Quality Management
Cost of Quality Revisited
by A. Blanton Godfrey
Perhaps it is time we rethought
the cost of quality concept.
Nearly 50 years ago, a new concept was introduced into quality management:
the cost of quality. For many years, this concept has been used to identify
opportunities for significant savings. Increasingly, though, leading quality
professionals argue that the original ideas have outlived their usefulness
and it is time we rethought the whole idea.
Two basic ideas have been used for these many decades. The first is the
idea of an optimum quality level, which is the point when total quality
costs are minimized. The second is the characterization of quality costs
into four parts: prevention, appraisal, internal failure and external failure.
In the early 1980s, researchers like Bruce Hoadley at Bell Laboratories
began questioning the notion of optimum quality levels. Hoadley and many
others, including myself, had discovered too many examples whereby changing
the process radically changed the basic shape of the cost curves and moved
the optimum point dramatically. For example, by implementing modern statistical
quality control methods on the production line and reducing much of the
costly (and often ineffective) final inspection, we could produce higher
quality output at lower costs.
Many people began questioning whether we shouldn't put our energies into
changing the curves rather than trying to find the elusive minimum points.
In 1985, Professor Hitoshi Kume of the University of Tokyo stated that in
the numerous Japanese companies studied, the only ones worried about this
classic approach to quality costs were divisions of U.S. companies. The
Japanese companies focused instead on finding ways to improve quality while
reducing costs.
A second breakthrough in our thinking came when we realized that we could
also change the costs of failures. Although this was not a new idea, in
the 1980s companies began to rigorously look for ways to reduce costs associated
with each failure. By making products easier to maintain or repair, the
cost of each failure could be drastically cut.
The concept of characterizing quality costs into four parts has also come
under fire. Not long ago, brilliant German quality pioneer Walter Massing
chaired a special task force of the International Academy of Quality to
review the basic ideas of cost of quality. At the European Organization
for Quality's Annual Conference in 1990, he reported some of their findings.
The first problem is the term itself. Since quality is so integral to goods
or services, how do we separate the costs of achieving quality from the
cost of producing goods or services? The modern approach has been to concentrate
on the "price of nonconformance" (Crosby) or the "costs of
poor quality" (Juran). But the real problem, Massing explains, is that
trying to minimize the so-called quality costs misses the main issue. What
we want to minimize is the entire cost of production, not one subset of
costs.
This approach has an even larger problem: defining prevention costs. Every
company does numerous things to prevent failures, from market research to
design to choice of suppliers to production techniques and even employee
training.
"If all these items were put under the heading 'Prevention Cost,'
it would soon become apparent that almost all of the total cost of running
the company comes under failure prevention," explains Massing. The
only viable policy is to concentrate on failure costs and to justify prevention
measures for one problem at a time, he notes.
During my days at Bell Labs, we developed an approach to cost of quality
that avoids many of the problems of definitions and accounting nightmares.
We called it the "golden line." We would simply walk the line,
making estimates of true production costs using rough estimates of labor
costs, materials and finished goods inventories, rework, inspection and
so forth.
From this simple estimate, we would subtract the theoretical costs of production.
What if the world were perfect? What if we had no redesigns and each design
resulted in a product that was produced and sold? What if we needed no inspection
anywhere, all purchased goods were perfect, all assemblies were perfect
and we never even had a solder touch up? By looking at the theoretical minimum
compared to the actual costs, we often identified major opportunities that
had never been seen before.
I would recommend this approach as a starting point for every organization.
Next month, I'll cover some other ideas that are having major payoffs in
reducing "costs of poor quality."
About the author . . .
A. Blanton Godfrey, Ph.D., is chairman and CEO of Juran Institute Inc.
Send questions about this column either to the editor or to Juran Institute,
11 River Road, Wilton, CT 06897, by fax to (203) 834-9891 or preferably
by e-mail to godfrey@netaxis.com. Visit Juran Institute's home page on the
World Wide Web at http://www.juran.com.
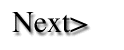