Creative Thinking Helps Boeing Improve
In the spring of 2001, Larry
Larson and his colleague Bob Harms, who help build Boeing
757 airplanes in a factory near Seattle, found inspiration
for a new technology in a barnyard.
The two men were a part of the Boeing Co.’s Moonshine
Shop factory team, which was charged with discovering new
ways to decrease the costs and time required to build jetliners.
The Moonshine Shop gets its name from a Japanese lean manufacturing
philosophy that describes innovators developing new methods
late at night.
That spring, the two colleagues set off on a mission:
to find a simpler way to lift passenger seats from the factory
floor to the airplane door.
“We stopped at a carnival and watched the way Ferris
wheel seats move upward,” says Larson. “We looked
at ski lifts and considered roofing material loaders. We
went to see how sugar beets are loaded, and then we started
looking at farm equipment.”
Larson, who lives in rural Washington, had seen hay elevators
operating on neighboring farms--lifting individual hay bales
up into barn lofts. He knew the elevators had potential
for other uses and began visiting farm equipment dealers
and scrap yards to determine what was available.
The quest for one that could be modified to lift airplane
parts eventually led to Jack Wheatley, a rancher at the
Level Best Ranch. “Once Wheatley got our specifications,
he made a custom elevator in three days,” recalls
Larson.
To meet safety re-quirements, Harms added guards, top
and bottom fixtures, and tracks. The seats, which had wheels
attached, could be rolled onto the elevator and up to the
airplane.
Before the team’s efficiency efforts, the process
for loading passenger seats onto each airplane was cumbersome.
After seats arrived at Boeing, wheels were attached to each
seat and then delivered to the factory floor in a large
container. An overhead crane lifted the container from the
factory floor to a mezzanine. Seats were unloaded and rolled
through the airplane door, where the wheels were removed
before installation. The crane then delivered the empty
container to the factory floor, lifted the next container
onto the mezzanine. The entire process took 12 hours.
Using the hay loader construct, seats roll across the
floor to a holding area near the airplane. When it’s
time for installation, the seats are rolled to the seat
loader, which carries them up to the airplane door. The
process takes about two hours and eliminates the need for
cranes, a common factory bottleneck.
Once the 757 seat loader was in operation, word reached
the Boeing 737 assembly line in the next building. Soon,
members of the 737 Moonshine Shop team came to watch it
operate. The team members suggested some improvements to
the design, and it wasn’t long before they were using
one too.
Soon, Moonshine Shop teams for the Boeing 767 and 777
were working with Wheatley to build seat loaders based on
the previous prototypes. Two years later, the airplane production
lines are still using the modified farm machines. However,
continuous improvement is the goal of the Moonshine Shop
teams. Today, Harms is at work on a new seat loader that
will cut production time by eliminating the need for wheels
to be attached and removed from the seats before they’re
loaded.
“The philosophy of lean manufacturing is lifelong
improvement,” says Larson. “The need for innovation
never ends.”
New Standard Aims to Control Measurement
Processes
All
the quality processes in the world won’t help a company
whose measuring equipment and measurement processes are
out of control. Especially in manufacturing, maintaining
accuracy in measurement equipment is essential to ensuring
a quality end product. The ISO 9001:2000 standard calls
for organizations to have some form of measurement process
control in place. To help fulfill that requirement, the
International Organization for Standardization has released
ISO 10012:2003.
The standard specifies the requirements for a measurement
management system that can be used by an organization performing
measurements as part of the overall quality management system,
and for ensuring that metrological requirements are met.
ISO 10012:2003 is useful for organizations struggling
to meet the requirements for measurement and measurement
process control in ISO 9001:2000 and ISO 14001:1996, although
its use is not a requirement of either. It can also be implemented
independently of these standards.
“ISO 10012 is intended to support meeting ISO 9001:2000
requirements for ensuring that a product conforms to specifications
by measuring the product’s physical characteristics,
such as length, width, thickness or other properties,”
says Dan Harper of the ISO working group that developed
the new standard.
The standard is intended for situations in which customers
and their suppliers need to specify product characteristics
as a technical reference guide or a tool in assessing and
auditing management systems. Its use in third-party certification
is not a requirement but a matter of agreement between the
interested parties.
The new standard replaces ISO 10012-1:1992 and ISO 10012-2:1997.
By merging the scopes of application of these earlier standards--equipment
and processes--in a unique document and integrating the
process-based approach of the ISO 9000:2000 series, ISO
10012 constitutes a comprehensive measurement management
system.
ISO 10012:2003, Measurement management systems--Requirements
for measurement processes and measuring equipment includes
requirement clauses followed by text boxes containing relevant
guidance. It was developed by ISO technical committee 176
and is available from ISO national member institutes. For
more information, visit www.iso.org.
Document Management Firm Implements Six
Sigma
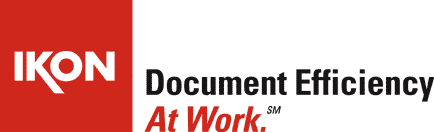
IKON Office Solutions, the
largest independent distributor of document management products
and services in the United States, has plans to develop
and implement a Six Sigma initiative to drive increased
customer satisfaction and process improvement. IKON executive
Andrew Twadelle will lead the program as vice president
of Six Sigma.
“IKON is focused on the needs of today’s businesses,
and we are working to align our internal structure and our
processes to best meet our customers’ needs and grow
shareholder value,” says Matthew J. Espe, CEO of IKON.
“Six Sigma is an extremely powerful methodology that
has proven to increase customer satisfaction and overall
productivity in many of today’s leading businesses.
Six Sigma can be equally effective for IKON.”
Twadelle has experience in corporate governance, reengineering
and customer-focused process improvement. In his most recent
role as vice president of internal audit at IKON, he applied
corporate governance practices throughout IKON while also
driving key business initiatives and process changes for
the company. Prior to joining IKON, Twadelle was director
of enterprise risk services at Deloitte & Touche LLP,
where he worked with Fortune 500 clients to identify and
manage risk related to strategic, tactical, process and
system areas.
IKON veteran Neil Daniels will take over Twadelle’s
previous position as vice president of internal audit. Daniels
will lead IKON’s efforts to support efficient operations,
accurate financial reporting and compliance with regulations.
IKON Office Solutions is a leading provider of products
and services that help businesses manage document workflow
and increase efficiency. Learn more at www.ikon.com.
Interoperability Could Save the Auto Industry
Millions
One of the most common reasons
for slow manufacturing processes is miscommunication. However,
with the aid of Internet technology, this problem is being
addressed by many industries looking to speed production.
In particular, the automotive industry is the subject of
an interoperability project that could save millions of
dollars per year.
The Automotive Industry Action Group is exploring the
interoperability of automated inventory visibility systems
that would allow companies to seamlessly communicate demand
throughout the supply chain, resulting in an estimated net
savings of $225 million, according to the Inventory Visibility
and Interoperability project team at AIAG.
The IV&I project, sponsored by AIAG, the Original
Equipment Supplier Association, and Odette, an industry
association of European automotive manufacturers and suppliers,
will eliminate the need for companies to maintain costly
multiple software applications to support making inventory
replenishment decisions.
“Our focus is to provide value for the automotive
supply chain,” says Linda Plawecki, AIAG’s executive
director. “Our members see the clear need for open
standards and are willing to provide the resources to accomplish
it, so we’ve put this project on the fast track.”
Many tier 1 and tier 2 automotive suppliers are in the
process of implementing Web-based inventory visibility tools.
In addition, some OEMs have developed their own fulfillment
tools. Suppliers are often required to subscribe to and
support multiple tools, increasing their operations cost
and complexity.
“In today’s uncertain economic environment,
companies may be trying to trim budgets here and there while
wasting hundreds of millions of dollars on processes,”
says Darrell Schwartz of Metaldyne, an AIAG member company.
“By tackling the complex issue of inventory visibility
and interoperability, AIAG is addressing a key process issue
that will yield cost savings throughout the supply chain.”
Upon completion of the IV&I project, customers and
suppliers will be able to view and share identical business
information regardless of the software packages used by
either company. Data will be shared in a secure environment
using a standard automotive electronic format that can be
accessed using a browser or integrated into a company’s
applications. AIAG has also entered into a strategic alliance
with the National Institute of Standards and Technology
for this project. The NIST interoperability test bed will
be used for the proof-of-concept phase of this project later
this year.
For more information, visit www.aiag.org.
Biotech Firms Can Have Too Few or Too
Many Quality Personnel
Amid
increased regulation and the U.S. Food and Drug Administration’s
scrutiny over manufacturing and quality control processes,
global pharmaceutical and biotech leaders must find an even
balance between devoting too many or too few resources to
quality management. A recent study by pharmaceutical research
firm Best Practices LLC, claims that top performing pharmaceutical
companies have found that balance by hiring the right number
of top-performing personnel.
The study has identified some of the latest benchmark
trends in quality organizations, staffing and execution.
The findings highlight how leading pharmaceutical and biotech
companies utilize appropriate quality staffing and effective
structures to optimize productivity, reduce costly rework,
increase operational improvements and boost bottom-line
savings. For example, extensive research uncovered these
quality staffing findings:
The average number of quality personnel per plant ranges
from 33 to 131, a fourfold difference that significantly
affects costs.
Benchmark companies cross-train other employees to increase
the number of qualified employees and reduce dependence
on quality personnel.
“We’ve found that organizations can have too
few or too many quality personnel,” says Keith Symmers,
vice president of Best Practices LLC. “Additionally,
it’s been demonstrated that you cannot hire your way
out of poor quality. The right staffing levels accompanied
with robust quality training for the whole company and supporting
systems are essential in avoiding the pain of poorly executing
on the quality front.”
The leading practices, lessons learned and benchmark metrics
in this consulting analysis were drawn from interviews and
benchmarking surveys with quality executives at nine leading
pharmaceutical organizations. The study describes the organizations’
tactics, including tips for managing quality control personnel,
sample rooms, team-based work stations and lab supervisors.
For more information, go to www.best-in-class.com/q/q27.htm.
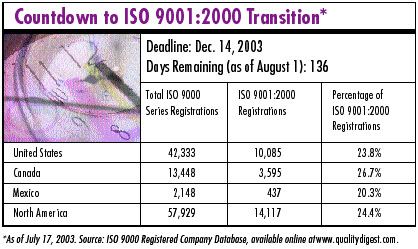
Note: These numbers are artificially low, perhaps due
to outdated registrar data. This month’s Quality Digest
ISO 9001:2000 Transition Survey shows that 53 percent of
registered companies have transitioned to ISO 9001:2000.
For more information, see “ISO 9001:2000 Transition
Survey.”
INDUSTRY NEWS
DNV Certification Inc. has been approved by the California
Energy Commission and California Climate Action Registry
to provide independent certification of greenhouse-gas emissions
on behalf of CCAR participants.
The CCAR has certified DNV to measure GHG emissions, establish
baseline emissions and report annual emission results. DNV
is the second company to become a participant registrar.
For more information about DNV Certification, visit www.dnvcert.com/cc.
The Yale New Haven Health System has selected Instantis
to automate its Six Sigma project management and knowledge
sharing across the organization.
Instantis’ Six Sigma project lifecycle management
system will augment a Six Sigma improvement methodology
introduced to YNHHS in 2001. The program, targeted at delivering
safer, higher quality care and service to patients and other
customers while managing resources more efficiently, will
use Instantis’ application to improve Six Sigma idea
selection, project management and tracking, communication
of results, knowledge sharing and best practices. Learn
more at www.instantis.com.
FARO Technologies Inc. has released two of its portable
coordinate measuring machines in a single package, uniting
the company’s platinum FaroArm control station, a
long-reach probe featuring six degrees of freedom, with
the FARO Laser Tracker Si, with a range of 230 ft. Both
systems share the same CAM2 Measure software.
The FARO Combo sells for $20,000 less than the cost of
purchasing the technology separately. “Combining these
two technologies creates an immediate ROI,” says FARO
hardware product manager Shaun Mymudes. “For the first
time, manufacturers have the ability to measure anything
of any size, anywhere, simultaneously, with no line-of-sight
limitations, and all on the same software interface.”
Details are available at www.faro.com.
Software
Certifications has initiated a new program to crack down
on communication and control failures within large systems-development
projects, the primary responsibilities of software project
managers.
The certified software project manager program is available
to qualified individuals under a skills and experience provision.
Examinations will commence Jan. 1, 2005. The program will
be sponsored by the Quality Assurance Institute certification
board and administered by the QAI professional certification
division. For more information, visit www.softwarecertifications.com.
Two direct mail processing facilities of Harte-Hanks Inc.
have been certified by the United States Postal Service
for compliance with its Mail Preparation Total Quality Management
program. The facilities are the first of their kind to earn
the MPTQM quality distinction.
The MPTQM process is a systematic prevention-based approach
for managing the quality of the mail preparation process.
Formulated by the USPS and an advisory group of mailers
and mail service companies beginning in 1995, MPTQM certification
is based on performance criteria related to ISO 9000, total
quality management and the Baldrige National Quality Program.
For more information, visit www.harte-hanks.com.
Troemner Inc., a provider of weight, mass and standards
calibration services, now offers temperature calibration
services for resistance-type measuring devices. Troemner
can tailor a temperature calibration to suit SPRTs, RTDs
and thermistors, from 196° to 700° C. Primary fixed-point
calibrations are available for calibrating in-house temperature
standards and high-precision devices. Secondary comparison
calibrations for less precise temperature devices are also
available.
The temperature laboratory is ISO/IEC 17025-compliant
with primary standards directly traceable to NIST. Troemner
is currently applying for NVLAP accreditation. For more
information, visit www.troemner.com.
The corporate headquarters and primary production facility
of Metrologic Instruments Inc. have been registered to ISO
9001:2000. The registration is part of a list of goals that
included the launch of several new point-of-sale and industrial
products intended to increase Metrologic’s market
share and sales.
Metrologic Instruments manufactures imaging systems using
laser, holographic and vision-based technologies, high-speed
automated data capture solutions and bar code scanners.
Learn more at www.metrologic.com.
|