by John E. (Jack) West
Last month's "Standard Approach" column ("Many Stand-ads, Few Volunteers," July 2005 issue) briefly reviewed key standards that are used to support implementation of ISO 9001. This article explains several of those documents in more detail.
Many ISO 9001 users indicate that they're not aware of ISO 9004. This is unfortunate because it contains many useful concepts. This standard offers guidance, not on how to implement ISO 9001, but on how to make the quality management system better.
An organization can use ISO 9001 to develop a basic QMS and achieve registration to that standard if desired. Using ISO 9004 together with ISO 9001, an organization can determine the best activities and processes to achieve improvements in performance as well as ensure it meets customer requirements. In theory, conformity to ISO 9001 provides an organization with a basic QMS. ISO 9004 helps the organization make this QMS more efficient and achieve improved results. The concept is illustrated in the figure on the following page and is described in greater detail in Chapter 4 of The ASQ ISO 9000:2000 Handbook (Charles A. Cianfrani, Joseph J. Tsiakals and John E. [Jack] West, ASQ Quality Press, 2001).
The guidance for improvement in ISO 9004 is arranged in the same way as the clauses of ISO 9001, making them easy to use together. In fact, the text of each clause of the ISO 9001 requirements is included inside a box following the related ISO 9004 guidance. For these reasons, ISO 9001 and ISO 9004 are frequently referred to as the "consistent pair."
ISO 9004 can be used as a general guide when QMS processes are developed or improved. The performance improvement guidance is treated like any other improvement input, such as information from textbooks or handbooks, or consultants' advice. Although this is probably the most common use, and plenty of ideas can be found in the document, it might not be the most effective.
A somewhat more effective use is to find ways to fill obvious gaps in a system that must comply with ISO 9001 but doesn't. ISO 9004 offers ideas about implementation that will help the organization focus on improvement. A good example might be a system that doesn't include either measuring customer satisfaction or continual improvement. An organization confronted with this situation will find excellent ideas related to both in ISO 9004.
Perhaps the best way to use ISO 9004 is through self-assessment. An organization can conduct a self-assessment as described in Annex A of that document. The annex provides a simple model for assessing the maturity of an entire QMS, individual functions within the organization or individual processes. One typical use would be to develop a business model for the organization that defines the processes, activities and functions that are most important to success and focus the assessment on those areas. The more focused self-assessment method is probably the best way to use the standard. It has the advantage of zeroing in on what's important in terms of business performance.
ISO technical committee (TC) 176/subcommittee (SC) 2 is now working on specifications for a revision to ISO 9004, which is projected to be issued in 2008. This revision will significantly upgrade the document so that it provides a more comprehensive bridge between ISO 9001 and the assessment criteria of excellence models such as the Malcolm Baldrige National Quality Award. ISO 9004 is a useful tool, and the 2008 version should be even better.
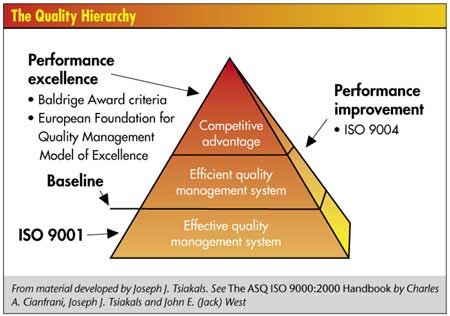
This small family of standards was developed by SC 3 of ISO TC 176 to provide process guidance on what to do when things go wrong. The notion is that customer satisfaction can be enhanced by determining what commitments are made to customers, competently handling customer complaints and providing good processes for resolving disputes. The family is planned to include the following documents:
ISO 10001, Quality management--Customer satisfaction--Guidelines for codes of conduct for organizations (currently at the committee stage)
ISO 10002, Quality management--Customer satisfaction--Guidelines for complaints handling in organizations (currently in the process of adoption as an American National Standard known as ANSI/ISO/ASQ Q 10002:200x)
ISO 10003, Quality management--Customer satisfaction--Guidelines for dispute resolution external to organizations (currently at the committee stage)
This series was inspired by the ISO Committee on Consumer Policy, which requested their development. The ISO Technical Management Board assigned ISO TC 176/SC 2 the task of developing the documents. Although the idea for the documents came from the consumer protection community, the development has had broad input from industry, consumer groups and other potential users.
ISO 10002 was the first of these. It was developed as guidance for an organization's complaints-handling process. It can be used alone or in conjunction with ISO 9001. The document has eight clauses. The first three are scope, normative reference, and terms and definitions. The other five are:
Guiding principles. The general notions upon which the processes for handling complaints should be built. They include visibility, accessibility, responsiveness, objectivity, free-of-charge to complainants, confidentiality, customer-focused approach and accountability
Complaints-handling framework . An explanation of why organizations should commit to effective complaints-handling, and the associated responsibilities and authority. It also describes considerations for developing a complaints-handling policy.
Planning and design. A description of how an organization can plan and design an effective complaints-handling process.
Operation of the complaints-handling process . Guidance for operating the process, from receiving a complaint through closing the issue after completion.
Maintenance and improvement . Guidance on gathering and using complaints data, monitoring performance of the complaints-
handling process, auditing
the process to ensure it meets the organization's requirements and continually improving it.
The standard also has several annexes that provide sample forms and expand on several of the topics in the body of the standard.
ISO 10002 has set the stage for the other two documents, which can be expected to have similar structures.
ISO 10001 is intended to cover codes of conduct that are promises to customers as well as related provisions addressing such items as advertising, pricing, fair trade, timing of product delivery and claims related to particular attributes of a product or its performance. Thus, the standard will cover codes of conduct that involve the organization's relationship with its customers. It's not intended to cover other aspects such as ethical business practices or conduct with fellow employees.
ISO 10003 is intended for organizations that need a third-party process to resolve customer disputes that aren't resolved by their own complaints-
handling process. It will also be of use to organizations that provide third--party dispute resolution.
ISO 10002 is available now. The set should be completed by late 2006, and it should prove useful to organizations needing effective customer codes, complaint resolution and external dispute resolution processes.
This standard is a guide to quality management in the project environment. It doesn't give guidance on project management itself but rather focuses on how the QMS works to provide assurance of project success.
ISO 10006 can be used in a wide variety of situations, for small and large projects alike. The guidance is intended for users who have experience with project management but who'd like to ensure that the concepts of the ISO 9000 series are used in their project. The guidance can be used alone or in conjunction with ISO 9001. ISO 10006 recognizes the unique nature of each project. Unlike most other types of production and service work, projects are unique, have a finite start and finish, and can involve higher degrees of risk and uncertainty. Projects are also often of long duration and subject to changing influences from both internal and external sources. Project managers have a great deal of authority to manage their project as they see fit. Introducing a new project manager has often meant a complete change in direction for managing the project, which makes a guidance document in this area a valuable addition to the ISO 9000 family.
As with ISO 10002, ISO 10006 has eight clauses. Guidance is provided in clauses four through eight:
Quality management system in projects. Describes the characteristics of projects that make them different from other types of work. It discusses typical project phases, processes used to manage projects and using quality management systems in project management.
Management responsibility . Discusses the importance of top management commitment and recommends development of strategic processes of the project so that the project objectives are met. It discusses strategic processes as they relate to each of the eight familiar quality management principles given in clause 0.2 of ISO 9000:
Customer focus
Leadership
Involvement of people
Process approach
System approach to management
Continual improvement
Factual approach to decision making
Mutually beneficial supplier relationships
Resource management. Addresses project-related resource considerations in resource planning, resource control and processes related to project personnel.
Product realization . Provides guidance on important considerations in managing product realization in projects. The guidance covers the following aspects of processes: interdependency, scope, time, cost, communication and risk. The discussion on project risks is particularly comprehensive.
Although this document has been used in the past for traditional project-
management organizations that are involved in processes such as major construction projects, we should remember that many activities in manufacturing and service businesses are actually projects. For example, the development and implementation of a new product or service has the characteristics of a project. Manufacturing and service organizations would be wise to obtain and study ISO 10006, and use it as a tool to improve the effectiveness and efficiency of project implementation.
From the above descriptions, it should be apparent that ISO 9001, although the most well-known standard in the ISO quality management family, isn't the only one. ISO 9001 addresses only the minimum requirements for a QMS. The supporting standards can be effective tools to continually improve customer satisfaction and internal operations beyond the minimum.
John E. (Jack) West is a consultant, business advisor and author with more than 30 years of experience in a wide variety of industries. He is chair of the U.S. TAG to ISO TC 176 and lead delegate for the United States to the International Organization for Standardization committee responsible for the ISO 9000 series of quality management standards.
|