by Scott Robinson
Manufacturers strive to avoid difficult gauging situations by enforcing strict quality control processes that begin with ensuring that their gauges are properly calibrated to international standards of measurement. For best gauging practices, manufacturers start by applying primary standards for measurement and inspection that will ultimately lead to consistent, reliable gauging results. Further, they use proper care and maintenance procedures to maintain accuracy and provide long tool life.
Precision gauge blocks are the primary standards vital to dimensional quality control in the manufacture of interchangeable parts. These blocks are used for calibrating precision measuring tools and for setting numerous comparative-type gauges used in incoming, production, and final inspection areas. Gauge blocks provide the most economical, accurate method of setting dial test indicators and other gauges used in conjunction with surface plates for inspecting parts with exacting tolerances.
Gauge blocks consist of a hard, stable material with a flat, parallel gauging surface on each side. The measuring surfaces are ground and lapped to an overall dimension with a tolerance of plus or minus a few millionths of an inch. Gauge blocks may be stacked or “wrung” together to form accurate standards of practically any length.
They are made in several grades or degrees of accuracy. Grade 0 is the most popular grade of gauge blocks, as this grade is usually suitable for most applications and offers the best combination of accuracy and cost. Higher-accuracy grades of blocks, such as Grade 00, are primarily used as masters to check other gauge blocks and for applications that require extreme accuracy. Grade B (±50 µin.) blocks are relatively inexpensive but are limited to workshop use where exacting accuracy is not required.
Gauge blocks are available in various materials. For instance, Starrett-Webber’s croblox brand of gauge blocks are made of chromium carbide, which is long-wearing, dimensionally stable, and extremely corrosion-resistant. Croblox gauge blocks will maintain their accuracy many times longer than steel blocks. Croblox gauge blocks are available in B89 Grades 00 and 0.
Another material option is ceramic gauge blocks, which are long-wearing and corrosion-resistant. Ceramic gauge blocks fill the gap between steel and croblox and are available in Grades 00 and 0. These blocks have favorable mechanical and thermal properties that compare the closest to steel of any alternative gauge block material.
Steel is the most economical gauge block material available, and steel’s thermal and mechanical properties are adequate in typical workshop environments. The main disadvantage of steel is its susceptibility to corrosion.
Various styles of gauge blocks are available, including rectangular, square, and heavy duty. The use of gauge blocks can also be extended by means of accessories that can be used with height gauges, snap gauges, scribers, and dividers.
Every linear measurement depends on an accurate reference surface from which final dimensions are taken. Precision granite surface plates provide the best reference plane for work inspection and layout prior to machining. They are also ideal bases for making height measurements and gauging surfaces, parallelism, etc. A high degree of flatness, stability, overall quality, and workmanship also make them ideal bases for mounting sophisticated mechanical, electronic, and optical gauging systems.
The most important element in the performance and life of granite surface plates is the percentage of quartz that is present in the stone. Quartz is more than twice as resistant to wear as the other minerals in granite. It provides bearing points that have a hard, highly polished, smooth character, and that protect the accuracy and finish of the surface plate and the tools and instruments used on it.
For example, Starrett offers pink granite, which has the highest percentage of quartz of any granite. Starrett’s charcoal-black granite also contains quartz, although a slightly lower content than pink. Higher quartz content means greater wear resistance, and the longer a surface plate holds its accuracy, the less often it will require resurfacing.
Surface plates without work-clamping ledges are recommended for sustained accuracy and reliability. Ledges are for work-clamping purposes only. If excessive torque is used when applying clamps to ledges, it can adversely affect measurements taken near the plate edges. If clamping is important, T-slots and threaded metal inserts may also be installed in the surface.
Some applications may warrant customized, special plates. For example, a custom-made plate might be needed for inspecting oversize parts and assemblies, such as diesel engine blocks and crankshafts, vehicle frames, missile components, and ground-support equipment. Or perhaps a special plate or a modification to a standard plate might be required for work-holding attachments, such as threaded inserts, studs, adaptor holes, T-slots, and dovetails.
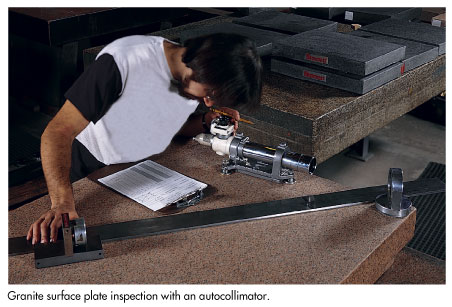
Granite surface plates are manufactured in three accuracy grades, including:
• AA. A laboratory grade typically specified for precision operations in constant-temperature gauging rooms and metrology departments
• A. Inspection grade typically specified for general work in quality control
• B. Toolroom grade typically specified for production checking work throughout the shop
All surface plates must pass a critical final inspection to prove that their surfaces are within the specified tolerance. The final inspection is typically done with an autocollimator in a controlled atmosphere. This instrument is checked and certified against standards traceable to the National Institute of Standards and Technology.
Because standards are so critical and form the basis for all precision measurement, extra care and regular inspection should be taken to ensure that they are accurate.
Wringability is a key test for evaluating the integrity of the surface condition of a gauge block. Wringability may be defined as the ability of two surfaces to adhere tightly to each other in the absence of external means, and is an important property of gauge blocks. Blocks that don’t wring may give erratic and unreliable results and should be replaced.
To prepare gauge blocks for wringing blocks must be free from nicks and burrs, because imperfections on one block may damage the surface of the other block. Blocks may be checked for defects with a gauge block stone before wringing. A stone with serrated grooves is recommended because it gives a better “feel” for nicks and burrs that catch the edges of the serrations.
The stoning process removes a small amount of raised material, improving the repeatability of readings and providing block sizes that appear to be truer to their original tolerances.
To wring gauge blocks, all surfaces must be clean. An oiled wring pad can be used for wiping the surfaces of the blocks. Next, a dry pad can be used to remove as much oil as possible. The blocks should then slide together without any bumps or scratching, and should adhere to each other strongly after being rotated into place.
Formal tests exist for testing wringability if a problem with the block is suspected. Tests may be done by the user of the blocks and do not require a laboratory. Wringability is an important property of gauge blocks, but is fortunately a quality that can be controlled and monitored readily by the user of the blocks. With proper use and care, gauge blocks will provide long, reliable, accurate service.
The granite surface plate is a precision piece of equipment and as such, must be properly installed and maintained. The plate should always have a reliable support system furnished with it. Typically this is a hard rubber pad attached to the bottom of the plate, forming a nondistortable three-point support system. The pads are installed during manufacturing, and the plate rests on them throughout lapping, inspection, and shipping. They are a critical factor in surface plate accuracy and must not be removed. Plates up to and including 6 feet wide by 12 feet long should be furnished with this nondistortable three-point support system. When mounting the plate on a stand, be sure that only the pads are resting on the stand. Never support the plate by the ledges or under its four corners, because this will completely void any guarantee of accuracy.
Plates larger than 6 feet wide by 12 feet long are supported on multiple support points (six or more points) consisting of granite pedestals and leveling wedges. The number of support points and positioning are determined by the size of the plate.
Nylon slings are highly recommended when lifting the granite. If a forklift must be used to move the granite surface plate, a protective padding should be placed between the metal forks and the granite.
Once set up, plates don’t require extensive care and maintenance. Keeping the surface clean and free from dust, dirt, grease, grime, and other foreign particles will maintain accurate tool readings and extend the life of the plate. Environment and usage have much to do with the frequency of cleaning. However, as a rule, it is recommended to clean a plate daily if it is used each day. If the plate is not used for an extended period of time, it should be covered with a surface plate cover.
There are some dos and don’ts for using granite surface plates. Don’t use granite surface plates as workbenches or lunch tables. Dropping wrenches or hammers on plates can chip and nick the surface, and spilling coffee or drinks on granite can cause permanent stains. Grease from food particles will do the same.
Work pieces to be measured must be set down gently on the plate, because a sudden jolt or blow to the plate with a heavy metal object can chip or nick the surface. Also, when inspecting work pieces, especially small parts, it is a good idea to use different areas of the surface plate because using the same spot over and over, year after year, will wear that area of the plate.
Surface plates should be checked on a regular basis for wear using a repeat reading gauge with a manual indicator. Generally, long before a surface plate has worn beyond specifications for overall flatness, it will show worn or wavy spots, which will produce measurement errors. The reading gauge will readily detect these error-causing areas.
Simply set the gauge on the plate and zero it at any point on the table. Move the gauge over the plate, and if the indicator moves more than 0.000025 in. for an AA plate, 0.000050 in. for an A plate, or 0.000100 in. for a B plate, then the plate may have some high and low spots and be out of tolerance. Specifically, the tolerance must repeat from side to side within the specified tolerance range to be an accurate plate.
An effective inspection program should include regular checks with an autocollimator to provide actual calibration of overall flatness traceable to NIST. If tolerance variations are excessive, the plate can be transferred to work involving less accuracy, or it can be resurfaced to restore its original level of accuracy. Outside facilities or manufacturers are available to assist with the resurfacing process.
Manufacturers that produce the highest quality products use the best quality control practices. The quality of products is only as good as the accuracy and reliability of measurements.
This begins with relying on primary standards to ascertain that gauges are properly calibrated and are being used to check parts on optimal work surface conditions. Due to a number of factors, including shop contaminants, normal wear and tear and more, gauges require regular calibration. By checking gauge readings and accuracies with gauge blocks and ensuring a reliable reference by using granite surface plates, manufacturers have the essential tools and methods for maintaining primary standards that will ultimately lead to reliable gauging and better quality parts.
Scott Robinson is a seasoned veteran in the mechanical and precision tool and gauging fields, including his current role as technical support manager at The L.S. Starrett Co. He has been with Starrett for 37 years. Prior to that, Robinson held technical and research and development positions in various industries, including aerospace. Visit online at www.starrett.com.
|