Capability Competence
Michael J. Cleary, Ph.D.
mcleary@qualitydigest.com
Rock DeBote, CEO of Greer Grate & Gate, has hit
bottom. Under pressure to produce profits and increase earnings,
he's taken a few small shortcuts--such as reporting several
million dollars as capital expenses--by mistake, of course,
as he's always considered himself an honest man. He'll admit,
however, that he's enjoyed the accolades that have come
his way when quarterly reports showed surprising earnings,
not to mention the substantial bonuses he's earned for keeping
the company profitable. At home, DeBote's also enjoyed the
time spent with his children on his new yacht and the vacations
in Aspen where they all learned to ski while staying in
his vacation house there. "I'm a family man,"
he insists when he's accused of wrongdoing, and he intends
to use this as his main line of defense at his upcoming
trial.
Quality Manager Hartford Simsack, having spent time in
prison prior to being hired by DeBote, has empathy for his
boss's situation--especially because DeBote is also his
brother-in-law. But he worries most about his own vulnerability
with respect to his limited understanding of statistics
and his propensity to fake his knowledge about a variety
of concepts related to statistical process control. DeBote's
replacement, Newt S. Tament, whose integrity is beyond reproach
and whose understanding of SPC has produced a record of
quality successes in several companies, worries him. "I'm
in trouble," Simsack says to himself.
Determined to impress his new boss with his statistical
prowess, Simsack organizes a training session for the entire
quality department. He plans to dazzle the participants
with his terminology, charts and silver-tongued explanations
of complex statistical processes. And, as a courtesy, he'll
invite Tament to the session, but he'll schedule the training
for a time when he knows his boss will be unable to attend,
at the same time there's a planning session at the company's
world headquarters.
Beginning what he hopes will be a scintillating presentation
about capability analysis, Simsack glances around the room
and realizes his boss has somehow made arrangements to be
at the session and is sitting in the back of the class.
"The normal distribution should be--well, normal,"
Simsack begins, hoping that by stating the obvious, he'll
warm up his group a little. He's prepared a canned lecture
that he copied nearly verbatim from a statistics textbook.
After he correctly points out that a process must be in
control before beginning capability analysis, he makes his
observation about normal distributions and proceeds immediately
to chi-squared analysis, hoping that no one will ask questions;
he knows only what he's read and memorized from his book.
He astounds himself with what he can actually remember,
and his confidence soars when no one, including the CEO,
asks questions. So he proceeds to offer an exercise for
the students. It's taken directly from his statistics book
and examines the following data:
1. Cp = 1
2. Cpk = -1
3.
= positive number
4.
= negative number
Endeavoring to demonstrate his interest, one of the participants
asks whether the process is capable. Simsack says, "Of
course it is. If the Cp equals 1, the process is producing
99.73 percent good--that is, within spec limits--parts."
Is Simsack's response true or false?
Simsack's response is false.
If the conditions listed are in place, the distribution
of Xis would be below the lower spec limit. A visual demonstration
of this may be helpful.
A process that is in control, with Xis following a normal
distribution, will have these parameters:
1. LSL = 6
2. USL = 12
3. 
4. 
5. 
6. 
This can be drawn as follows:
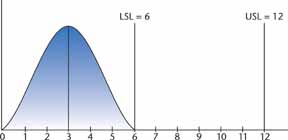
Cp = 1
Cpk = -1


Although Simsack is wrong in this case, he's learned a
great deal about finding someone to blame for his mistakes.
His strategy, therefore, is to insist that he knew the right
answer; the unwitting seminar participant, however, had
asked the wrong question.
Michael J. Cleary, Ph.D., is a professor emeritus at Wright
State University and founder of PQ Systems Inc. He has published
articles on quality management and statistical process control
in a variety of academic and professional journals. His
Web site is www.pqsystems.com. Letters to the editor regarding
this column can be e-mailed to letters@qualitydigest.com.
|