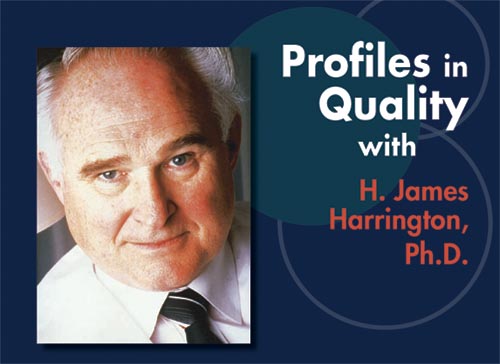
by Carey Wilson
H.James Harrington, Ph.D., is a world leader in business performance improvement. He is the chief executive officer for the Harrington Institute and Harrington Middle East. He also serves as a quality advisor to China and the U.S. government.
Harrington served for 10 years as an A-level member of ISO TC 176 (the technical committee responsible for the ISO 9000 series of standards) and ISO TC 207 (the technical committee responsible for writing the ISO 14000 environmental standards). The New York Times referred to him as having “a knack for synthesis and an open mind for packaging his knowledge and experience in new ways--characteristics that… matter more… for new economy success than technical wizardry….”
Harrington was awarded the Simon Collier Quality Award by the Los Angeles Section of the American Society for Quality (ASQ) in 2007, and his contributions to quality around the world have brought him many such honors. He was appointed the honorary advisor to the China Quality Control Association, and was elected to the Singapore Hall of Fame in 1990. He has been named lifetime honorary president of the Asia-Pacific Quality Control Organization and honorary director of the Association Chilean de Control de Calidad.
He is currently working on a set of 20 books that will include CD ROMs. The series , Harrington’s Performance Improvement Series, covers subjects such as creativity tools, process redesign, process reengineering, reliability, design of experiments, poor-quality cost, measuring executive performance, a balanced scorecard, and simulation modeling. The first four books in the series, released in 1998, are : The Creativity Tool Kit: Provoking Creativity in Individuals and Organizations, Statistical Analysis Simplified: The Easy-to-Understand Guide to SPC Data Analysis, Area Activity Analysis, and Reliability Simplified: Going Beyond Quality to Keep Customers for Life.
Here, he talks about the role of quality in his life, and where it may be headed as the international web of supply and demand adapts to modern concepts of quality assurance.
Quality Digest: You started at IBM as an apprentice toolmaker at age 18 and rose to the level of senior engineer and project manager in quality assurance. In your 40 years of working with IBM, what were the greatest changes in the management of quality assurance issues?
James Harrington: Quality at IBM, when I started with them in 1947 as a full-time employee, was statistically focused on control charts and acceptance inspection. Inspectors roamed the line, doing first-piece and last-piece inspection plus grabbing samples throughout the production run and plotting control charts. Quality was in control of the line. The inspector had total power. Each operator could stop the line if they had a problem. Production control would shake every time the quality manager walked into their area, because it usually meant that the line was about to be shut down.
Over the next 40 years quality became everyone’s job. The quality function became much smaller and less powerful. The quality function’s responsibilities widened to cover many of the support areas. The manufacturing and support people were trained to solve problems and to control the quality of their own work. The focus on suppliers and reliability was greatly expanded in the quality area. As more and more people became accountable for their own quality, no function was responsible. The nice thing about a team is that you always have someone else to blame.
The quality of our products is much better today. Process designs are much better, making it easier to produce better quality. Everyone has been trained on what quality is and how they impact the quality system. We understand our customers much better than we did, although in most cases we do not work as close to them as we did. Personal relationships turned into business relationships.
QD: Did your career path from apprentice to project manager at IBM affect your outlook on how to design and achieve the goals of quality-improvement programs?
JH: I worked as an assembly operator, in the tool room, in a development department as an electrical engineer, in the industrial engineering department, in the component-analysis area, in reliability, and in personnel before I started in quality. This background was the key that helped me understand the full importance of cross-functional processes and that drove the development of our redesigning efforts to improve our support processes as well as our manufacturing processes.
QD: You obviously continued your education as you advanced in your career. What course of study or itinerary of courses would you recommend for students who are considering entering the quality-assurance field? And for people already engaged in quality assurance, what sort of continuing education would you recommend?
JH: How much education is enough? I first started working part-time at IBM on my twelfth birthday, setting pins in their bowling alleys. Then I started to work full time with IBM at the age of 18. IBM’s motto was “THINK”--we were all expected to continuously go to school on our own time. IBM’s schools provided us with tools to do engineering assignments. Local universities gave us the other parts of the degrees that we needed. I stopped going to school when I was 55 years old, but I am still studying, reading, resourcing, and learning.
What does a quality professional need to study? Everything. They need to know everything: How to modify behaviors. How to change top management’s leadership styles. How finance works. How marketing quality is measured. How effectiveness in development engineering is measured. I am 78 years old now, and I just realized how much more I want to know. As a quality professional, don’t limit yourself to studying quality--study business. This is the only way to have quality penetrate throughout the total organization. The best training that any CEO could have would be to be promoted to CEO after being the functional manager of quality assurance.
QD: You’ve written many books and hundreds of technical reports and articles dealing with quality and process improvement. Along with your own vast body of work on the topic, which other books and authors have you found most valuable in gaining the insights that have influenced your career?
JH: W. Grant Ireson’s book on quality that he wrote in the 1950s was what I learned quality from. Then, Val Feigenbaum’s book, Total Quality Control , filled in the remainder of the picture. There has been little new added to the technology since the 1980s and these two books still stand me in good stead.
QD: As a member of the technical committees that wrote the ISO 9000 quality standard and the ISO 14000 environmental standard, how do you view the connection between manufacturing affordable quality products and maintaining environmental quality?
JH: Quality, ISO 9001, is driven by our customers. Environment, ISO 14001, is driven by our conscience. It is always easier to do what we have to do--quality; it is much harder to do what is right--environmental controls.
QD: As an advisor to international companies and governments, and an honorary member of quality societies in Asia and South America, what do you see as the greatest challenges facing today’s manufacturers and supply-chain members in regard to quality assurance?
JH: We need to stop thinking quality and start thinking value ; value is what customers want, need, and expect. Use quality to drive value, not for quality’s sake alone. Understand the added value to the stakeholders by going from 4 sigma to 6 sigma. Is it better to reduce variation of cycle time or to reduce the average cycle time? Our real challenge is how to provide real value to all the stakeholders, not just the customers and stockholders.
QD: For companies dependent on imported goods, components, or ingredients, is there a way to reliably verify the quality of their supply chain? What sort of quality-assurance procedures would you recommend for such a company?
JH: Supply-chain management, down one level, is relatively easy. Certify the supplier, understand their processes, do frequent audits, and be sure the management team is constant. Information technology systems help with the production status. When you try to ensure the quality of second-level suppliers, this is where the major problems occur. The new supply-chain management approaches and software help, but the best answer is to ensure that the first-level suppliers have an excellent supplier-control process that is working.
Today’s supply-chain experts talk about a supply chain that starts from the basic element all the way through to the consumer’s acceptance. This means that it includes your process, as well as suppliers and sub-suppliers. How can you ask your supplier to be ISO 9001-certified if you aren’t? You may be, and often are, the weakest link in the quality chain.
QD: You have said that “We live in a business environment that is traveling at near light speed. The things that were impossible yesterday are being done today and will be obsolete tomorrow…. The word ‘impossible’ needs to be stricken from our vocabulary. Thinking outside the box isn’t good enough. We need to tear down the walls of the box and build a wall-less culture.” How can businesses best work toward creating such a culture?
JH: We need to have excellent performance in the five pillars of organizational excellence. They are:
• Process-management excellence
• Project-management excellence
• Change-management excellence
• Knowledge-management excellence
• Assets/resource-management excellence
The quality professional has focused on process and even then he or she has only focused on a small part of the job--flowcharting. Probably, what are more important than process flow are information flow and the organizational networks. Simulation modeling is the only way to really understand the problems with your processes.
We have just started to make use of behavior-modification methods. I can do more to improve the organization’s customer satisfaction through knowledge management than through implementing a Six Sigma program.
Why are we reporting dollars saved from Six Sigma programs, not improved customer satisfaction? Is it that customer satisfaction isn’t improving and we are just saving money for the company? We say Six Sigma is designed to improve customer satisfaction, but we report on dollars saved, not improved customer satisfaction. I know of some major organizations that are doing Six Sigma, and their customer-satisfaction ratings are getting worse. What is the quality of your marketing system? Errors in marketing can have more impact upon the customer than the organization’s total quality organization.
Don’t limit your thinking to ISO 9001; that is just the minimum level. If you have won the Malcolm Baldrige award or another national quality award, you have earned 600 points out of 1,000 that you should have reached. You are 60 percent of where you should be. To get the other 400 points, you need a totally new approach.
To be successful, you must excel today. It has been said that to attain excellence you need to:
• Care more than others think is wise
• Risk more than others think is safe
• Dream more than others think is practical
• Expect more than others think is possible.
Have a quality day with a high degree of reliability!
Carey Wilson is Quality Digest’s news editor.
|