by Barry Rogers
Companies competing in today's global market must continually cut manufacturing costs to survive. Ask any production engineer where bottlenecks occur, and he or she will most likely point to the coordinate measuring machine or inspection departments. To remain globally competitive, manufacturers must find ways to cut inspection and nonvalue-added quality costs.
How can you reduce the cost of quality when more rigorous part inspection becomes increasingly essential, and as industries comply with standards requirements and adopt Six Sigma disciplines? The problem comes when parts must be produced to ever-tighter tolerances, then validated and documented before shipping. Rather than sampling parts to a set schedule, producers now seek to verify each critical feature on every part.
Squeezed between just-in-time delivery schedules and pressures to cut work in process, manufacturing planners look for inspection technologies that can keep pace with manufacturing flow while providing prompt feedback for process control.
At the same time, manufacturers are working with industry groups and standards organizations on open metrology technologies that allow interoperability between different makes and kinds of CMMs and other inspection equipment, while making plug-and-play upgrades possible to avoid huge capital investments in replacing obsolete metrology equipment.
The metrology industry is responding with advances in automated part inspection technology, particularly in CMM probing capabilities that enable programmable part checking with high levels of throughput, accuracy and repeatability.
New sensor and motion control developments are closing the gap between speed and accuracy in part inspection and qualification. Until recently, CMM inspection methodologies were essentially either/or propositions involving distinct tradeoffs:
Vision scanning probes for higher speeds with lower accuracies
Contact probing at slower speeds for higher accuracies
This is now changing. Innovations in CMM controls and probe design are overcoming factors that previously limited scanning speeds for contact probing. This can greatly shorten part inspection routines, especially on large and complex parts involving thousands of inspection points.
Part features and accuracy specifications will always be the primary factors in determining the probing methodology to use. No matter how strong the push for faster throughput, speed must be a secondary consideration to accuracy.
Touch-trigger probes and contact-scanning probes both involve physical contact with the part surface to provide dimensional measurement with high levels of precision. They are capable of accuracies of up to 0.00004 in., compared to 0.001 in. for many optical-scanning probes.
Touch-trigger probes take their measurements by intermittent single-point touches. Scanning probes maintain continuous moving contact with the part surface to capture 2-D and 3-D data. With the proper strategic use of both kinds of probes, manufacturers have been able to automate qualification of various parts and features to high accuracy levels.
Touch-trigger probes have been ideal for discrete point measurement. They are best suited to checking part features where clearance, location or a single particular dimension is critical. A wide selection of probe configurations and motorized probe heads provides optimal part access and approach angles.
Discrete point measurement is done at a constant velocity with zero acceleration during the point of contact. The touch displaces the probe's stylus tip, generating a trigger signal. This intermittent go-touch-retract motion and need for constant velocity at touch mean that the fastest touch-trigger probes register about 12 measurements per second. In practice, however, a much slower rate is normal. Single, point-at-a-time measurement makes touch-trigger probing inefficient for most form inspection, where hundreds of measurement points might be required to fully define and qualify a part feature for close-tolerance form or fit.
Contact scanning provides the faster data acquisition needed for form measurement. A rapidly scanning, continuous measurement process records many data points to measure and control a form. Scanning probes are particularly suited to determining functional fits--e.g., cylinders, bores, valve seats and gears--where variation can affect product fit, function and reliability.
Although modern CMMs are capable of moving at high speeds--i.e., several hundred mm/sec--scanning methods have traditionally been restricted to slower measuring speeds to minimize deflection of the machine's structure caused by acceleration and deceleration during the measurement process. Unlike touch-trigger probing, where the probe moves along a single vector at constant velocity, scanning takes measurements at continuously changing velocity vectors.
The figure to the right shows the effect of dynamic forces as scanning speeds rise, causing form error to increase. The blue plot shows low-speed readings (10 mm/sec or 0.4 in./sec), which provide an accurate assessment of feature size and form. The red plot of uncorrected high-speed readings (150 mm/sec or 6 in./sec) shows that the measured size of the bore decreases as dynamic forces take effect, causing deflections on the CMM.
To obtain acceptable accuracy on tight tolerance parts, the standard practice in CMM scanning is to take measurements at less than 10 mm/sec (0.4 in./sec), but often that's just not fast enough to give real-time feedback to the production floor.
All that has changed with a recent announcement from Renishaw regarding its long-anticipated Renscan5 and REVO head and probe systems. (See sidebar below.) The new technology allows high-accuracy, high-speed (up to 500 mm/sec) scanning with up to 400 mm probes.
Renscan5 provides far greater capabilities than the company's existing dynamic compensation technology. That product, RenscanDC, enables CMM users to measure at extremely high speeds, but with accuracies that previously could only be achieved at low speeds. RenscanDC is based on error-mapping the dynamic errors when measuring component features. These dynamic errors are normally repeatable. Scanning a feature first at low speed and then at high speed allows dynamic errors to be determined and a dynamic compensation map to be computed. Only one sample component from a production line needs to be scanned at the slow speed to generate the dynamic error map.
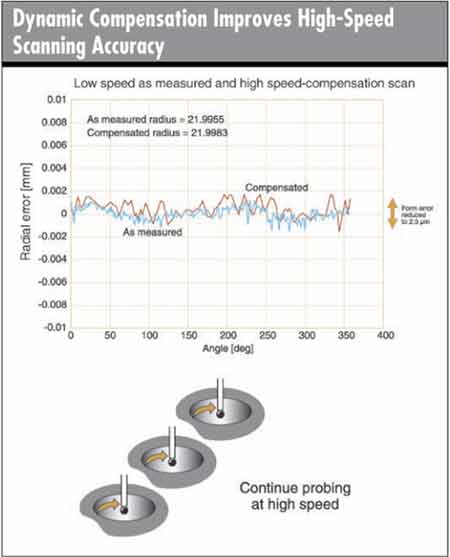
The correction data are saved and automatically applied to subsequent parts and batches, which can now be measured solely at the fast speed. The figure above shows the improvement in high-speed scanning accuracy by applying the compensation. RenscanDC is part of an optional scanning plug-in for Renishaw's universal CMM controller (UCC).
High-speed scanning provides a variety of advantages in meeting the objectives of lean manufacturing:
Faster part checking--many times faster, sometimes by a factor of 10 or more--for quicker feedback to the process to reduce rejects and/or rework. This can be especially effective on parts such as engine blocks or cylinder heads where, at present, a sizeable number of valuable units can be machined before inspection results are available to report unacceptable process shifts.
Significant cost and space savings by reducing the number of CMMs required to inspect and process output from machining lines
Greatly increased inspection throughput, especially on complex geometry parts, such as engine blocks with many critical features to be measured. Higher throughput makes it easier to synchronize and integrate inspection with manufacturing flow.
As an example of the gains in throughput that are possible with high-speed scanning, comparative measurement tests were conducted on two cylinder bores (each measured at six sections) and crankshaft bores with a single scan in each journal (see figure below). The measurements were first made at 5 mm/sec, a typical scanning speed. The measurements were then repeated with RenscanDC applied at a scanning speed of 100 mm/sec.
Inspection time at slow speed: 27 minutes, 27 seconds
Inspection time at fast speed: 4 minutes, 34 seconds
Reduction in inspection time: 83 percent

Scanning at high speed requires not only the latest in controller technology but new sensor designs as well. Today's sensors must be capable of quickly and accurately capturing large amounts of streaming data. Although the controller might move the machine at 100-200 mm/sec, new probes must be capable of capturing repeatable data at more than 1,000 data points a second.
Renishaw offers two different probe systems--the SP25 and the SP80--engineered specifically for both high-speed scanning and general-purpose versatility. Each probe is capable of scanning well in excess of 100 mm/sec while using a stylus up to 400 mm in length. Working in combination with the UCC, both probes capture data at 1,000 data points a second.
A compact, low-mass probe design means low inertia for rapid dynamic response to contour changes while keeping the stylus in contact with the surface at higher scanning speeds.
All of the added functionality and throughput afforded by new CMM technology is worth nothing unless it can be easily adapted across multiple brands of CMMs and software. This lack of interoperability has long been an issue for companies with multiple brands of CMMs. I++ DME is a key element in evolving global industry standards designed to ensure the interoperability of metrology systems. It provides an open protocol that gives cross-platform controller compatibility with all measurement software packages. Major users in the automotive industry, through the global Automotive Industry Action Group, have pushed for interoperability in manufacturing and metrology systems, but the new developments will benefit all industries using CMMs.
The I++DME protocols give CMM users flexibility in use, and choice of software and CMMs, along with fast access to breakthroughs in measurement technologies. This offers major benefits for plants with more than one make of CMM.
A demonstration by AIAG and the National Institute of Standards and Technology at Quality Expo 2005 showed how three different brands of CMMs using three different brands of software could seamlessly communicate with each other to control and collect data. AIAG called the demonstration "a world first" in "using standard, plug-and-play interfaces" to make it possible for "disparate systems to interoperate while maintaining 100-percent data integrity." The demonstration showed how metrology interoperability provides "the potential to save industries millions of dollars worldwide through the seamless exchange of measurement information," according to AIAG.
High-speed scanning is here to stay as manufacturers look for solutions that can significantly reduce operating costs and time to market. Technology advances are making contact scanning a viable solution to high-throughput and high-accuracy automated part inspection. Effective applications require a powerful, reactive CMM controller; open systems interoperability; automated probe and stylus change; and probe designs optimized for application versatility and high-speed, dynamic forces. These technologies are becoming available today for progressive CMM users and builders.
More sensor and motion-control advances are on the way that promise to revolutionize CMM measurement performance with ultra high-speed, five-axis scanning capability, collecting data at up to 5,000 points per second. Faster part inspection can raise shop throughput, overall equipment efficiency and velocity to market. New interoperability standards will ensure that these technologies are cross-platform. All these are vital elements that will keep U.S. manufacturers globally competitive. For most manufacturers, high-speed inspection can't happen fast enough.
Renishaw just announced a new head and probe technology, Renscan5, that will improve scanning speeds by a factor of 10. The five-axis scanning technologies, about seven years in development, enable measurement at speeds of up to 500 mm/sec and essentially eliminate the measurement errors normally associated with existing three-axis scanning systems. The Renscan5 concept uses the measuring head to perform most of the motion during inspection routines, minimizing the dynamic errors caused when moving the larger mass of a CMM structure.
The first product to take advantage of the new technology is REVO, a two-axis head that uses synchronized motion when scanning to quickly follow changes in part geometry without introducing its own dynamic errors. This allows the CMM to move at a constant velocity along a constant vector as measurements are being taken, removing the inertial errors that result from acceleration of the machine during conventional three-axis scanning.
The two axes are driven by state-of-the-art, brushless motors linked to 0.08 arc-second, high-resolution encoders, giving fast, ultra high-positioning accuracy. The infinite rotation and infinite positioning capability of the head means better access to features and the ability to take the shortest positioning path.
A new probe further minimizes the errors caused by the dynamic effects of high-speed motion and allows the use of long styli (up to 400 mm) without reducing accuracy. A laser is used to accurately measure the exact position of the probe tip, with a beam of light directed from within the probe body down a hollow stylus to a reflector at the stylus tip, as seen in the figure at the bottom.
The hollow stylus is designed to bend, thereby deflecting the return path of the laser beam which is received by a position-sensing detector (PSD), also mounted in the probe body. Movement of the laser spot on the PSD is translated into a measurement output by combining it with information about the geometry of the measuring head and probe, and each of the CMM-axis scale outputs. The exact stylus tip position can therefore be calculated. This process takes place while the stylus tip is dynamically scanning the part and the measuring head moves synchronously with the CMM. With minimal inertial effects on the laser beam, measurement accuracy is maintained even with very long styli.
Renishaw showed off the Renscan5's capabilities at a recent press conference. The demo first performed a typical scan of an 80-mm cylinder bore using a standard Renishaw SP25M probe at 10 mm/sec. In such a scan, the CMM provides movement in all three axes in order to keep the probe in contact with the cylinder. CMM movement is necessarily slow to avoid inertial error. The total scan took about 90 seconds. Next, the same scan was performed at 100 mm/sec using RenscanDC; this scan took about 12 seconds. Finally, the cylinder was scanned with the REVO head in place. The CMM moved in one vector only, at a constant velocity along the center axis of the cylinder while the REVO head spun, as seen in the figure above. The result was a helical scan of the bore that took no more than 2.5 seconds. Each method scanned the feature using the same number of revolutions.
.jpg)
|
Barry Rogers started his career in tool and die making with Honeywell and John Deere, then moved into the metrology field with LK Tool USA, a manufacturer of coordinate measuring machines, rising to general manager of the LK-Cincinnati Milacron Tech Center in Detroit. In 1988 he joined Renishaw, global leader in inspection probe and machine calibration technologies, where he is presently national sales and marketing manager.
|