Wanda Ring’s Strategy Goes Awry
Dick Moby, quality assurance czar for a plastics extrusion company in the Midwest, is serious about control charts. He sees data analysis and process control as ways not only to ensure high-quality products for his firm but also to enhance his own career.
Moby personally instructs each new employee in his department on the proper use of control charts, giving them a solid foundation in statistical process control fundamentals. Most recently he’s lavished this attention on Wanda Ring--who also aspires to advance in the organization--and has emphasized the importance of keeping all process data points between the upper and lower control limits. Unfortunately, Moby doesn’t realize that he’s put the process--and his own reputation for quality--into the hands of a tamperer.
Ring is assigned to monitor a series of machines that extrude raw materials used for manufacturing toy parts. She believes that one of these machines isn’t operating with the same consistency that others on the line demonstrate. Because she’s had fleeting experience as an operator prior to being hired by Moby, she’s confident that she can reduce the process variability by making a few simple adjustments in the machine’s operation. The operator advises her not to tamper with the machine because this can contribute to variability in the process, but Ring says she knows what she’s doing. It’s a classic case of a little knowledge being a bad thing.
Ring is using an individual moving average chart. She makes the fateful choice to adopt a decision rule: If a point falls above X-bar, she’ll adjust the operation of the machine downward to compensate for the distance between the data point and X-bar. If a data point falls below X-bar, on the other hand, she’ll adjust the operation upward to compensate.
This, Ring feels, will allow her to fulfill Moby’s instructions to keep the data points within strict ranges. As a logical consequence, it should also help her maintain upward mobility in the company’s corporate hierarchy. She couldn’t be happier with her choice; the results are another matter.
If Ring goes forward with her plan, which of the following results will occur?
a. The variability of the process (as measured by the variance s2) will decrease by approximately 50 percent.
b. The variability of the process (as measured by the variance s2) will increase by approximately 50 percent.
c. The variability (as measured by the variance s2) will remain the same.
d. The variability (as measured by the variance s2) will increase by approximately 25 percent.
Answer b is correct.
By adjusting the process to X-bar, Ring illustrated rule No. 2 of W. Edwards Deming’s “funnel experiment,” which demonstrates natural variability in a process by using a funnel to drop a marble on a target. If the funnel never moved, these marbles would reflect variation because no two would fall in exactly the same position.
If, on the other hand, the funnel is adjusted after each drop, the process would reflect increased variability. What Ring is doing reflects rule No. 2: “At drop k (k = 1, 2, 3…), the marble will come to rest at point Zk, measured from target. Move the funnel distance -Zk from its last position.” (See Deming, W. Edwards, Out of the Crisis, MIT Press, 1982.) Following this rule will increase process variability by approximately 50 percent.
The figures below demonstrate the variability found in Deming’s funnel experiment.
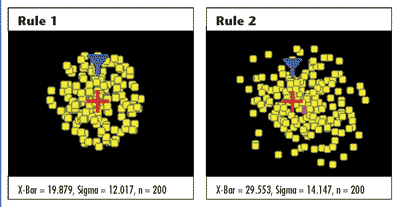
Moby is left shaking his head. Unfortunately, process operators in every environment are tempted to touch dials, either literally or figuratively. Changing a sales process after only one month’s drop, for example, is a related symptom. Overcontrol--i.e., making adjustments to “compensate” for natural variation inherent in a process--is a common error.
What dials have you touched lately?
Michael J. Cleary, Ph.D., founder and president of PQ Systems Inc., is a noted authority in the field of quality management and a professor emeritus of management science at Wright State University in Dayton, Ohio. A 29-year professorship in management science has enabled Cleary to conduct extensive research and garner valuable experience in expanding quality management methods. He has published articles on quality management and statistical process control in a variety of academic and professional journals.
|