America's Best Plants
by Theodore B. Kinni
In 1990, IndustryWeek magazine recognized 12 facilities exhibiting
world-class manufacturing practices as the first "America's Best Plants."
Each year since, IW's editors have chosen 10 additional facilities to join
their ranks. In America's Best: IndustryWeek's Guide to World-Class
Manufacturing Plants (1996, John Wiley & Sons Inc.), author Theodore
B. Kinni reveals the collective lessons of the America's Best Plants winners.
The criteria are organized into three core strategies-customer focus, quality
and agility; and six supporting competencies-employee involvement, supply
management, technology, product development, environmental responsibility
and safety, and corporate citizenship. This excerpt focuses on the core
strategy of quality.
Nowhere did the quality revolution of the late 1970s and 1980s have a greater
impact than on manufacturing companies. In the United States, entire industries
disappeared as consumers discovered and embraced defect-free, long-lasting
imported products that were priced significantly below the products they
had previously been offered.
Many industries, and many of America's blue chip companies, came under intense
profit and market-share pressure during this period. Xerox Corp., for example,
found itself in the unenviable position of trying to figure out how to compete
against Japanese companies that were somehow able to sell their copiers
at prices below Xerox's manufacturing cost. How was this possible, asked
bewildered managers? There were a variety of reasons, but one of the most
important was encompassed in the word "quality."
Quality, which was thought of by many American companies as simply an inspection
function, had been completely redefined while they weren't watching. Their
competitors were building quality into the structure and the culture of
their companies and eliminating waste, returns and nonvalue-added activities
from their production processes. More importantly, they weren't adding to
the cost of products by adding quality. They were actually lowering their
production costs at the same time.
It is difficult to overstate the extent of the corporate consciousness-raising
that occurred when American companies belatedly discovered this new competitive
weapon called quality. For close to a decade, the concept spread like a
wildfire through every aspect of manufacturing. Quality became the byword
in industry, and, as the concept expanded into every operating arena, it
often seemed the sole objective of plants. The 72 manufacturing plants that
have won IndustryWeek's annual America's Best Plants awards since 1990 are
no exception, and, although quality is no longer the sole concern of these
manufacturers (the stakes on this gaming table are always rising), it is
still an integral part of their operations. Quality is a core strategy of
Best Plants.
Establishing a quality mind-set
The main objective of the core strategy of quality is to consistently provide
the best possible product at its price point in the marketplace. The means
by which this is accomplished are far-reaching. But first, quality must
become a basic component of the structure and the culture of a plant. This
is a primary lesson of Best Plants: Quality is not a program that can be
simply imposed on an operation; instead, it is a way of operating that permeates
a business and the thinking of its employees.
Best Plants start creating a quality process by including quality in their
corporate intent statements. These quality-based values become the basis
for its place in the strategic hierarchy of the plant. For instance, Unisys
Government Systems' 1993 award-winning Pueblo, Colorado, plant enumerates
seven values that serve as "the basis of operations for managers, employees
and teams":
Quality is the responsibility of every employee
and team.
Quality improvements result from management
leadership.
Quality should be viewed from the customer's
perspective.
The focus of quality improvement must be on
each job, at each step in the process.
No level of defect is acceptable.
There must be a commitment to continuous improvement
and the seven-step process to continuous improvement.
Quality improvement reduces costs.
These quality values are brought to life in the plant's total quality process
plan, which was introduced in 1990 and is shepherded by senior executives.
TQP is deployed through a three-level structure and is guided by a quality
steering committee.
"The TQP staff council champions TQP culture and ensures the TQP process
is compatible with our business strategy and plan," explains internal
quality consultant Rudolph Krasovec. "The council includes our senior
executives and members of the Benchmarking Partnership Team, who are selected
from staff organizations. The next level includes the BPT, whose charter
is to coordinate all our benchmarking activity, our TQP Staff Facilitation
Team and the people who work on applications for quality awards. This level
leads our TQP initiatives and focuses on the cultural aspects of ensuring
that TQP is our standard operating procedure. The third level comprises
our TQP process operations and program teams."
Engelhard Corp.'s 1991 award-winning plant in Huntsville, Alabama, depends
on its quality council to lead the establishment of a plantwide quality
mind-set. The council defines the plant's quality mission and guiding principles.
It uses a quality operating system to translate quality goals into operational
objectives.
QOS defines three areas of quality for the plant: customer focus, internal
focus and preventive focus. By developing monthly performance measures in
each of these areas, the plant is able to target quality improvement opportunities
and continuously raise quality levels. In customer focus, for instance,
customer rejects and returns are logged by part number and the reason for
return, and are summarized in Pareto and bar charts for analysis. QOS's
internal focus measures in-process parameters, first-run capability and
costs of quality (such as internal and external failure costs) as percentages
of the plant's total product costs. The prevention focus utilizes customer
quality ratings, supplier ratings and advanced quality planning methods
such as FMEA control plans and design of experiments to identify and address
quality concerns before they result in product defects.
Making quality everyone's job
When quality is built into the culture and structure of a plant, it becomes
everyone's concern. Quality in Best Plants is no longer the sole responsibility
of the quality assurance or quality control departments, which, historically,
have tended to be reactive and inspection-based jobs, not proactive functions.
In fact, Best Plants often believe it is a waste of resources to try to
inspect-in quality. They prefer to build quality into process and products.
The realization that inspecting-in quality is ineffective compared with
building-in quality is why many of the Best Plants have reduced or eliminated
their dependence on traditional quality functions. Instead, the responsibility
for quality has been spread over the entire work force. Quality is a part
of the job description of every employee in a Best Plant.
Among other things, this translates into quality at the source. "At
the source" means that the responsibility and accountability for quality
resides with the people who are actually producing the goods and services.
For example, Edy's Grand Ice Cream plant in Fort Wayne, Indiana, which began
operating in 1986, has never had a laboratory or quality control staff.
Instead, all quality checks are performed by the machine operators. Operators
have full control over their output, which includes withholding product
of suspect quality or stopping the production lines at any time.
Quality at the source means more than ferreting out defective products.
It also means identifying and eliminating the causes of those defects. Integrating
quality into the daily responsibilities of production workers meshes smoothly
with the overall Best Plants movement toward employee involvement and team-based
structures at this plant. Once defects are identified, the effort and creativity
of the entire work force can be brought to bear on resolving quality problems.
Automotive parts supplier Nippon-denso Manufacturing, for example, requires
all operating employees to inspect their own work. When a problem is discovered,
the plant's quality circles are used to determine its cause. Thus, the problem
resolution process "results in improved operator skills, better teamwork,
reduced customer complaints and an improved training-and-operations manual,"
according to the company. All the plant's employees take part in quality
control circles. The results of their work are presented during a biannual
competition that is judged by the company president and a panel of executive
staff members.
Quality at the source requires a significant investment in time and employee
training. Johnson & Johnson's Sherman, Texas, plant spent eight years
fully implementing the concept. It is neither realistic nor responsible
to ask employees to take control of the quality of their work without also
giving them the training, the tools and the responsibility they need to
successfully undertake the challenge. For example, Chesebrough-Ponds' 1992
award-winning Jefferson City, Missouri, plant trains all production employees
in decision-making, problem-solving and quality tools before giving them
the responsibility of monitoring and improving the quality of the plant's
manufacturing processes.
Building quality into processes
The next lesson embraced by Best Plants is that product quality is highly
dependent on the consistency of a plant's processes. It was the late W.
Edwards Deming who brought this idea into the mainstream of manufacturing
thought. He taught that the largest cause of defective products was poorly
designed processes and that no matter how much pressure was brought to bear
on the work force, products could not be consistently and/or significantly
improved without addressing the systemic causes of their defects.
Whether they directly credit the famous consultant or not, Best Plants are
Deming disciples. They understand that defect-free products result from
tightly controlled processes. Best Plants map, measure and continuously
improve their processes. This process orientation is also intimately connected
to the Best Plants' predisposition to practice quality at the source. Front-line
production employees are responsible for much of the Best Plants' success
with process control and improvement.
As Deming taught, a comprehensive understanding of process is the primary
weapon in the war to eliminate the process variations that cause product
defects. This is a lesson well understood by Rockwell International's El
Paso, Texas, plant. Although it is primarily a short-run production facility,
El Paso's 20-odd products all flow through a series of common processes
before being distributed to product-specific areas for final assembly. In
an effort to completely understand its processes, the El Paso plant maps
all of its core manufacturing and support processes using tree diagrams
and flowcharts. The charts and diagrams are then posted in team areas.
After process maps are complete, El Paso uses statistical process control
techniques to measure its processes. For each process, variables and attributes
data is collected. Variables data is converted to Cpk measures. The plant's
attributes data is measured in defects per million opportunities. All of
this process data provides the raw material for the plant's continuous improvement
efforts. The results: In 1995, El Paso reported Cpk measures above 2.0 on
85 percent of its processes. (A Cpk of 2.0 is roughly equivalent to a six-sigma
quality level.) From 1990 to 1995, the plant reduced its defect rate from
1,200 DPMO to less than 50 DPMO, a 96-percent improvement.
Although SPC may provide a gold mine of information for quality-improvement
hungry manufacturers, its usefulness can be overstated. Westinghouse Electric's
Cleveland, Ohio, plant uses computerized and manual SPC extensively, but
when it comes to short production runs, Operations Manager David Shih cautions,
"It is a tedious, time-consuming process to plot control charts manually,
which provides little real benefit for either quality-improvement or troubleshooting
needs, especially for short-run production quantities, where production
is frequently over before process control charts can be produced."
Furthermore, installing an SPC-based system doesn't actually solve a plant's
quality problems, it merely identifies them. Once processes are charted,
limits established and variations recorded, Best Plants must eliminate the
causes of process variance using other quality tools and techniques. Poka-yoke,
also called fail-safing or mistake-proofing, is one commonly practiced technique
that Best Plants utilize to build quality into their processes.
Baxter Healthcare's North Cove, North Carolina, IV operation effectively
utilized a poka-yoke solution in the plant's sterilization process. In one
of the final production tasks before shipment, a series of racks holding
innumerable full IV bags are wheeled into a large sterilizer. Any error
in the sterilization process results in a loss of all the product. Even
more serious would be a mix-up of sterilized and unsterilized product. To
eliminate that possibility, the plant's staff designed gates for the area
that allow product to move only in the proper direction.
Building process quality
Building quality into processes further requires that Best Plants build
process quality. This may sound like hair-splitting on the surface, but
every piece of machinery and equipment that comprises a process must run
as intended to reach high quality levels on a consistent basis. Equipment
wear and failure are also major causes of defective products.
Best Plants keep their equipment operating in perfect condition using a
series of techniques that are grouped under the generic heading of total
productive maintenance. TPM is really an entire family of maintenance tasks,
including predictive maintenance, preventive maintenance, equipment improvements
and even maintenance prevention-a strategy that attempts to eliminate the
ongoing need for maintenance altogether. All these related techniques support
a single goal: process quality.
SPX Corp.'s Power Team takes a team approach to its TPM program. Each TPM
team is made up of the machinist who operates the equipment, the area supervisor,
the scheduler and a member of the plant's maintenance staff. The team members
work together to schedule all preventive maintenance, and, in the case of
breakdowns, every team member is involved in their resolution. The machinist
is responsible for routine maintenance chores and also takes a front-line
role in the early identification of maintenance problems.
The plant's more sophisticated computer numerical controls equipment is
serviced using laser alignment equipment and a personal computer. "This
allows us to not only tweak the machines, but also gives us an early warning
for things like ball screw and spindle bearing replacement," explains
Plant Manager Jim Schultz.
Power Team uses a "home-grown" computer program to track and schedule
its preventive maintenance tasks. Active for more than a decade, the program
creates a weekly schedule of equipment maintenance. The program also keeps
a history of parts used in the maintenance and repair of each machine and
the hours spent working on it for the previous 12-month period.
Continental General Tire's Mount Vernon, Illinois, plant reports that nearly
three-quarters of its work orders are now planned maintenance, and machine
uptime runs steadily at 99 percent or higher rates. This plant also established
a computer network to log and store its database on machine performance.
It offers an excellent piece of advice for plants working on process quality:
"Make maintenance proactive-not reactive."
Approaching zero defects
Even taking into account the waning of the quality mania of the 1980s, the
pursuit of quality remains a serious business at the Best Plants. Once-acceptable
product defect levels seem ridiculously high by today's standards. In fact,
modern quality goals require new standards of measure. Six-sigma quality,
which translates into a defect rate of 3.4 parts per million and was originally
established by Motorola Inc. as an internal stretch goal, is the de facto
standard at many of the Best Plants. Nippondenso, for example, reported
a customer claim rate of a mere 1.2 ppm in 1991. Other plants have also
recorded defect-free production for long periods of time. In their 1995
Best Plants application, General Motors' Grand Rapids, Michigan, valve lifter
plant reported 18 months of shipments to a major customer without a single
defect. The plant concluded 1994 with a defective parts per million rate
of 2. Two of four production teams worked at a level of less than 1 ppm.
This is a level of performance that represents a 91-percent reduction from
1992 defect levels and, needless to say, the plant exceeded its customers'
supplier goals in every instance.
John Crane Belfab's "No Use As Is" nicely illustrates the Best
Plants' quest for perfection. Explains Quality Manager John Michaelos: "In
1990, we implemented a program of No Use As Is. The Use As Is disposition
is frequently used in industry to accept product that does not meet specification.
This was a major step in our quality management program that did not come
without pain. Use As Is requires our president's approval, and he won't!"
This article is excerpted from Chapter 3 of America's Best: IndustryWeek's
Guide to World-Class Manufacturing Plants ($27.95, 1996) and is reprinted
with the permission of Theodore B. Kinni and publisher John Wiley &
Sons Inc. The book is available through bookstores nationally and from The
Business Reader at (757) 258-4746.
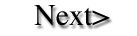