by Jeff Nestel-Patt
Other industries, such as automotive, should look at the way semiconductor manufacturers have integrated automation into the production environment to find answers to their soaring warranty recall costs. According to AMR Research, vehicle manufacturers claim to have fully functional solutions that can detect quality problems, but unfortunately it may take them up to 220 days after the vehicle has left the plant before they figure out they have one. That’s why in 2004 North American auto manufacturers recalled more vehicles than they made. Early warning track-and-trace systems can analyze vast amounts of data to minimize recall costs. Real-time manufacturing software utilizes the process/product /people data it collects to determine the source of a manufacturing problem (for example, over-torquing a bolt at a machine station).
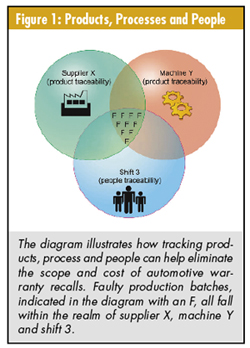
Figure 1 uses a Venn diagram to show incidence reports related to a recall. Note that all of the faulty products can be traced to supplier X (green circle). A track-and-trace system can limit the recall to parts provided by supplier X. Note also that all faulty parts had machine Y in their process plan (brown circle). Thus process traceability would be able to further limit recalls to supplier X parts that were assembled on machine Y. Finally note that all faulty parts were produced during shift 3 (blue circle). In this example, the faulty parts resulted from an individual manually over-torquing a bolt at machine Y on the third shift. A warranty or recall action could be focused specifically to just those parts, saving the manufacturer millions of dollars in recall costs.
Based on a sense-decide-respond approach, a flexible and configurable track-and-trace solution can achieve a wide range of benefits for automotive and other discrete manufacturers. These benefits fall into a number of categories, including improvements in exception management, overall equipment effectiveness (OEE) and overall factory effectiveness (OFE); quality improvement; user empowerment; lean manufacturing; enterprise performance management (EPM); and supply chain execution (SCE). For exception management, the system senses, in real time, the process, product and people “faults.” This means further processing and/or shipping can be stopped to minimize any corresponding scrap and/or future warranty issues. This early-warning capability can then be linked with other applications to decide how to reconfigure the system to maintain factory goals. With respect to OEE and OFE, the availability of traceability data allows the user to evaluate metrics on a real-time basis and drill down to investigate nonoptimal and suspect operations to determine root cause and decide on the appropriate improvement processes. A track-and-trace solution serves as a key enabler for lean manufacturing by tying components such as productivity monitoring into a factorywide data collection and management infrastructure. EPM is supported by providing a complete data collection and analysis infrastructure across all processes and from low-level sensors up through high-level factory management systems. Finally, the breadth of data collection, storage and management supports SCE initiatives such as warranty cost reduction by reducing the scope of a recall.
|
There's an old story that's made the rounds of the semiconductor industry about the fully-automated, lights-out semiconductor fab of the future. It will be staffed by a man and a dog. The man will be there to feed the dog, and the dog will be there to keep the man from touching the equipment.
Whether or not we eventually see true lights-out manufacturing, the story speaks to how chipmakers have willingly embraced automation as a strategic component of their manufacturing operations to help improve yields, increase overall factory effectiveness, and achieve the profitability and return on investment (ROI) targets necessary to remain competitive.
The world's most complex manufacturing environment is probably the most automated as well, and for good reason. Manufacturing semiconductors in new, state-of-the-art, 300 mm (approximately 12 in., which refers to the silicon wafer upon which the chips are manufactured) fabrication facilities or "fabs" (the industry has always shunned the term "factory") is more complicated than ever. This has been driven partly by necessity because much of the manufacturing takes place in vacuum environments where human contact with the work in process (WIP) is impossible. Ergonomic factors require high levels of automated material handling to eliminate damage to WIP caused by human operators. Managing the complex processes and workflows requires highly reliable, fabwide software systems. As a result, manufacturers quickly discovered the hidden value of real-time manufacturing data. By making the data available to other production systems, such as equipment maintenance or higher-level business systems enterprise resource planning, manufacturers can create real strategic value for their organizations.
A high-volume, 300-mm fab can cost upwards of $3 billion. The vast majority of that capital investment is spent on the processing tools used in manufacturing the chips. A single lithography tool can cost $20 million, and a fab might be equipped with as many as a dozen of them. A high-volume fab starts 30,000 to 40,000 wafers every month. A wafer will travel upwards of 12 miles from start to finish as it moves in its maze-like, 45-day journey through the fab. The latest generation of microprocessors can have as many as 30 different layers of circuitry. As each layer is added on top of the previous one, the wafer is painstakingly and exactingly moved in and out of the expensive tools (e.g., ion implant, lithography, deposition) as many as 600 times. It's a huge
material-handling nightmare to keep track of and monitor the quality of the wafer lots as they move through production. Without highly reliable wafer-handling robotics and robust manufacturing software, production volumes would drop significantly, and the wait for a new PC or hand-held device would be measured in months instead of days. It's no coincidence that manufacturing execution system (MES) software was quickly adopted by the semiconductor industry beginning in the early 1980s.
The wealth of manufacturing data spawned the development of other value-added applications that drove further value in manufacturing operations. MES captures real-time manufacturing data with minimal configuration, and maintains records of products and processes by unit, subassembly and lot. WIP is tracked at each station, and the data are transmitted to an online tracking system that records and tracks all material movement within the plant. The data are fed into a statistical process control application that checks whether the data are in spec and analyzes whether the process is in control. This is performed throughout the process, and all the data are stored in a central repository.
Fault detection and classification software allows factory personnel to obtain instant access to equipment health data and alarm logs, including drill-down capability into equipment and sensor data for troubleshooting. The ability to access specific tools and alarm data facilitates high-level reporting as well as low-level equipment diagnostics. Data visualization through user-configurable dashboards and scorecards enable factory personnel to monitor the manufacturing and quality data that are important to them. Whenever a manufacturing parameter goes out of spec or a machine or tool malfunctions, these applications ensure that otherwise hidden problems in the manufacturing process are discovered early, well before product quality is put at risk or a faulty unit leaves the factory.
Chipmaking has always been about the chemistry and physics associated with the increasingly complex processes required to manufacture each successive semiconductor generation. Little did Gordon Moore realize when he postulated his now-famous Moore's Law back in 1965 that he'd be defining the industry's performance benchmark for decades to come. Moore postulated that the number of transistors on a chip would double every 18 months, giving rise to higher levels of power and functionality. With uncanny accuracy and totally unanticipated longevity, Moore's Law has been the standard by which the semiconductor industry has measured itself ever since. To maintain the technological innovation outlined in Moore's Law, the industry has not only had to develop new process technology (i.e., the physics and chemistry) needed to achieve the functional requirements of each new generation of semiconductor, but also the sophisticated software and automation systems required to manage and control the increasingly complex production facilities where these chips are produced.
Producing high-quality semiconductors has been a challenge from the beginning. In the early days, semiconductors were less complex, and the silicon wafers were much smaller, measuring only 3-4 in. in diameter. Chip yields on the wafer were extremely low (approximately 50-60 percent). Loading a process tool was done manually. A technician, using a pliers-like wand, would grab the edge of a wafer and place it in the tool. During the late 1970s, robotic technology was developed that began to automate many of the manual wafer-handling procedures in an attempt to improve yield and increase tool throughput. At this point automation was still seen as an enabler to better tool performance measured by improved yields and throughput. A broader fabwide view of automation as a strategic contributor to enterprise performance was still to come.
Something else happened that would accelerate both the growth of semiconductors and the automation needed to manufacture them: Our appetite for all things digital exploded. The percentage of silicon content in electronic devices really started to take off during the early 1990s, and this drove manufacturers to find new ways to meet the demand. The average personal computer made in the mid-1990s had more computing power than what was found on the Apollo command module that went to the moon. Semiconductor manufacturers answered by building more fabs, shrinking the circuitry to smaller dimensions and increasing the size of silicon wafers from 4 in. to 6 in. and then to 8 in., which has been the production standard from the 1990s to today. The larger size, of course, meant that more chips could be produced on a single wafer. The shrinking circuitry dimensions meant that more transistors could be designed into a single chip, thus allowing it to run faster and accomplish more tasks. Moore's Law was alive and well.
Each successive semiconductor generation meant new process technology was needed to produce it, so fab design favored highly compact process bays of expensive capital equipment arranged by the various process steps. The cost of outfitting a new fab reached astronomical numbers, and manufacturers were driven to achieve the shortest possible ROI.
Inside the fab on the production floor, processes were getting more complicated. With all the WIP moving through the fab, it was no longer enough to simply optimize a single tool or process bay for optimal throughput. Achieving overall factory effectiveness meant finding ways to ensure that the right wafer was at the right tool at the right time. To achieve that, manufacturers needed to simulate, schedule, dispatch, execute and track all those wafers in real time. They also needed to find new ways to monitor and control the processing going on inside the tool itself to ensure tool performance. Additionally, as the wafers started getting bigger, ergonomic factors prevented workers from handling the material. Automation was no longer an option; it was an operational necessity driven by increasing complexity in the production environment and business drivers to achieve higher ROI.
The answer to these challenges was robust, highly reliable automation software. The cost of lost production in a fab is measured in millions of dollars per hour, so a fab can't go down. MES software allowed manufacturers to implement execution control over the critical shop-floor production processes. Equipment engineering software for SPC and advanced process control allowed manufacturers to determine when a tool was drifting off its intended process specification and catch quality problems before they occurred. Manufacturers implemented fabwide automated material handling systems (AMHS) that incorporated radio frequency identification technology to automate the scheduling and delivery of wafers directly to the load port of the process tool. Modeling and simulation software allowed manufacturers to model the entire fab layout for optimizing clean-room space, the placement and number of process tools, and the routing of the AMHS systems for quickest delivery times. Not surprisingly, yields began improving, and overall fab productivity increased.
With production yields now approaching the high 90-percent range, manufacturers are looking at ways to achieve more efficiency and profitability from their manufacturing operations. The answer is to automate more of their production to optimize their capital-intensive manufacturing assets and link those systems with other enterprise business systems to drive better business decision making. It would be impossible to operate a modern, high-volume production fab without the high levels of automation deployed in these environments today.
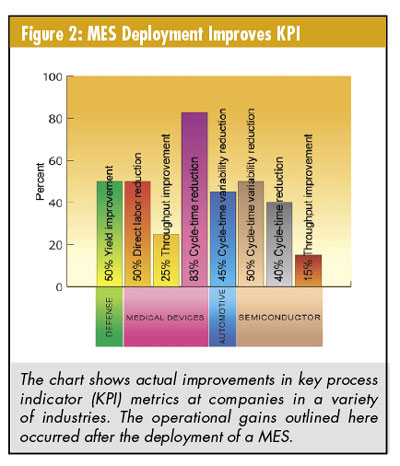
At the recent Brooks Software Worldwide User Conference, Bill White, CIO for Amkor, one of the world's largest back-end semiconductor test, assembly and packaging companies, told the audience that his company has more than 1,500 different packaging solutions to meet their customers' requirements. Their biggest challenge is having enough visibility into the order pipeline so they can have the right product available when the customer wants it. After all the investment in information technology (IT) during the past few decades, companies are still asking the age-old question: "What should I make?"
Manufacturers are now realizing that to achieve the ROI in business and IT systems, they must integrate their manufacturing operations with other business-level systems to drive the visibility from the shop floor to other parts of the enterprise. The goal is to bring the visibility of market dynamics to the manufacturing floor in real time. Many of the components to achieve this goal are already in place. Again, the semiconductor industry has set the bar for how manufacturing automation can help large, complex manufacturers connect the disparate parts of their organizations into an adaptable, real-time enterprise.
Adaptive Automotive (a fictional company) has multiple suppliers, customers and manufacturing sites for their products. Figure 3 below shows their distribution chain, two manufacturing sites running different manufacturing execution systems (MES) or shop floor systems and a third-party supplier who is also using a different MES system. Prior to implementing their supply chain execution (SCE) solution, they struggled with getting a consolidated view of their entire operations.
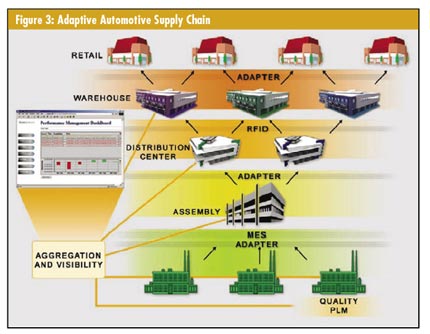
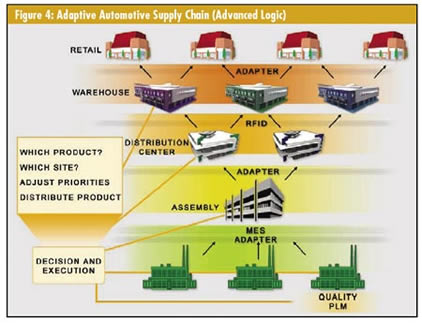
Their SCE system has real-time adapters that continuously stream current information from their various enterprise systems and aggregate it into a common data model that's used for compiling real-time reports to a Web-based dashboard.
Adaptive Automotive also uses the dashboard to provide alerts if any of the real-time data indicates an exception has occurred. The company can now recognize problems immediately and has instant access to the most current enterprise information through consolidated reports. This allows for quick analysis and resolution.
Armed with real-time data from its supply chain, Adaptive can use more advanced logic to make challenging product-routing decisions between sites, as shown in figure 4. For example, if the third-party supplier falls behind on a certain part because of an unexpected machine outage, the system's
decision-and-execution capability sees this exception as it occurs and begins to take action. The system can be configured to automatically act on a decision (to prevent any delays from occurring) or to present the options and wait for confirmation before execution. The execution commands are then sent directly to the different manufacturing systems for immediate problem resolution in minutes or even seconds. Now Adaptive is reducing its WIP and, as a result, driving a shorter lead time.
Adaptive is starting to see measurable improvements in its most important key process indicators (KPI). The company's manufacturing and assembly sites adjust priorities and product based on demand-driven changes in the market. Adaptive's real-time manufacturing applications let all its sites seamlessly share tool setup data, tracking data, quality information, order information, lot history, and bills of materials regardless of the shop floor or manufacturing system used at each site. Multiple sites can operate as a single entity, ensuring the optimal use of all resources at the sites. Adaptive's global manufacturing environment is fully collaborative, both internally and with its extended supply chain and customers. The company provides ultimate efficiency and the ability to react in real time to changes in both the supply chain and demand.
As demand for more intelligent electronic devices continues to soar, average selling prices for chips continue to fall, and consumers receive the benefit. The laptop I used to write this article costs only a fraction of what it did five years ago, but it's equipped with far more computing power. The cell phone sitting on my desk has a product life measured in months, not years, and came free with my service contract.
The global market is changing rapidly, and only those companies that can establish an adaptable manufacturing environment capable of responding in real time to changing market demands will survive. Real-time manufacturing data can no longer be isolated within the four walls of the plant because the definition of the shop floor is changing. High-tech brand owners today outsource the manufacture of their products to a series of global contract manufacturers that must produce high-quality products and deliver them on time. Government agencies are driving life sciences companies to implement good manufacturing practices into their manufacturing operations to comply with government regulations. Automotive manufacturers are trying to drive down the cost of warranty recalls by implementing early-warning systems that catch quality problems before vehicles are shipped to the dealer.
I recently attended a large medical device trade show and asked one of the attendees who stopped by our booth what kind of manufacturing execution system his company had in place to manage production. He told me they have programmable logic controllers that collect equipment data, and that they produced spreadsheets to track production. I was reminded of that semiconductor technician sitting at his process tool back in the mid-1970s, grabbing 3-in. silicon wafers by hand and feeding them into the most advanced process tool of the day. I asked the attendee if he was interested in automating his production with a more comprehensive MES. "I don't think we can afford not to," he said.
Jeff Nestel-Patt is the director of marketing at Brooks Software, a division of Brooks Automation, a leading provider of real-time applications for discrete manufacturers around the world. He has more than 20 years of high-technology marketing experience for a number of companies, including Digital Equipment Corp., EMC Corp., Danaher Motion and PRI Automation. Brooks Software supports enterprise initiatives such as lean manufacturing, supply chain execution, enterprise performance management and close-loop automation.
|