by Cliff Veach
Depending on which vertical industry or department you work in, the definition of "asset management software" can vary widely. From a maintenance perspective, names such as DataStream, AssetSmart, Mpulse and eMaint might come to mind. If, however, your primary focus is on compliance issues such as calibration, then you might think of Blue Mountain, Cebos, Cybermetrics and ASI DataMyte.
The broad applicability of asset management has encouraged a tendency for individual departments to purchase or develop point solutions for their particular needs. This shortsighted approach limits the opportunity for strategic analysis of the service-and-support capabilities protecting your most costly assets, and ignores the cross-dependency of many assets and services during their life cycles.
This article discusses the need for an integrated asset management system and the considerations involved in taking such a step. It also examines existing technologies that allow such an integration to take place. The term "asset management" is limited here to manufacturing environments, including all production-process assets such as mechanical machinery and tooling, maintenance equipment and parts inventories, test and measurement instrumentation, gages, and any other assets used to support the manufacturing process.
Although most legacy software systems on the factory floor focus on repair, changeover or calibration, it's important to remember that an "asset" is the core element, and service and support tasks are merely activities or events that contribute to documenting the overall cost of ownership, system governance, maintenance and compliance programs.
Companies invest millions of dollars in assets for production facilities, including manufacturing machinery, test equipment and human capital. Consolidating real-time and historical
service data from the disparate software systems that manage assets can help optimize an organization's potential in the following ways:
• Increase production volume predictability
• Reduce machine downtime and increase productivity
• Synchronize activities to decrease redundant costs
• Increase turns of mission-critical parts inventory
• Reduce standing parts and consumable inventory
• Reduce redundant software and database systems
For example, if a specification or work instruction is required to perform a task within one system, it shouldn't require re-entry or manual cut-and-paste to another application database to make it visible to that application. Common procedures and specifications should reside in one place and be available to all other applications that need that same data. Cost savings can be realized by eliminating redundant data-entry operations as well as by increasing data reliability.
By consolidating redundant information and selecting software systems that track activity-based costs around the asset itself rather than the type of work being performed, an organization will increase cost-reduction opportunities across multiple disciplines in the asset-management process. The company might actually reduce the number of software applications, databases and administrative resources required to maintain a healthy asset program.
From a software-technology perspective, the process required to keep tactical assets of any type available and functioning are basically the same, regardless of the type of service or support activity being performed. The process includes:
• Identifying the physical asset that requires service activity
• Specifying the activity to be performed and who shall perform it
• Providing the task-specific information required for success
• Providing necessary supplies and/or equipment
• Managing the information and/or resources during the process
• Documenting the process and assessing related effects
• Analyzing opportunities to prevent negative recurrences
The more asset life-cycle data are centralized and made available to all support personnel, the more efficiently they can assess a situation and execute their duties based on facts. This results in a positive, cost-effective outcome.
Lab and calibration systems, for example, don't always have access to preventive maintenance or line-changeover schedules. The lack of manufacturing visibility to the calibration lab prevents it from easily synchronizing calibration schedules to minimize equipment downtime and avoid duplicate or redundant effort for activities that could have been scheduled concurrently.
When internal facilities operate as suppliers or customers of one another, it's good business to synchronize preventive downtime across facilities to avoid soft spots in production performance that could affect other facilities' production capability, delivery and profitability.
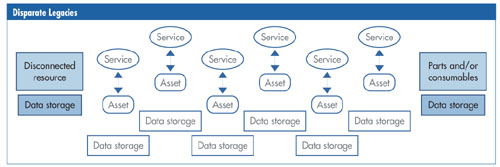
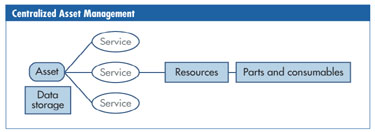
Before considering any new software solution, you must first understand your asset management requirements across the entire organization. For each type of asset (e.g., equipment, gage, personnel, vehicle, etc.), you must address the following:
• Asset tracking. Where will the organization manage and track data about a particular asset? What's the primary information system (i.e., application) used to manage this asset? Is this system capable of maintaining the overall asset life-cycle management data?
• Operations and service . Review each
service-and-support software system for data and compliance requirements for internal governance, customer audits and regulatory issues. Focus on redundant data elements and administrative tasks, and develop open architecture that allows for easy data exchange with other third-party applications. This is a key to reducing administrative redundancy on the factory floor.
• Systems that support services . Create an environment that will promote
"enterprise-asset awareness" vs. departmental ownership. Think outside the box (or department) and analyze service inventories by use, owner, location and critical response requirements such as maintenance or changeover consumables, tooling and equipment standards used for calibration. Separate the more predictable services from those that are ad hoc, critical and unpredictable. The goal is to automate events that can be eliminated from the administrative workflow and thereby reduce resource drain.
Many new technologies now provide the ability to access and consolidate data and information in disparate application databases. This allows us to leverage legacy data to serve new investments in software. Such rules-based technology tools offer open access to, and data-mining capability from, almost any ODBC-
compliant or SQL database; some even offer data extraction from ASCII files and proprietary databases.
These tools come in a variety of packages, from Microsoft's BizTalk Engine, whose application capabilities include establishing rules for initiating decision support activities, to more analytically focused, executive dashboard-development tools such as eServer by Statware, which specializes in analyzing custom data sets derived from data extracted in real time from multiple application databases.
By using XML "triggers" when data are altered, the BizTalk engine is capable of enforcing the exchange of data requirements between applications such as maintenance, repair and operations (MRO) software, and calibration software to eliminate manually re-entering and updating asset information. Any new asset or updated information can be entered automatically into any number of application databases containing the identical field requirements for data.
The eServer could be configured to identify and analyze trends or potential conflict issues across processes or within multiple applications. Examples include synchronizing activities relating to a single asset or assessing machine downtime for root cause and preventable redundancy. The software can be customized easily to assess the probability of redundant downtime between several independent application schedulers that might require machine shutdown for service, and even notify and recommend synchronizing activities to the appropriate parties.
These enabling technologies automate the process of information flow, or redundant administration, based on existing data or what can be extrapolated from them. These tools also support basic auto-
decision making and notification to responsible parties when a consistent outcome is observed based on the analyzed data. Whether the technology is considered a reporting tool, dashboard or data-mining engine, the primary goal is providing contextual information where you need it, when you need it. Suppliers that develop these technologies are usually willing to demonstrate their capabilities using the customer's internal data sets.
Any outsourcing service carries with it the inherent risk of decentralizing necessary compliance information and making financial or compliance audits more complex, costly and time-consuming than necessary. In no arena is this more apparent than outsourcing instrument and gage calibration, and the service and/or repair of electronic and mechanical equipment, including warranty service contracts.
Every supplier that performs a service generally offers to provide, via Web interface to its systems, necessary compliance documentation such as calibration certificates or detail sheets of work performed. Unfortunately, by its very nature, outsourcing distributes a client's service data to other systems beyond its control. Retrieving the necessary documentation (not necessarily with supporting data) must be done on the client's time from data stored off site. From a comprehensive, asset life-cycle management perspective, this method offers no analytical capability or correlation to the organization's involved assets. From a system perspective, outsourcing can be a less than optimal, sometimes even counterproductive, method of data collection that could expose an organization to higher risk and additional costs while offering less visibility and control.
The answer lies with an overall asset service tracking and management philosophy, similar to that of Dynamic Technology Inc. of Hartland, Michigan. A premier service provider for outsourcing calibration, service, and repair of electronic equipment and instrumentation, DTI enjoys relationships with more than 80 percent of the top 50 automotive manufacturers, primarily due to its unique total asset management approach to service.
When faced with providing the best possible service to its world-class clientele, DTI asked its internal development staff to find a method for leveraging its sophisticated cross-functional software technology to accommodate its customer base. DTI has combined calibration, service and repair management into a single, asset-specific service focus, so that all data regarding a specific asset, including the supporting documentation, is available online, in a single history, with associated costs and raw data components available for download to the customer's site for review and analysis. This asset life-cycle information capability is available to all DTI customers.
DTI's online service also provides customers with the ability to use the DTI online software to facilitate the same high level of service and compliance tracking at their own facilities for equipment and machines outsourced to other service suppliers. This allows customers to consolidate all their asset service and repair activity in one database for future auditing and analysis, without investing in new internal servers and software. By using their own Web browsers to access the DTI system, the company's customers get the same level of service as that provided by multiple legacy software systems, for a price much lower than what it would cost to maintain those systems, not to mention the resulting time saved performing internal or customer audits when all the information is stored in one place.
The DTI system offers not only centralized service data for the assets it manages for customers, but also provides an additional capability for consolidating other service data on these managed assets, such as internal preventive maintenance or mechanical repair and/or overhaul that are part of the assets' overall life-cycle history. All data are stored in one system for easy access, review and analysis. Moreover, having a consolidated asset-service management system reduces the need for operators to learn multiple systems for calibration, service or repair activities.
DePuy Orthopaedics, a Johnson & Johnson company, recently identified cost-reduction opportunities within the process that distributes and manages its service inventory and tooling supplies. All consumable inventory was dispersed from a central crib area, requiring multiple resources and excessive inventory for stock outs and potential machine downtime issues. In addition, operators created their own "private stock" inventories for tooling, which skewed the true consumption numbers, making accurate assessment and reordering almost impossible. Machines had to be shut down two or three times a day for trips to the crib area, and with more than 200 operators, this added up to a serious loss of productivity. To reengineer the consumables supply process, DePuy's management team set five basic goals for improving the process:
1. Reduce machine downtime due to operators waiting for tools and/or supplies.
2. Ensure around-the-clock access to all materials and supplies.
3. Reduce on-hand inventories and eliminate private-stock overages.
4. Require increased accountability from employees for tool and/or supply use.
5. Substantially increase reporting accuracy for replenishment and purchase.
DePuy selected its largest internal business unit to pilot a point-of-use dispensing solution by DispenseSource Inc., a full-service solution provider of Web-based systems for managing service and support inventories.
The pilot system was set up to provide operators with 24/7 access to the tools and supplies required to do their jobs from a series of networked dispensing cabinets installed in their own departments, thus eliminating the time spent walking to the crib. The networked units provided accurate, up-to-the-minute inventory control numbers directly to purchasing and accounting, and extensive reporting capability for management review.
In addition, the system's Web-based executive reporting and real-time data integration capabilities allowed DePuy to leverage its legacy purchasing system, automating the purchasing process for all supplies and tooling dispensed from the point-of-use cabinets by issuing replenishment orders directly to the relevant supplier through a Web-enabled link. As inventory levels reached replenishment thresholds, the supplier would be notified automatically to initiate a shipment against its blanket purchase order, which in turn triggered the supplier payment process with notice of shipment. The loop was closed by automating redundant activities between applications.
After a three-month pilot test, the results were impressive:
• Standing inventory time was reduced from three-and-a-half months (representing approximately $119,000) to slightly less than two months (approximately $81,000) during the pilot, and continued to decline to less than two weeks after the rollout.
• Machine downtime fell from approximately eight hours per week to less than two hours per week during the pilot, and continued to fall to less than one hour per week after the rollout.
• Out-of-stock adjustments and resulting "response orders" fell from more than 600 per week to less than 100 per week, and continue to decline.
• The purchasing department significantly reduced the hours required to administer the process by automating the supplier interface.
After three months, the pilot program had outperformed expectations. "Any skepticism as to whether the point-of-use cabinets could make a real difference faded after less than two months," says Dick Perry, DePuy's manager of strategic MRO. Perry credits the system with an ongoing reduction in tooling expenses of nearly $250,000 per year, in addition to a return on investment several times that which the company expected.
Traditionally, each department or functional unit had its own method of monitoring asset management, with little or no data-sharing, automated or otherwise. The result was a task-driven asset-management system that provided no overall view of an asset's life cycle.
Technological solutions are available for creating asset-management systems that provide complete asset life-cycle visibility and that also integrate data from an organization's legacy point-solution asset software into one dashboard. In addition, technologies such those produced by
DispenseSource allow for automated asset handling and procurement.
Production asset management is becoming an integral component of business strategies to achieve competitive advantage and stakeholder value, and therefore any undertaking to develop an asset-management system must be based on sound business principles coupled with sensible technology investments.
Effective asset-management systems have strong business justifications, with returns often measured in the range of ten times cost. In addition, the residual benefits of using a flexible, scalable system that can evolve with an organization's individual needs will far surpass the original savings from the core technology.
Cliff Veach is a well-known functional software design and marketing strategist whose design concepts have won several notable industry awards. A contributing author in the areas of asset management, performance optimization and supplier-quality relationships, he co-authored the SME Blue Book on Technology Trends for 21st Century Manufacturing. Veach has also served for several years as an executive advisor to the Computer and Automated System Group (CASA) of the Society of Manufacturing Engineers (SME). He's currently a manufacturing systems associate with Latitude Consulting Group
|