on a machine vision system’s capabilities, said, “It’s
not a matter of knowing what application the camera can
handle but what application it can’t handle.”
A proven track record for smart camera machine vision
will also carry weight in the minds of decision makers,
especially for applications in which meeting strict government
standards--such as 21 CFR Part 11 or other quality control
measures--is critical.
Machine vision systems are used in a variety of applications,
including:
n Pharmaceutical packaging inspection. The machine vision
systems are typically 21 CFR Part 11-compliant.
Automotive light bulb inspection that meets Six Sigma
standards
Inspection
of fill-levels of opaque bottles using smart cameras in
concert with X-ray technology
Inspection
to ensure Teflon coating is properly applied to medical
inhalant canisters
Although machine vision applications have proved increasingly
useful in recent years, the technology offers untapped
potential in the manufacturing industry worldwide. As assembly
line speeds have increased, human inspectors can’t
keep pace with a 100- percent inspection rate.
Simple sensors and other rudimentary machine vision tools
offer a basic level of inspection, but as applications
grow in sophistication, smart cameras are proving their
worth on the assembly line. Packaging, pharmaceuticals,
automotive, electronics and plastics are all growing markets
for machine vision smart camera systems. Lower integration
costs and better after-sale support give the technology
a distinct advantage over frame-grabber systems in many
applications.
A smart camera or “smart image sensor” is
much more than just a camera. It’s a digital camera,
small enough to fit in the palm of your hand but also packed
with the high-tech capabilities of an onboard computer
processor and a CCD that captures digital images at the
smallest unit: a pixel.
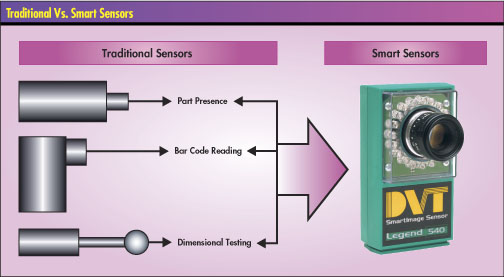
High-end smart cameras can measure down to a tenth of
a pixel with total reliability and even smaller with varying
degrees of reliability. Smart cameras can take precise
measurements, sort by miniscule color variations and object
shape, and perform optical character recognition, bar code
recognition and other tasks--all at speeds faster than
most assembly line inspection rates. Smart cameras can
handle speeds up to 2,000 parts per minute, depending on
the application.
Sales of smart image sensors for manufacturing applications
have grown from 30 to 50 percent annually since their introduction
more than a decade ago. Vision Systems International conducts
annual financial analysis reports that review productivity,
profitability and other standards for public machine vision
companies. Its 2002 report, which looked at 31 companies
that receive 5 percent or more of their revenue from machine
vision/imaging, indicates a slowdown of growth as compared
to 2001 numbers but, nonetheless, a 19 percent median gross
margin. Despite absorbing blows from the sluggish U.S.
economy, the future of smart cameras remains bright.
The technology’s versatility and ease of use continue
to drive its success in the marketplace. Sensors are used
throughout manufacturing to provide feedback for process
control and monitoring. The sensors can direct their information
to programmable logic controllers through a hard-wired
DC connection. In the simplest case, the sensor provides
a yes/no indication.
For example, a proximity sensor will detect if a part
is present or not. More advanced sensors can provide a
variable result. For example, a fill-level sensor can indicate
the fluid height inside a tank. Another common example
is a bar code reader that collects a code and outputs it
via serial to a controller.
A smart camera is similar to standard sensors in that
it visually measures a quantity or reads information from
a part. The difference is that a smart sensor can be configured
to perform a variety of tasks simultaneously and communicate
this information in nearly any format, as illustrated on
page 21.
Smart cameras are used in a number of fields, including
automotive, pharmaceutical, plastics, electronics and food/beverage.
They’re proficient in detecting defects,
taking precision measurements, and picking, placing and
performing other positioning applications involving robots,
OCR, data collection and 2-D data matrix. Currently, packaging
is the fastest growing industry for smart camera machine
inspection.
For the first time, smart cameras are being used in an
X-ray unit that features affordable nondestructive testing
for nontransparent applications. The combination of smart
sensor technology and X-ray capabilities allows smart cameras
to perform varied functions on items that are hidden to
the naked eye.
The KMV Technologies InnerVision X-ray system, using
DVT cameras, is an example of the marriage between X-ray
vision and machine vision. The KMV unit can be used for
most nontransparent applications, including:
Checking wire connector integrity
Checking fill-levels in nontransparent containers
Checking proper fill of injection-molded parts
Checking electrical connector pin alignment
Unlike smart cameras, traditional sensors can’t
be programmed. Instead, they’re limited to performing
one task at a time, making a single pass/fail decision
based on adjustments to sensitivity. A typical application
might read the bar code on a part, perform a measurement
and relay this information to the factory network. The
PLC would set the part aside for rework if it didn’t
meet the specification, and the work cell controller would
track the part based on the bar code. With a traditional
sensor, this application would be done using contact probes
and a bar code scanner connected to a PC--three different
hardware units performing separate tasks with separate
information channels.

A smart camera can perform these tasks simultaneously
with the same set of tools, completing the application
at a lower cost and providing more options for flexible
manufacturing. It can also convey information from more
than one inspection in one communication channel.
Two major classes of vision systems compete in the market
today. Vision and photoeye systems can be taught using
a single button or a video game controller, whereas smart
cameras are connected to a PC. The former class is easy
to set up but less flexible and limited in communications
options. Such sensors are best used for solving simple
problems when a great deal of automation hardware is already
present to handle variations and communications, as illustrated
at the top of page 22.
Traditional sensors using serial connections make pass/fail
decisions that can’t be integrated into one system
but must instead travel to different systems on different
paths. Because they’re not programmable, traditional
sensors can’t make intelligent decisions about information.
They simply make one decision based on input from one source.
When a customer uses a PC and takes advantage of the familiar
Windows interface, setting up a more advanced class of
smart camera is easy. In this case, a powerful communications
system’s flexibility can be fully configured. When
standardizing on a common sensor platform, a single software
package can be learned, and many different applications
can be solved quickly with a common interface, as illustrated
on page 22.
Smart image cameras handle information flow much more
efficiently than traditional sensors. Smart cameras can
perform more than one inspection at a time, sending that
data in a single stream to PLCs or other devices. The data
can then be easily stored for analysis or use with reject
mechanisms or other components on the line. Smart cameras
are commonly found in the automotive industry, where there’s
an urgent need for quality, low cost and ease of use. And
now, with the expanded capabilities of recent models, packaging
and pharmaceutical industries also make use of the technology.
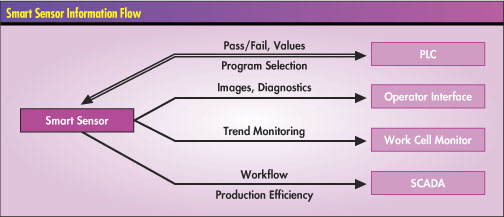
The applications vary widely, but some common problems
solved by smart cameras include checking for a part’s
presence or a defect’s absence. When first developed,
the smart camera was designed to replace arrays of photoeyes
that were used to verify that a part was assembled properly.
The photoeyes did a great job until it was time to switch
the line to a new part.
A smart camera can draw on hundreds of configuration
files to determine what inspection is to take place. As
tools were added to the design, tasks such as dimension
checking and tolerance verification were accomplished with
low-cost platforms. Formerly done by humans or analog frame
grabber-based vision systems, the smart camera proved that
direct-image acquisition provided a level of consistency
that hadn’t been seen in a hardware device costing
less than $10,000. This led to further improvements to
handle bar code reading and optical character recognition
in a single package. Applications that would normally be
done with four or five different devices could be solved
with one.
Throughout the 1990s, the Ethernet market outgrew its
humble beginnings of connecting PCs in schools and offices.
Industrial devices emerged that could communicate over
this now ubiquitous interface. In late 1998, DVT introduced
the first vision smart sensor with onboard Ethernet. The
smart sensor had outgrown its role as a simple yes/no decision
maker into an information provider for the entire factory.
In the coming years, as industrial quality standards
merge, the Ethernet may well be the hardware interface
that binds all the equipment. Smart
sensors will evolve along with the standards to support
communication, from the least expensive PLC to the most
costly enterprise resource planning software package. As
software and hardware are added, these sensors will be
able to handle increasingly complex visual inspection tasks.
At the same time, the falling costs of electronics and
the availability of free training will allow more of the
sensor market to be overtaken by inexpensive smart sensors.
The success of new technology is usually tied to the
ebb and flow of economic fortunes. When money flows, technology
grows. As the machine vision industry is fueled by new
capital expenditures, smart camera technology will continue
to provide more robust solutions for the manufacturing
world.
Phil Heil earned his mechanical engineering bachelor’s
degree at Carnegie Mellon University and his doctorate
in mechanical engineering at Georgia Tech. He has worked
at DVT Corp. in the Applied
Engineering Department since 1996. Heil has since worked
in training, technical support and application support
for DVT.
Richard Daigle has a bachelor’s degree in journalism
from Southeastern Louisiana University and a master’s
degree in communications from Georgia State University.
After serving as reporter and editor for a daily newspaper
in South Georgia, he worked in public relations for the
State of Georgia Department of Natural Resources, Coastal
Resources Division. Richard was formerly a writer for a
multimedia company in Atlanta. Since joining DVT, Daigle
has launched the company’s quarterly magazine, Vision
in Action.
Portions of this article © 2003, Society of
Manufacturing Engineers.
|