Accreditation Forum Signs Worldwide Recognition Agreement Members of the International Accreditation Forum, a membership group of ISO 9000 accreditation bodies and interested stakeholders, recently signed a historic Multilateral Recognition Agreement in Guangzhou, China. The effort began five years ago, when the group conceived the idea to promote efficiencies and economies in world trade. Signatories to the MLA include accreditation bodies from the United States, Australia-New Zealand, Canada, China, Japan and the European Council for Accreditation. Specific EA member countries signing the MLA include Denmark, Germany, Italy, the Netherlands, Spain, Sweden, Switzerland and the United Kingdom. Joseph R. Dunbeck, the Registrar Accreditation Board's chief executive officer, signed the IAF MLA on behalf of the American National Standards Institute-Registrar Accreditation Board's National Accreditation Program, which represents the United States in the IAF. "A company operating in one country, which feels there's value in getting its organization registered through a registrar accredited by a signatory to this agreement, has a level of comfort that it is a multinational operator," says Dunbeck. "The goal is to assure ourselves that we each are operating in a consistent and comparable way." The MLA represents the culmination of a series of peer evaluations in which the procedures and operating practices of each accreditation body were audited by skilled evaluators from two other peer bodies. Participants were evaluated to the IAF MLA document, which incorporates ISO/IEC Guide 61, the internationally accepted criteria for the operation of accreditation bodies. Now that the initial IAF MLA is in effect, the IAF process will extend to other accreditation bodies as they apply for membership and successfully complete peer evaluations. The IAF is designing its own mark to identify participating registrars. For more information, contact ANSI-RAB at (888) 722-2440.
Baldrige Spotlight: Xerox Business Services
In the late 1980s and early 1990s, Xerox Corp., a pioneer in the document control industry, came under siege. Accustomed to monopolizing a market they essentially had created, Xerox found themselves facing stiff competition from rival businesses in Japan. "Quite frankly, we were in danger of going out of business," recalls Thomas J. Dolan, president of Xerox Business Services. The company began its rebound after adopting total quality management principles, says Dolan. When the Baldrige Award was established in the early 1980s, it was a natural step for the company to apply for the award and put Xerox Corp.'s principles to the test, says Dolan. The company first applied -- and won -- in 1989, for its Business Products and Systems division. At that time, Xerox Business Services was a relatively small division within the company. Now, with about 14,000 employees, Xerox Business Services has found the award a powerful focal point and motivator. "You really apply for the award with the idea that it will help your company become better and stronger," Dolan notes of the Baldrige. "Having said that, though, winning is clearly the ultimate recognition that you've been practicing the principles of quality management." As a result of their first win in 1989, Xerox Corp. began a partnering program with other companies interested in applying for the award. "That's one of the key responsibilities of winning the Baldrige Award," explains Dolan. "We are willing to share it and express to other organizations what it might mean to them." The Baldrige has affected Xerox's ideology, especially regarding customer focus, says Dolan. "Back in 1989 when we applied for it the first time, we were beginning to appreciate just how important customer satisfaction and the customer is," he observes. "Because of its focus on the customer as the center of the process, the Baldrige has helped us keep that customer-first orientation in place and strengthen it." U.S. Coast Guard Unit Registers to ISO 9002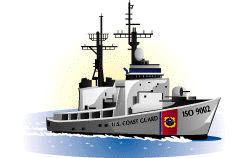 ISO standards have proven popular with the military. The industrial support division of the U.S. Coast Guard Integrated Support Command, located in New Orleans, recently joined the ISO 9000-registered ranks, receiving ISO 9002 certification in December. The industrial division, which employs 40 people, provides services for other Coast Guard units, including electrical repairs, carpentry, offshore structure repairs, underground tank removal/replacement, diesel engine overhaul, and ship fitting and plumbing. It also serves the public through search and rescue, fisheries patrol and law enforcement on the water. "Our customers are the public," maintains Chief Electrician's Mate Tom Cramer, quality manager for the industrial division. "We want to provide the best quality products and services in their best interests." In January 1997, the base reviewed its quality system, comparing it with the Baldrige Award criteria. To begin fulfilling the criteria's requirements, the base commander implemented a management system based on ISO 9000. The project took nine months, beginning last April. Cramer was chosen to spearhead the project, which included educating military and civilian personnel -- as well as himself. He also was involved with writing the unit's ISO 9000 manual and operating procedures. The unit hired a consultant for training and guidance, and saved tax dollars by partnering with a small business to defray consulting costs. Free Guide for Medical Device Manufacturers Current FDA Good Manufacturing Practice requirements stipulate that manufacturers must implement a quality system for medical devices intended for distribution in the United States. The regulation addresses the design, production, distribution and service of medical devices and helps ensure that they are safe and effective for their intended use. Excel Partnership Inc., an international training and consulting firm located in Sandy Hook, Connecticut, offers a free pocket guide of FDA QSR Part 820 of Title 21 of the Code of Federal Regulations for medical devices. The FDA holds all medical device manufacturers responsible for the preamble and interpretation of the QSR. Excel Partnership's guide is designed to be used in conjunction with the interpretation. Single pocket guides are available at no charge. For more information, call Excel Partnership Inc. at (800) 374-3818, ext. 229, or e-mail xlp@xlp.com. Get Your QA Master's Degree on the Web California State University at Dominguez Hills, included in Forbes magazine's top 20 cyber universities, is home to a unique Web site: www.csudh.edu/msqa. The site hosts the school's master's degree program in quality assurance, which offers tracks in manufacturing, service and health care. The program began two years ago when Scott Mackay, director of the university's Center for Training Development, realized the power of e-mail. Many of his program's students had relocated to follow jobs, which made continuing their degree work difficult. Mackay conceptualized a degree program where students could use e-mail as their means of communication -- and transportation. Since then, the program has transitioned to the World Wide Web and has gained accreditation from the Western Association of Schools and Colleges. "We are still the only 100-percent online program," notes Mackay, who also directs the online master's program. He says the program has enjoyed great success, and he anticipates it will continue to grow rapidly. Enrollment has increased 60 percent since the last trimester; students from eight foreign countries and 22 states are represented among the current enrollees. Mackay stresses the need to keep quality not only in the program's curriculum but in the way it's administered. "No matter how advanced technology gets, you can't divorce the human touch from education," he says. To help keep that human touch, Mackay makes himself available via e-mail or telephone to his long-distance pupils. For more information, contact the MSQA's office at telephone (310) 243-3880 or e-mail msqa@csudh.edu. Burton Snowboards Combines Quality and Fun
Burton Snowboards is used to trailblazing. Founded in 1977, the Burlington, Vermont-based company began when snowboarding was still a fledgling sport and has since become a forerunner in its industry. The company's latest venture is ISO 9001 registration. Burton manufactures snowboards, boots, bindings and clothing; the ISO 9001 registration specifically addresses the design and manufacture of snowboards at the Burlington facility, which employs 350 people. The company currently produces 70 models of snowboards from its four manufacturing sites; besides Burlington, it has facilities in Austria and Canada. Burton is known for its relaxed, friendly atmosphere; employees even bring their dogs to work. The reason the company sought ISO 9000 registration had little to do with marketing, notes Lee Bryan, Burton Snowboards' quality manager. The company realizes that most of its customers know little or nothing about ISO 9000. "We did it to add internal structure to a company that was expanding at 30 percent to 40 percent a year," says Bryan. "We've definitely reduced the amount of problems feeding into manufacture on the design process." Staff can perform their jobs better, which has reduced staff turnover and rework, he relates. For more information, e-mail Bryan at 100275.3521@compuserve .com or visit the company's Web site at www.burton.com. Service Jobs Broaden in Scope ompanies are changing their customer service methods and giving greater responsibility to service personnel, according to a recent survey of service, training and quality managers released by Sigma International Inc. For the survey's purposes, service personnel were defined as people who work with customers to answer questions; install, repair or maintain equipment; or provide other assistance. An overwhelming number of respondents report that employees in their call centers, field forces and other departments now function as consultants, clarifying customer needs, attending to a range of customer concerns and providing the best possible solutions to problems. Survey results show a clear shift for service personnel, not only in terms of their importance within their organizations but in the work they do. No longer just responsible for sales, service personnel now contribute to managing the ongoing company/customer relationship, which involves selling additional products and resolving conflicts. This means that service jobs are more challenging and that those who can meet the new responsibilities can command higher salaries. Managers rank satisfying and retaining customers as their top goals, abandoning the ideas of average time spent per customer and total customer calls per day in favor of an increasing focus on customer needs. When asked, "What's most important today?" respondents listed a proactive approach to helping customers as their top priority. Bringing in new revenue ranked at the bottom of the list. More than 100 managers responded to the survey, conducted by Sigma International Inc., the Association for Service Managers International and the National Association of Service Managers. For more information, telephone Sigma International at (703) 934-0300. New Web Site Helps with R&D Alliances The National Institute of Standards and Technology's Advanced Technology Program has launched a new Web site, the ATP Alliance Network, to help companies form research and development alliances. Joint R&D ventures are potentially powerful tools for attacking difficult research tasks because they allow companies to share the costs and risks associated with long-term, high-risk R&D or with entering new markets. The Web site provides visitors with information about the business, managerial, administrative and legal resources required for a successful R&D joint venture. The Alliance Network is a particularly valuable resource for potential research partners who are considering applying for an ATP award. The award program has co-funded more than 100 joint ventures to date. The ATP Alliance Network Web site includes the pros and cons of conducting high-risk R&D in an alliance, proven best practices for ATP joint ventures and data from recent economic studies on the benefits of doing collaborative R&D under the ATP. It also offers a roadmap of the ATP administrative process -- including links to the most important documents required for creating and managing an ATP cooperative agreement -- and links to other resources for R&D alliance managers. Visit the ATP Alliance Network at www.atp.nist.gov/alliance. General information on the NIST Advanced Technology Program, including policy, procedures and projects funded to date, can be found on the ATP Web site at www.atp.nist.gov. |