Gages: The Hand Tools of Quality
by George Schuetz
With thousands of gages available,
selecting the right one requires care.
Virtually every manufactured product must be measured in some way. Whether
a company makes automobiles or applesauce, laptops or lingerie, it is inevitable
that some characteristic of size, volume, density, pressure, heat, impedance,
brightness, etc. must be evaluated numerically at some point during the
manufacturing process, as well as on the finished product.
For a measurement to have meaning, an accepted standard unit must exist.
The inspector measuring parts on the shop floor must know that his or her
millimeter (or ounce, ohm, Newton or whatever) is the same as that being
used on a mating part across the plant, or across the ocean. A chain of
accountability, or traceability, connects the individual gage back to a
national or international standards body to ensure this. (See "The
Importance of Traceability," February 1996, Quality Digest).
Measuring vs. gaging
Once the unit of measurement is accepted, some means of comparing the process
or product against that unit must be applied. When the characteristic to
be evaluated is dimensional-e.g., size or location-there are two basic approaches.
The first approach, simply called measuring, involves the use of direct-reading
instruments that count all units and decimal places, from zero up to the
dimension at hand. Direct-reading instruments commonly used in manufacturing
include steel rules or scales, vernier calipers, micrometers and some digital
height stands. Coordinate measuring machines can also fall under this category.
The second approach is gaging, which uses indirect-reading instruments to
compare the work piece against a standard or master-a precision object that
represents a known multiple of the measurement unit. Gages typically start
not at zero but at the specified dimension, and they indicate the size of
the work piece as deviation from the specification. A result of zero on
a gage thus indicates that the part is precisely the right size.
Both kinds of equipment have their roles. The strength of measuring devices
is their flexibility: You can measure virtually anything with a vernier
caliper or a CMM over a fairly broad range of sizes. Gages tend to be quicker
and easier to use because they are designed for more specific tasks. The
gage user generally needs to observe only the last digit or two of a dimension
to know whether a part is within tolerances. And because gages are designed
for use over a shorter range of dimensions, they tend to be capable of generating
results of higher accuracy. Therefore, gages are usually the practical choice
for high-volume parts inspection, particularly where high precision is needed.
Hard and variable gages
Gages fall into two general types: hard and variable-reading. Hard gages
are instruments such as go/no-go plugs and rings (for inside and outside
diameters, respectively), feeler gages (for gaps) and nonadjustable snap
gages (for outside diameters). All are simple mechanical objects that rely
upon no moving parts, and all are very quick and easy to use. But hard gaging
is not amenable to generating numerical results; it tells the operator if
the part is good or bad, but not by how much. It therefore cannot be readily
incorporated into statistical quality control programs.
Variable-reading gages do generate numerical results, and the majority of
dimensional gages are of this sort. Variable gaging incorporates, at minimum,
some kind of display, such as a dial indicator or a digital readout, and
some physical means to detect variation in part size. This is most commonly
accomplished with a mechanical linkage, but other principles such as electrical
capacitance, air pressure and laser reflections are also in use. Variable
gaging includes everything from simple mechanical indicator bore gages and
snap gages, to highly automated in-process gages with electronic transducers
and feedback loops to control production variables, to sophisticated laser-based
gage block comparators.
Variable gages may be further divided into fixed and adjustable varieties.
Fixed variable gages measure manufacturing variation for a specific-size
part, while adjustable variable gages can be set for use across a wide range
of part sizes. The adjustable variable gage must be mastered when part size
changes, however, measurement range is not synonymous with range of adjustment.
Plug gages (such as air tooling, for inside diameters) are fixed variable
gages. Snap gages, ID/OD gages, thickness gages and depth gages are all
available in adjustable versions, as are most other indicator-type gages.
Due to their relative simplicity of construction, fixed variable gages can
measure tighter tolerances and are somewhat quicker and simpler to use.
A separate fixed gage is usually required for every different dimension
that must be inspected. Adjustable variable gages have greater flexibility
of use. For high-volume jobs, where many thousands of identical parts must
be inspected rapidly, or for production runs that are likely to last for
months or years, the additional investment in fixed gaging may pay off.
Where production runs are short or where inspection speed is not an issue,
variable gaging may be more economical because the investment can be spread
over a greater number of jobs.
Measuring vs. gaging, hard vs. variable, and fixed vs. adjustable-these
are just the roots of a rather convoluted decision tree. Because manufactured
parts and manufacturing processes are so diverse, thousands of gage varieties
have been developed. In working with a gage supplier, it is helpful to first
analyze your inspection needs by considering the factors shown in the sidebar.
Mechanical, electronic or air gaging?
Another choice that has become a basic issue within the past few years is
the analog vs. digital question. It used to be pretty straightforward: If
you favored economy, an analog gage equipped with a mechanical dial indicator
was the obvious choice. If the application required extremely high accuracy,
then a gaging amplifier equipped with an electronic gage head was the way
to go.
Now, however, there are digital electronic indicators that are about the
same size and price as dial indicators. Gages equipped with digital indicators
may possess all of the benefits of amplifier gages, including automatic
zeroing and off-set functions, and data export, at a fraction of the cost.
Digital readouts are not necessarily superior to analog dials, however.
Analog displays are ergonomically superior in many applications. For example,
users can observe size variation trends more readily. They also can quickly
sense whether a part is good or bad without having to go through the intellectual
process of comparing the number on a digital display to the allowable tolerance
specification. Some electronic indicators now incorporate analog displays
to replicate this benefit.
Air gaging can offer the best of both mechanical/analog and electronic/digital
gages. Air gages are virtually always fixed gages, built to measure a single
dimension by directing a controlled jet of air against the work piece and
monitoring the back-pressure. Capable of accuracy to within a few millionths
of an inch, air gages may have either analog or digital displays, or both,
and some feature data-output capabilities. Other benefits of air gaging
include: It is self-cleaning, making it appropriate for use in dirty environments
and on dirty parts; it is a noncontact method, so it doesn't mar delicate
part surfaces; and it can be used to gage compressible materials (such as
textiles, film and nonwovens) without distortion.
New trend: Surface finish
and geometry gaging
Typical dimensional tolerances in precision metalworking industries have
decreased by three orders of magnitude since World War II, from 0.002"
in the 1940s to 20-millionths of an inch in the mid-1990s. Some industries
now produce features to tolerances of 2-millionths of an inch. Clearly,
precision in gaging must do more than keep up: It must stay well ahead of
the ability to produce parts to tight tolerances.
But as dimensional tolerances have decreased, a new quality issue has arisen:
Factors of part geometry and surface roughness, once so subtle that they
could previously be ignored, are becoming increasingly important. A flat
surface that undulates by a mere 10-millionths of an inch may now throw
off the accuracy of a part. Gages to measure these characteristics are therefore
proliferating. More and more plants are placing these once-exotic instruments
on the shop floor, where they may soon be viewed as just another part of
the vast and ever-expanding gaging tool box.
Twelve Questions for Dimensional Gage Selection
How do you select a dimensional gage? There are literally thousands of varieties,
many of which could perform the inspection task at hand but not all of which
will be efficient, practical or cost-effective. The first step in finding
the best tool for the job is to take a hard look at the application. Answers
to the following questions will help the user zero in on the gaging requirements.
What is the nature of the feature to be inspected?
Are you measuring a dimension or a location? Is the measurement a length,
a height, a depth or an inside or outside diameter?
How much accuracy is required? There should
be a reasonable relationship between the specified tolerance and the gage's
ability to resolve and repeat. Naturally, the gage must be more precise
than the manufacturing tolerance, but a gage can be too accurate for an
application.
What's in the budget for gage acquisition?
Inspection costs increase sharply as gage accuracy improves. Don't buy more
than you need.
What's in the budget for maintenance? Is the
gage designed to be repairable or will you toss it when it loses accuracy?
How often is maintenance required? Will maintenance be performed in-house
or by an outside vendor? Remember to figure in the costs of mastering and
calibrating.
How much time is available, per part, for
inspection? Fixed, purpose-built gaging may seem less economical than a
more flexible, multipurpose instrument, but if it saves a thousand hours
of labor over the course of a production run, it may pay for itself many
times over.
How foolproof must the gage be, and how much
training is required? Fixed gaging is less prone to error than adjustable
gaging. Digital display is not necessarily easier to read than analog. Can
you depend on your inspectors to read the gage results accurately at the
desired rate of throughput? If not, then some level of automation may be
useful.
Is the work piece dirty or clean? Some gages
can generate accurate results even on dirty parts, others can't.
Is the inspection environment dirty or clean,
stable or unstable? Will the gage be subject to vibration, dust, changes
in temperature, etc.? Some gages handle these annoyances better than others.
How is the part produced? Every machine tool
imposes certain geometric and surface-finish irregularities on work pieces.
Do you need to measure them, or at least take them into consideration when
performing a measurement?
Are you going to bring the gage to the part
or vice-versa? This is partly a function of part size and partly of processing
requirements. Do you need to measure the part while it's still chucked in
a machine tool, or will you measure it only after it's finished?
What is the part made of? Is it compressible?
Easily scratched? Many standard gages can be modified to avoid such influences.
What happens to the part after it's inspected?
Are bad parts discarded or reworked? Is there a sorting requirement by size?
This may affect the design of the inspection station as well as many related
logistics.
About the author . . .
George Schuetz is marketing manager, gaging products, at Federal Products
Co. In Providence, Rhode Island. Federal Products manufactures and markets
a wide variety of precision gaging products, ranging from dial indicators
to sophisticated dimensional, surface finish and geometry gaging systems.
For additional information, contact: Marketing, Federal Products Co., 1144
Eddy St., P.O. Box 9400, Providence, RI 02940-9400. Telephone (800) FED-GAGE
or (401) 784-3100. Fax (401) 784-3246.
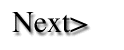