by Paul Iannello
Wireless Data Collection
Case Study: Cooper Surgical
Cooper Surgical Inc. was founded in 1990 with a focus on women’s health care. It is a leading company in providing medical devices and procedural solutions that improve health care delivery to women.
In the medical device field, inaccurate data can be a matter of life or death. Any improvement in the efficiency and accuracy of data transfer during product development and testing helps medical device manufacturers ensure that their data, and thus their products, are the safest they can be while maintaining product throughput.
Cooper Surgical is no different. In the past, the company’s quality department was hampered by endless hours of shuffling through part files and folders and manually entering each inspected dimension into analysis software over and over again. To ensure that there were no transcription errors, manual data entry had to be done very carefully. This time consuming and nonvalue-adding task hindered Cooper Surgical’s quest for continual improvement.
The company needed a solution that would provide accurate, innovative methods to enhance data gathering and analysis. Cooper Surgical purchased DC-9005 Data Collectors from I & R Partners. Its wireless networking, integrated barcode scanner and direct gauge interfacing helped the company address its data collection and transfer problems. Shuffling file folders and manual data entry were replaced with barcode scanning, direct network access and the ability to read measurement data directly into a hand-held computer. The time spent on each inspection turnaround decreased twofold with the implementation of a wireless system.
“Not only did we see an improvement on the upfront time investment required for each inspection routine, but we also found great profit in a system that instantaneously uploaded its data wirelessly to our server, making our entire data collection process ‘real time,’” says Tony Branco, a quality engineer for Cooper Surgical. “This is a scenario that is desired by most quality professionals today but rarely attained.”
Wireless data collection has taken Cooper Surgical to the next level of inspection while facilitating its mission of creating and continually improving the quality of its medical devices.
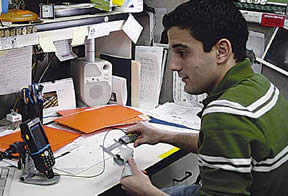
Tony Branco, quality engineer for Cooper Surgical, performs a quality audit while data is wirelessly uploaded to the network server.
|
From pencil and paper, to black-box gauge interfaces, to portable and fixed-station statistical process control (SPC) data collectors, the technology for collecting data for quality control and manufacturing applications has continually evolved to make shop floor data collection more efficient, cost effective and reliable. An obvious benefit of this progression has been an increase in corporate profits along with enthused shareholders.
With the advent of hand-held personal computers (PCs), many new possibilities for data collection have presented themselves. Wi-Fi-capable, hand-held mobile computers are popular because they eliminate the need for running network cables from one end of a facility to the other. Today’s hand-held mobile computers utilize technologies such as Bluetooth and IEEE 802.11 for their wireless capabilities. Such capabilities offer tremendous advantages for real-time data collection.
For instance, real-time wireless data collection can transfer measurement data to a network server so that authorized personnel have access to information to help them make critical decisions regarding process and part quality, even if the measurement is taken at a remote location within the facility or in a hard-to-reach spot on the part itself. Not having to worry about wires opens up real opportunities for measurement.
Some wireless PCs automatically export measurement data to any user-definable location at the completion of a subgroup or set of tasks. With such systems, instant, real-time wireless data collection encompasses both collection and analysis. Users have instant access to trend checking, allowing them to prevent problems rather than dealing with them afterward. Data can be exported to a network server in a format that’s easily imported into various databases or analysis packages, which allows management access to the data for decision making while operators are simultaneously reacting from anywhere on the shop floor.
Wireless data collection isn’t synonymous with wireless gauging. Wireless gauging was actually implemented before wireless networking standards such as Wi-Fi capabilities were introduced for laptops and hand-held PCs. With wireless gauging, one has the ability to communicate between a transmitter attached to a gauge and a receiver attached to a PC some distance away. The advantage with this type of technology is that there are no wires that could possibly be snagged or tangled in tight quarters. A limitation is in confirming the values that are actually sent. Without a visual display, as with a mobile computer, readings and charts are nonexistent. This lack of feedback also means that an operator receives no real-time trending information. This is the primary reason that manufacturers are moving to wireless hand-held mobile computers.
Hand-helds have further advantages. Imagine giving users the ability to roam the plant, scan barcode data for traceability, walk to a station or cell of gauges to automatically collect data and wind up in final inspection, scanning visual defects with a barcode scanner integrated into a hand-held PC.
What if a hand-held data collector could download part programs? Operators might have to collect data and roam to various parts of a plant throughout the production process. Before reaching their first point of data collection, they realize that they don’t have the part program or inspection routine needed. With a few simple keystrokes, they access the network server from the hand-held wireless PC and download the necessary files to execute their application. In the past, that would have involved walking back to an office--regardless of how far and time consuming that may have been--to download the proper part programs. Wireless hand-held PC data collectors allow operators to access an entire library of part programs or inspection routines available on the network server.
The obvious value of wireless data collection is freedom. In prewireless days, the cumbersome task of running network lines to data collection stations was bad enough, but when a new area needed to be added, a team of cabling specialists once again had to shut down the manufacturing area to assemble scaffolds and run overhead wires. With wireless capabilities, once a plant has been set up for wireless, new data collection areas can be added simply by purchasing an additional wireless hand-held PC. Weighing in at a pound or less--just a little larger than a TV remote--and capable of withstanding being dropped repeatedly from four feet or higher onto concrete, industrial mobile computers can be easily carried while data are collected and transferred wirelessly.
A hand-held wireless PC designed for data collection should have some essential features. With the extensive use of barcoding in manufacturing, an integrated scanner is a valuable benefit. This feature gives users the ability to scan everything from part and lot numbers, to operator’s badges, machine numbers, defects, and even production control and material management data. Today’s hand-held industrial PC has other convenient features such as infrared data communication, color touch screen and battery operation for up to 24 hours. A familiarity with the Windows operating system greatly shortens the learning curve for operators.
Validation and traceability are two of the most crucial issues for manufacturers when improving internal processes and resolving customer’s demands for verification. If the method utilized to verify the quality of parts and processes is defective, eventually the manufacturing process will also deteriorate. That’s why any wireless hand-held PC being utilized must have built-in features to ensure that operators don’t err when manually entering data. It’s also imperative that the process resides within control limits. When out-of-control situations occur, the operator must assign a cause for the identified situation and take corrective action. This should take place via the audible or visual warnings built into the system. For further traceability, tags can be utilized for associating data with variables such as operator, lot, shift, and machine and part numbers. Traceability fields are valuable for sorting data during problem solving. A typical scenario would be for a manager to say, “I’d like to see everything off of machine 25, inspected by John Doe, for lot number XYZ.” This kind of information is invaluable in exposing manufacturing problems and solutions. This is where an integrated barcode scanner becomes a tremendous asset; it allows point-and-shoot data entry of all the previously mentioned parameters.
For years the shop floor environment was the environmentally sensitive desktop PC’s biggest nemesis. The hand-held mobile computer requires no fans, thereby eliminating the concern of contaminants entering the mobile computer. Many industrial hand-held mobile computers meet the IP-54 specifications for temperature, humidity, shock, vibration and water.
One of the strongest considerations when constructing a wireless network is the physical environment. Concrete, for example, can hinder wireless transmissions. Lots of metal can reflect wireless transmissions, causing interference. Care must also be taken to understand what other wireless networks or interfering devices may be doing in the same area. Wide open spaces are a wireless network’s best friend.
Ideally, there will be multiple access points (APs) that provide connectivity to the overall network, usually Ethernet. The wireless mobile computer can roam from one AP area to another without losing connection to the network. Each AP has a wireless range that is dependant upon building construction and the proximity of electrical noise-generating equipment.
Therefore, before implementing any wireless network, a site survey should be done to plan the requirements. Fortunately, due to the growing prevalence of wireless networks, from homes to Wi-Fi hot spots, to retail stores, to hospitals, warehouses, factories and beyond, there are many tools and experts to make this task manageable. Further, a wireless network can be used for many other functions besides wireless mobile data collection for quality systems, thus spreading out the cost burden and dramatically increasing the value for use. Often, a wireless network is already established, and the hand-held mobile computer can easily be integrated onto the existing network.
As with anything else, the return must exceed the investment. Industrial hand-held PCs for shop floor data collection range in price from $1,500 to $5,000. This is more expensive than a desktop PC, but consider that some wireless hand-held PC data collectors include SPC data collection and analysis software, gauge interfacing capability, a barcode imager and wireless 802.11 networking. By the time the costs for SPC software, gauge multiplexer, wireless networking card and barcode scanner are added to your desktop computer to match the capabilities of a wireless hand-held PC, you may have matched or exceeded the cost of a hand-held PC.
Other financial factors include the benefit of having immediate access to data with which to make critical decisions. These inevitably result in cost savings due to reduced downtime, scrap, rework and warranty repair. Additionally, hand-held PCs can perform their tasks quicker and more efficiently than the manual paper-and-pencil method, saving more time and freeing manpower for other tasks. When you determine what your current cost of quality is, the question as to whether you can afford such a purchase becomes irrelevant. Quality, like anything else of value, costs money, but compared to losing customers due to lack of production or quality, a wireless system will quickly pay for itself.
When considering a wireless hand-held PC-based data collection system, keep the following in mind:
• Savings. With labor costs rising, any tool that makes an operator more efficient and productive must be considered. Wireless data collection expedites operator responsibilities.
• All-in-one. With integrated wireless networking, built-in barcode scanners, Windows operating system, gauge interfacing and SPC capabilities, today’s hand-held PC is an industry must.
• Customer satisfaction. In an age where companies can contract their work out to a multitude of suppliers, any competitive quality edge is necessary.
• Real-time process improvement. With the SPC traceability analysis capability, the potential for decreasing downtime, scrap, rework and warranty repair is greatly increased. This drives cost justification right to the bottom line.
• Decreased training costs. By using one system throughout the facility, it’s possible to decrease operator training time, increase flexibility in manpower repositioning, allow for emergency borrowing of units, provide single contact support and aid in cost justification.
Paul Iannello is president of I & R Partners LLC. After graduating as a mechanical engineer from the Rochester Institute of Technology in 1982, he started his career in SPC data collection in 1986 with Quality Measurements Systems. He has since worked with various other SPC data collection companies such as Verax Systems, Dataputer and GageTalker. For more information, visit the company Web site at www.iandrpartners.com.
|