newsdigest
by Dirk Dusharme
DIRECTORY
Don't Lose Your ISO 9000 Registration
10 Steps to CE Mark Compliance
Jack be Agile; Jack be Quick
The Rework Can Kill You
Apprenticeships Prepare Tomorrow's Work Force
When My Machine Calls Your Machine
Beware of Autonomous Teams
ANSI and RAB Release EMS Accreditation Guidelines
Maintain Positive Employee Attitudes
Don't Lose Your ISO 9000 Registration
Although it's a rare occurrence, companies do sometimes lose their ISO 9000
registration. In the United States, estimates range from a fraction of a
percent of registered companies to a little more than 1 percent, depending
on the registrar surveyed.
Reasons for withdrawal of a company's registration are covered in ISO/IEC
Guide 48, "Guidelines for Third-Party Assessment and Registration of
a Supplier's Quality System." Reasons include:
· Surveillance indicates a serious nonconformance. "If surveillance
indicates a major nonconformance, we sit down with the supplier and agree
on a time period for corrective action," explains Malcolm Appleby of
KPMG Quality Registrar. "If at the end of that time, the client has
not taken the necessary corrective action, we can withdraw the certificate."
· The system rules are changed, and the supplier will not or cannot ensure
conformance to the new requirements.
· The supplier ceases to supply the product, process or service for an extended
time.
· The supplier requests the certificate be withdrawn.
· The registered supplier fails to pay their bills to the registrar. Registrars
unanimously agree that this is a swift and sure way to lose your certificate.
· Continuing to use registration documentation or the registrar's symbol
or logo in an improper manner. For instance, advertising that a product
which falls outside the scope of your company's registration is certified.
Following the withdrawal of a certificate, some registrars may publish your
company's withdrawal notice in an appropriate trade journal. They may also
report the withdrawal to their accrediting agency.
Return to News Digest Directory
A wide variety of products currently require the European Union's CE Mark
in order to be sold in Europe. Ann Been of Abbott Laboratories suggests
the following steps as an outline for seeking CE Mark compliance.
Do your research. Read the actual directive.
Interview consultants, competent bodies/notified bodies and test labs
until you feel comfortable about the directive requirements.
Understand the different routes to compliance for your directive.
Establish a good working relationship with a European competent body or
notified body.
Prioritize the products you are dealing with.
Draft a process flow for the compliance work.
Gather all customer literature and product documentation.
If applicable, review your list and your compliance route with a competent
body.
Do the work.
If extensive product modification is needed, reassess your priority list.
Will the time spent on this product mean not meeting the conformance deadline
on another product?
Source: "European Community Quarterly Review," Third Quarter
1995, Technology International Inc., telephone (804) 560-5334 or fax (804)
560-5342.
Return to News Digest Directory
Jack be Agile;
Jack be Quick
Quality and customer service remain U.S. manufacturers' two most competitive
factors, according to the "Sixth Annual Grant Thornton Survey of American
Manufacturers Report."
Executives are twice as likely to cite as reasons for their success either
high-quality products (38 percent) or superior service (33 percent) over
cost efficiency (17 percent) or rapid product development (12 percent).
However, Grant Thornton's report states that speed and agility will ultimately
become a critical requirement for mid-size manufacturers as their major
customers move toward mass customization. To that end, 78 percent of mid-size
companies are reducing product cycle times by simplifying product design
or reducing the number of component parts.
For more information or a copy of this study, contact Grant Thornton at
(212) 599-0100.
Return to News Digest Directory
The Rework Can Kill You
By the end of 1993, escalating rework costs almost drove Astro Metallurgical
out of business. Fortunately, a holistic quality approach emphasizing employee
awareness has enabled the Wooster, Ohio, company to cut rework hours in
half, saving the company half a million dollars by the end of 1995.
Part of the problem was that employees simply weren't aware of the cost
of their mistakes, explains Richard Edelen, director of quality for the
piping and pressure-vessel fabricator.
"For instance, if a welder made a quarter-inch error out of 300 feet,
to go back and correct that quarter inch was extremely expensive,"
says Edelen. "Making people more aware that what they thought of as
incidental errors were actually very expensive really helped reduce the
rework. That welding station is now more than 99-percent accurate."
Increasing employee awareness includes problem-solving teams and counseling
sessions, where supervisors and employees discuss the results and root causes
of shop-floor mistakes. This helps drive home the importance of identifying
problems before they reach the end of the line.
Last year, Astro started a unique problem-spotting incentive program called
"Waste Watchers." The company gives $10 to any nonsupervisorial
employee who spots an error one process step from its source. Rework immediately
dropped by 50 percent when the program went into place in July 1995 and
has remained at that level for six months, says Edelen.
"From July to December, I handed out about $3,000," he recalls.
"The drop in rework probably paid for itself 10 times over."
Astro plans to reduce rework another 30 percent and customer complaints
by 65 percent in 1996.
Return to News Digest Directory
Apprenticeships Prepare
Tomorrow's Work Force
Apprentices have gained solid experience in a wide range of company operations
while earning a college diploma through a program launched two years ago
by Rochester Institute of Technology and Fisons Pharmaceuticals.
The apprenticeship program involved rotating apprentices through different
jobs in various departments-including quality departments-throughout the
two-year program. Apprentices-full-time workers-attended on-site courses
taught by RIT instructors that related to the business operations they were
immersed in. Courses on quality, for instance, included foundations of quality,
TQM overview, basic statistical quality control, costing for quality and
leadership for quality.
"This is a new concept of apprenticeship," says Lynda Rummel,
associate dean of RIT's College of Continuing Education. "It's more
like the European model, which is a highly sophisticated integration of
work experience and in-depth education, but with an American character."
The benefits for students are numerous, notes Rummel. They receive extensive
on-the-job training, the company pays their tuition expenses, and unlike
traditional internships or co-ops that last only three to six months and
focus on one job, the apprenticeship program gives students a broad base
of experience over an extended period.
Return to News Digest Directory
When My Machine Calls Your Machine
Have you ever been run in circles by automated attendants? Does it seem
like the voice on the voice mail isn't interested in your business? Ever
wonder how customers perceive your company because of your voice mail? Follow
these tips from Nancy Friedman, the " Telephone Doctor."
Your voice-mail system
· When recording a message, identify yourself and your
department.
· Smile and use your personality when you record-callers can hear the difference.
· Practice your recording. Record until you sound natural and conversational.
· Avoid the obvious. Instead of, "I can't come to the phone right now,"
say "I'm in a sales meeting until 3:00 p.m. I'll return your call as
soon as I can."
· Update your voice-mail greeting frequently.
· Give your callers an out-the option to talk to an actual human being.
· Always return calls.
Their voice-mail system
· Be prepared to leave a clear, concise message. Write it down, if that
helps.
· Smile when you leave a message. It'll brighten the message and make it
stand out from the rest, increasing the chances of a return call.
· Unless it's an emergency, avoid leaving bad news.
Return to News Digest Directory
Beware of
Autonomous Teams
Participatory management, which attempts to increase the involvement of
lower-level employees in corporate decision making, has failed to break
down the walls of bureaucracy, according to Charles Heckscher, chair of
Labor Studies and Employment Relations Department at Rutgers University.
"I am an enthusiast of participation when it is done right," says
Heckscher, who interviewed more than 250 managers in 14 large organizations.
"But, when empowerment means autonomy, it actually has a negative effect."
The problem, explains Heckscher, is that restructuring, delayering and downsizing
have led companies to give more control to autonomous teams rather than
increasing the interactivity between those teams. This, in turn, has eroded
the informal communication channels that exist within a standard bureaucracy.
This results in teams that work well but, because of "turf-building,"
have trouble communicating outside the team.
As a means to fight the turf-building tendency, Heckscher suggests temporary
decision-making structures or problem-solving teams. These teams allow employees
to work on problems outside their normal sphere of influence and helps prevent
them from growing roots in their own turf.
"You have to think of empowerment not as increasing your autonomy but
as increasing your influence," Heckscher points out.
Heckscher also maintains that successful companies focus their employees
on the company's purpose-what the company is trying to accomplish in the
next three to five years.
"The sense of purpose is what really unites people," says Heckscher.
"It's the glue that allows flexible participation."
Return to News Digest Directory
ANSI and RAB Release EMS Accreditation Guidelines
The race is still on for who will become the U.S. accreditation agency for
ISO 14000 registrars. Although both the Registrar Accreditation Board and
the American National Standards Institute will provide accreditation for
U.S. registrars, the question still remains as to which organization will
represent the United States internationally-only one accrediting organization
from each country gets that honor.
Recently, both the RAB and ANSI announced their plans to release guidelines
and criteria for the accreditation of ISO 14000 registrars. The RAB has
completed a draft of its criteria for accreditation of ISO 14000 registrars.
The draft has been available since the end of February.
"This draft document describes how a registrar must organize and operate
in order to achieve EMS accreditation by RAB," explains Joseph Dunbeck,
RAB's CEO. "We encourage all interested stakeholders to review the
criteria and respond to RAB with any comments. It is this public review
and comment process that will provide robust criteria for EMS registrars."
ANSI-which recently established a council to oversee the formation and activities
of its national program to accredit registrars, auditor certifiers and training-course
providers-also promises that its ISO 14000 accreditation program will reflect
the desires of all stakeholders.
"The council is committed to customer satisfaction," says Gerald
Ritterbusch, an ANSI board member and chair of the EMS Council. "We
will ensure that ANSI's EMS National Accreditation Program is credible,
provides a high level of confidence to stakeholders and, most important,
provides value all across the board."
For additional information, contact the RAB at (800) 248-1946, fax (414)
765-8661; contact ANSI at (202) 639-4193.
Return to News Digest Directory
Maintain Positive
Employee Attitudes
Downsizing is a stressful time for employees. But it is possible to avoid
some of the pitfalls of downsizing, according to researchers from National
Computer Systems.
The first step is to communicate, says NCS. Often during downsizing, the
rumor that develops during the preliminary planning stages results in employees
spending significant amounts of time gossiping and worrying about what is
happening. At the same time, managers "in the know" are guided
by a policy that discourages talking about rumors with employees. The associated
costs, in terms of lost productivity and employee loyalty, may be significant.
Communication will help curb the worry and redirect employee energies. The
company should admit that a downsizing will occur, the purpose of the downsizing
and that employees who are let go will receive appropriate severance pay.
Second, make valuable employees feel they are part of a progressive organization.
Discuss the downsizing as a step toward a more efficient and profitable
business with an attractive future. Too often, during the downsizing process,
employees wonder whether to stay or leave, say researchers, especially those
with valuable skills and training who may have outside offers. Also, when
employees see top managers leave voluntarily, they may question the company's
long-term viability and opt to leave immediately.
Last, long after downsizing is completed, you must continue communicating
with employees in order to rebuild trust. Management must not assume that
remaining employees are merely grateful to still have jobs. Employees need
to feel they are valued, that they have a place in the company and that
management believes that they are an important part of the organization's
success. To emphasize the point, talk about where the company is headed
and describe any plans for growth and prosperity.
Source: NCS Research Notes, National Computer Systems
Return to News Digest Directory
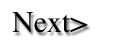