Still Targeting Perfection
In 1981 I was working for an aerospace company in a position known as "head, total quality systems." Total quality systems (TQS) was a precursor of both total quality management (TQM) and Six Sigma. The role was created by my employer's vice president of manufacturing after he and his staff, at my behest, attended a seminar held by W. Edwards Deming. Their experience at the seminar was quite unpleasant because they made two mistakes: They let Deming know they were senior managers of a U.S. company, and they sat in front.
After the seminar they decided to reconsider their approach to quality, although they weren't sure what to do. TQS was created to help them find the answers. Our mission was to research best practices in quality, identify those with potential and promote the use of these promising technologies within the organization. We enlisted the vice president and his staff as a steering committee and obtained a list of opportunities to address. Projects were chartered, each with a senior leader acting as a sponsor. Most project teams included a person with a master's degree in an engineering discipline, including several statistics courses. The projects were wildly successful, as would be expected when the fruit wasn't just low-hanging but lying on the ground in piles.
Although the TQS approach bore similarities to Six Sigma, there were many important differences. The figure below lists a number of differences between the quality environments of 1981 and 2006. Two of them are critical. First, in 1981 the highest level of leadership that one would find actively involved in performance improvement was a vice president. The CEO supported the vice president, but that support was generally passive. There were exceptions, of course; Ford Motor Co. president Donald Petersen was perhaps the most noteworthy. Petersen took Ford from three sigma to four sigma in less than five years and restored the company's profitability as a result.
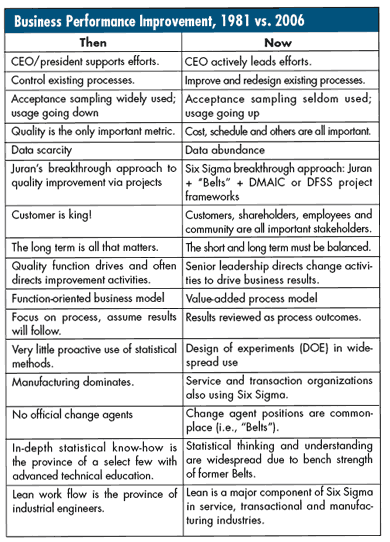
Second is the development of a well-defined project framework. Motorola started with measure- analyze-improve- control (MAIC), which helped take the company all the way from the brink of bankruptcy to a Baldrige Award in just a few years, sans Green Belts and Black Belts. General Electric added "define" to the framework and gave us the DMAIC approach that dominates Six Sigma today.
People who have learned the Six Sigma approach think differently. When the CEO thinks differently, the rest of the organization soon follows. Business schools will begin teaching the Six Sigma way of running an organization instead of old- fashioned command-and-control management. Organizations that don't get on board will find themselves at a severe competitive disadvantage. Evolution will do the rest.
Thomas Pyzdek, author of The Six Sigma Handbook (McGraw-Hill, 2003), provides consulting and training to clients worldwide. He holds more than 50 copyrights and has written hundreds of papers on process improvement. Visit him at www.pyzdek.com.
|